The future of automated rail transport
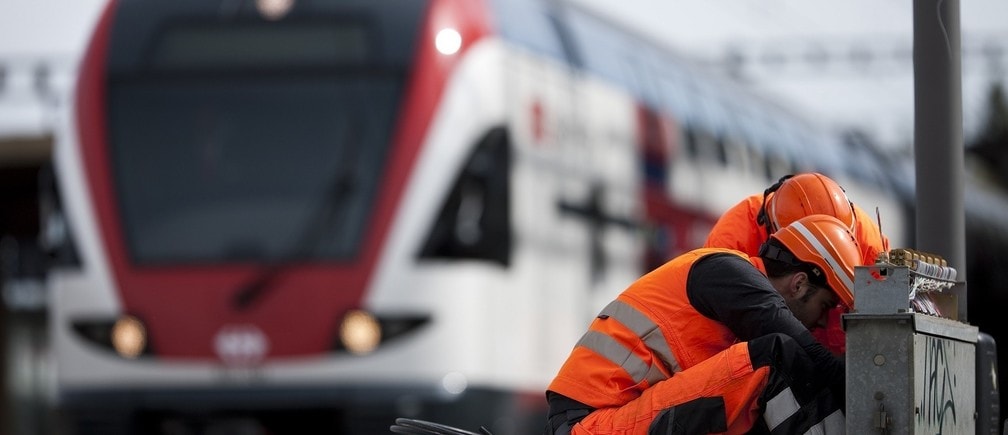
Stay up to date:
Travel and Tourism
Key takeaways
- Pilbaran train drivers earned an average of A$210,000 in 2013—the result of the remote location and the need for a high degree of technical skill to safely transverse the diverse topography while carrying such heavy freights, according to BHP.
- In response to competitive pressures, Australian iron ore producers have increasingly turned to cost-cutting measures, including train automation.
- Leading the way in rail automation is Rio Tinto, which has invested US$518m in the effort and has begun testing automated trains this year with the hopes of fully implementing the world’s first automated heavy-haul rail network in 2015.
China’s booming economy has strongly driven up iron ore prices since 2002; China’s current iron ore appetite is sated only by consuming roughly 67% of all seaborne iron ore exports. Such demand has breathed new life into mines from northern Brazil to Minnesota’s Iron Range but nowhere has this ferrous renewal been more pronounced than in Australia—the world’s largest exporter—where production has boomed from 188m tonnes exported in 2002-2003 to 556m tonnes exported in 2013. Getting that ore from the mines to processing facilities or export points like Port Hedland—the world’s largest iron ore port—is none too easy, however.
The Pilbara region, where 94% of Australia’s iron ore is located, has scarcely any population—in 2010, its population density was less than 0.1 person/square km. Pilbara temperatures can reach 130 degrees Fahrenheit, infrastructure is minimal and, with a social scene mostly dominated by kangaroos, difficulties abound in finding and retaining mine workers and the workers needed to transport the ore—resulting in high labour costs.
Compared with its primary iron ore competitor, Brazil, Australian labour costs are substantially higher. In 2012-2013, an Australian mine worker earned US$137,100, while his Brazilian counterpart earned US$76,800. Similarly, BHP Billiton reports that Pilbaran train drivers earned an average of US$190,694 in 2013; they bring a high degree of technical skill to this remote location—necessary to safely transverse the diverse topography while carrying such heavy freights.
In response to these pressures, Australian iron ore producers (BHP, Rio Tinto, and Fortescue, which, together with their subsidiaries, were responsible in 2011 for 91% of Australia’s iron ore production) have turned increasingly to cost-cutting, especially by improving their trains and private rail networks that freight the ore to port. In a context of high labour costs, the more automated the better.
Leading the way in automation has been Rio Tinto, one of the world’s three largest iron ore producers alongside BHP and Vale. Rio has invested US$518m in the effort and has already begun testing automated trains this year with the hopes of fully implementing the world’s first automated heavy-haul rail network in 2015. Helping it create this rail system are GE and Ansaldo STS. The former will provide its “Evolution Series” locomotives—which can run 1.4-mile-long trains pulling roughly 26,000 tonnes of iron ore freight, according to GE—while Ansaldo has been developing an automated train management system. The system, which began testing this year, would allow Rio to run driverless trains across its rail network, eliminating the need for upwards of 500 drivers and delivering a savings of more than $100m annually.
Others have followed suit. Fortescue, for example, is developing its own integrated train control system for its network based in Perth that will track its trains via GPS and digitally deliver operating instructions. BHP, however, has indicated that it would prefer to allow others to develop automated train technology and then adopt the second-generation technology when it becomes available. Vale, however, relies on a multi-user railway and cannot turn to automation as easily. It therefore decided to cut costs in its Brazil operations instead, investing US$20bn in a project that will build a railway through the Amazon and replace mining trucks with a 23-mile-long conveyor belt in the hopes of reducing mine-to-port costs.
These cost-cutting efforts are needed: iron ore prices have been falling recently amid rising doubts over the continued power of China’s growth engine and rising global iron ore supply (Morgan Stanley expects Australia to double its iron ore exports from 2010 to 781m tonnes by 2017). These dynamics brought the price to a five-year low of $84/tonne in September 2014, putting pressure on high-cost producers.
For the lucky few that already enjoy low-cost production, ramping up production will enable them to maintain absolute profit levels while forcing competitors out of the game by driving prices even lower over the short term. One the best positioned to pursue that strategy in Australia may be Rio Tinto: at a cost of US$44/tonne, it has one of the lowest price points in the industry—in no small part because of the riches of the Pilbara and the investments Rio made in its railway networks.
This post first appeared on GE LookAhead. Publication does not imply endorsement of views by the World Economic Forum.
To keep up with Forum:Agenda subscribe to our weekly newsletter.
Author: Drew J. Hart is a writer for GE LookAhead.
Image: Employees of the Swiss Federal Railways perform maintenance operations in front of the new regional two-floor train connecting Geneva and Lausanne before its inauguration trip in Romont, April 26, 2012. REUTERS/Valentin Flauraud.
Don't miss any update on this topic
Create a free account and access your personalized content collection with our latest publications and analyses.
License and Republishing
World Economic Forum articles may be republished in accordance with the Creative Commons Attribution-NonCommercial-NoDerivatives 4.0 International Public License, and in accordance with our Terms of Use.
The views expressed in this article are those of the author alone and not the World Economic Forum.
Forum Stories newsletter
Bringing you weekly curated insights and analysis on the global issues that matter.
More on Industries in DepthSee all
Cathy Li and Andrew Caruana Galizia
March 3, 2025
Francesco Venturini and Bart Valkhof
February 27, 2025
Joe Myers and Madeleine North
February 19, 2025
Minos Bantourakis and Francesco Venturini
January 21, 2025
Pawan Goenka
January 20, 2025
Maria Alonso
January 19, 2025