Is the reshoring of US manufacturing a myth?
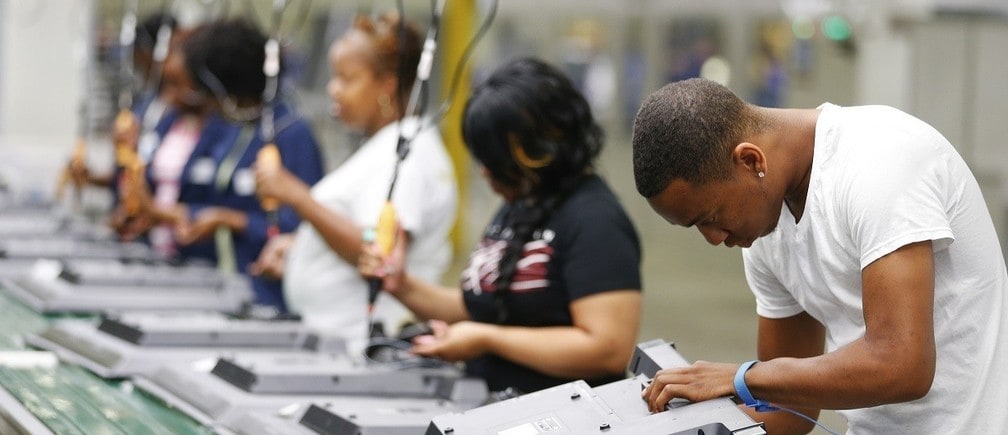
Stay up to date:
United States
here’s been a flurry of news reports suggesting that U.S. corporations are bringing overseas manufacturing back to the United States, notably from China. The reason for the reshoring: As labor costs rise in China and other emerging markets, the advantages of lower wages recede. But new research by Morris Cohen, a Wharton professor of operations and information management, and Hau L. Lee at Stanford, shows the reality is more complicated. There is actually little reshoring on a net basis in the U.S., while supply chain movements are crisscrossing more than ever. Even within the same company, one department might be outsourcing while another is reshoring. In this Knowledge@Wharton interview, Cohen outlines the key findings from of the study, “Global Supply Chain Benchmark Study: An Analysis of Sourcing and Re-structuring Decisions.”
An edited transcript of the conversation appears below.
Three Fundamental Questions
I’m engaged now in this very ambitious research project, a benchmarking research project with a consortium of other universities to address three fundamental questions about the sourcing of manufacturing on the global scale. We’re interested in first, what are companies doing? Where are they sourcing manufacturing? Are they changing the locations, the countries where they’re sourcing manufacturing? Years past, many went to China and low labor cost countries in Asia. And we’ve seen changes in relative labor costs. And there have been predictions that we’ll see an immense amount of reshoring. And yet, on the other hand, we see major restructuring going on.
There’s confusion as to what companies are doing.
Second is why a company is doing it — what are the main reasons for doing this? Is there some dominant reason, like labor costs or technology? Or does it depend on exactly where they’re going, who they are, what technology?
And the third, which is the hardest question to answer, is: What is going to be the impact of this in terms of jobs, in terms of economic efficiency, in terms of growth and market share? That is what we’re trying to address — to give it a sound empirical basis by benchmarking leading companies all over the world and asking them, based on the actual decisions that you have made in the last two or three years affecting the sourcing of manufacturing, tell us what you’ve done, why you did it and what the impact either was or is expected to be.
So, it’s been very gratifying. We initially did a pilot study in China where we got 50 companies to respond. And we’ve analyzed that data and we’re writing that up and it’s going to be distributed. We then created a consortium of seven leading universities with leading global supply chain scholars, people who work in this area who are all working together and we started the initial phase.
‘Unprecedented’ Restructuring
Number one, there is an unprecedented amount of restructuring going on. Companies are addressing the question of how and where to produce products, and they’re opening factories, they’re closing factories, they’re shifting employment. So, there’s just been a lot of change going on.
Number two, that change is not in one direction.
Not everybody is reshoring back to the U.S. or to Europe. Not everybody is offshoring again to Asia or to China — South America, Eastern Europe — every part of the world is engaged. We see companies making a range of decisions for what seems to be a variety of reasons. So, there’s a lot of change, but it’s a very complicated picture. We need to understand where it’s happening and why it’s happening.
‘It’s Not a Simple Flow Back’
So far, what do the preliminary results indicate?
First of all, it seems pretty clear that predictions of wholesale reshoring back to market related countries like the U.S., Canada, Europe is not happening on a large scale. It is happening. And in selected industries, it’s a major thing. But just as much as companies are returning, there are other situations where companies continue to offshore, either to Asia or to other parts of the world.
So, that is the number one headline — that it’s not a simple flow back. There’s a complicated pattern of flows that is occurring. Some are leaving, some are coming, some are going to different locations. I’d say that was the main observation.
The other thing is, we asked for the drivers of these decisions and we offered a variety of possible choices. And we had about 20 possible different factors.
We had very unique way of pursuing this in the benchmark. It’s very difficult to ask a company the question, ‘Where should you be producing your product?’ Just think about that. That’s a very complicated question. It involves all parts of the company. There are many players involved and companies make multiple decisions. So, we saw companies were sometimes doing what looked like contradictory things. While they were going in one direction they were also going in the other direction.
We decided that the only way we could get a handle on this was to use as a unit of analysis the decision. What decisions have you made? Give us examples of decisions and explain to us why you made that decision. And so, our observation is based on a sample of decisions drawn from these companies, which is a very different way of doing a benchmark — asking the company: “What are you doing? What are you thinking? What are your priorities? You made a decision. Tell us why you made it.”
And that gave us the ability to ask much deeper and more nuanced questions, and we learned a lot from that.
‘Opposite’ Decisions:
I don’t think I was surprised that reshoring was dominant. Other people have noticed this already. What surprised me was that companies were making oftentimes what seemed to be opposite decisions. I’m going to go to China. I’m coming back from China. The same company simultaneously making what seemed to be opposing decisions. And when you asked them why, they would give the same reasons. It’s because of labor costs. It’s because of market access. It’s because of this and that.
And this at first surprised us. And then we thought about it and said, well no, we understand this.… We have modeled global supply chain strategy decisions for a long time. I’ve worked in this problem over the years. And the conclusion — it’s not an easy conclusion to express — but companies seem to be going through very complex or at least involved trade off and risk analyses. They’re taking into account multiple factors. And depending upon what is dominant in a particular case for a particular product, it could push them in one director or the other direction. They’re doing all these different things because they’re evaluating these decisions and they’re making tradeoffs because they can no longer view it as a no-brainer. They have to use their brain. They have to analyze this problem.
And so, what I saw, which I think it was surprising and I think gratifying, that the level of analysis that seems to be going on is actually quite deep.
No Dominant Reason:
I think the main misperception is — there is no one, dominant reason. The one that everybody talks about is labor costs. Our labor costs are not going up and therefore this is going to drive everybody back [to the U.S.]. A lot of people have proposed that.
Another one is: It doesn’t matter what labor costs are because everything’s going to be automated. So, the robots are going to make the product. It doesn’t matter what the human labor cost is. We found that it’s not that simple.
Another thing that surprised us is that places like China and Asia, and parts of South America, have become very attractive, not just because of low labor costs but because of high quality, because of access to markets. That seemed to be a major driver.
A lot of companies are going into China, not so much because they want to save money but because they want to have access to that huge market. And the only way they can have effective access is to be there on the ground. So, these are all valid reasons and once you look at them it doesn’t surprise you that this is happening but it’s not just chasing a low labor cost or getting rid of labor and using robots. It’s not that simple — and some of these developing countries are attractive for reasons like quality and market access, which we normally don’t hear about so much.
A ‘Wave’ of Restructuring:
[A] wave of restructuring … is definitely occurring — every day, you see press releases from companies saying we’ve shifted our production from country A to B. This is happening and it’s continuing to happen. And governments are continuing to put pressure on companies to bring jobs home, to bring activity home, and the stakes couldn’t be larger and the issues have become more and more focused.
I think that this problem — not that it has ever gone away, it’s always been a part of overall strategy — is going to continue to be with us. As we see technology developing, as we see markets evolving, as we see different labor forces going through different demographics and having different prices, companies are going to have be, on an ongoing basis, evaluating these decisions and preparing to make changes. That’s the main takeaway at a practical level.
The GE Story:
One of the most publicized stories has been the General Electric story having to do with appliance manufacturing in Kentucky. Not many years back, GE decided to more or less shut down that activity at Appliance Park, which was the major manufacturing center for appliances. This is the white goods appliances — refrigerators, stoves, things of that sort. They shifted it overseas to Asian countries.
And they announced with great fanfare that they were, I think, going to invest a billion dollars in reopening those plants and hiring American workers and reshoring. It was one of the major examples of the reshoring phenomenon. And things have not gone so smoothly. There was a recent article I think in the MIT Sloan Management Review by Professor [Willy C. Shih] of Harvard evaluating the bumps in the road that GE has encountered in trying to do that. When they hired [workers], after three days they had to fire them because they said, “This is what you want me to do? I don’t want to do this.”
So, they had enormous turnover. People aren’t trained to think that way anymore. So, will we ever go back to where we were? I don’t think so. But at the same time, we have new technologies and new products and new opportunities. So, I’m not pessimistic about the opportunities for the future, but they’re not going to be based on what we did in the past.
The GE story is quite instructive. They had trouble finding skilled workers, retaining those workers. There was a big issue of labor costs. The union made major concessions so that [GM] could hire people to enter at wage rates that were lower than they normally would have required, otherwise it wouldn’t have worked.
In spite of that, it’s been a tough go. That’s one instructive example — that it’s not so easy to pull this off and there are a lot of issues to look at.
The Role of Labor Costs:
When you take your iPhone from Apple, labor cost is clearly under 10%. And so, you could argue it doesn’t really matter what happens to the labor costs in China or Thailand with respect to their cost of the product. It’s more important that they can develop new products and have access to flexible, high-capacity, high-quality manufacturing. And that the actual labor cost — it’s not that it’s insignificant, but it’s not the most important factor.
On the other hand, take the apparel industry, which is labor-intensive. To this day, we see Chinese companies outsourcing to Vietnam because labor costs in Vietnam are lower than in China. And this is what we’ve seen in our surveys. We actually have results that show Chinese companies are going from the coast, where the cost of living and wages are high, to the interior, where it’s cheaper.
They’re not leaving the country, they’re just going to another place. And so, it depends very much on what the product is, what the cost composition is, what type of technology. We found in our survey that these kinds of factors, either for the product or the technology, are significant. And different answers therefore are generated in different industries…. Labor costs may drive me if I’m in the apparel industry, but if I’m in a high-tech industry, not so much.
On the other hand, take aerospace and defense, another industry we looked at. There are companies like Rolls Royce, which only makes products in the highest labor cost countries in the world — the U.S., Great Britain and Norway.
I’m talking about aircraft engines and marine products. They’ll argue that that’s where they have access to the skilled labor and that they couldn’t find the labor that they needed in other countries, even if the wages are lower. So, labor is also probably not a major component of the cost of building an aircraft engine, but you’ve got to have skilled labor. It becomes essential.
So, again, it illustrates how the trade-offs come into play and how industry and product and technology factors become very important.
Labor and Location:
One interesting thing we observed in our survey is that companies in capital-intensive industries in some cases are moving their production into China. And to some, that may be viewed as counterintuitive, because you think of going to China and Asia as places where labor costs are more are dominant, and that for capital-intensive products for the advanced technologies — these aren’t the places that you would go.
Part of the explanation for that is you can no longer view countries like China — or Brazil, for that matter, or countries in Eastern Europe — as being places where you have unskilled labor. They have highly skilled labor. Twitter And they’re very anxious to expand into these high-tech industries. China is investing billions to build up its aerospace and defense industries. For example, in commercial aircraft, they’re competing directly with Airbus and Boeing for regional jets — at least they’ve announced that they’re going to do that. And so, there are highly skilled labor forces now in places like China. And they may be cheaper and they may be just as good. So, we can no longer fall back on this comfortable notion that well, when it comes to these types of jobs … we have to be in these highly developed countries because that’s where we find our labor. Some of their competitors don’t agree with that. Sikorsky is a company that has gone the other way.
And so, it’s just fascinating how in the same industry with the same products and the same technologies, some will choose to go in one direction and some will choose to go in the other direction. That suggests that their local evaluation of the trade-offs might be different. They may have other factors, other constraints, other reasons for making those decisions.
Is the Reshoring Trend Very Strong?
Apple’s another interesting case in point. They have announced and they have started producing some computers back in the US. Remember, when they started they had one factory in California and then they built a second factory in Texas, and then they expanded. They would argue that they were an American-made product, even though 90% of their cost of goods was imported parts, even then. So, most of Apple’s products are made offshore for all the reasons we discussed. Yet, they have done this project where they’ve taken certain high-end computers and are now manufacturing them in the U.S.
It’s a very small fraction of their total activity. It’s a very small fraction of their total capital investment. It’s gotten a disproportionate amount of publicity. They can point to that and say, we’re doing the right thing, we’re reshoring. So, skeptics would say that there was a political motive. I don’t know. But I think objectively, that’s certainly not the dominant thing they’re doing. So yes, everybody’s doing some of it but is it a major sea change for them? I don’t think so.
Ethical Questions:
We have in many manufacturing industries, where products are assembled, the use of contract manufacturers. Contract manufacturing is where you outsource production to another third party. They build your product in their factory with their workers. Some of them, like Foxconn and others, I think have — like Foxconn has over a million workers in China. And they make in the same factory competing products. So, you will see laptops with two different brands competing coming down the same assembly line.
That is the nature of global supply chains. You search the best source of supply and very often it might be the same source for your competitor as for you. And so, these contract manufacturers have become very large and a major player in certain industries, especially where you need assembly of piece parts, where you need fine motor control. And so, what they’ve done is they would hire young people, young women who have good eyes and hand coordination and motor skills, and they can put together little pieces and assemble them.
There have been a lot of terrible situations — suicides, people going home for the holidays and not coming back, all kinds of disruptions, arguments that they’re mistreating their workers, they’re not paying them well. And this has led some of the customers to impose ethical standards on their suppliers. We, of course, see the same thing in the apparel industry with the use of child labor and unsafe work conditions in [developing] countries.
Ethical Responsibilities:
So, what’s the ethical responsibility of the company that outsources to another company, maybe in another part of the world, to maintain standards that we would think are minimal in our country? This is a very complex question. But it acts as a kind of an additional constraint, if you will, or an additional incentive to either go or not go to certain places, or to control how you do it. So, even some of these contract manufacturers — like Foxconn, which has over a million workers in China, has stated publicly that it wants to replace them with a million robots. Now, they’re not going to do that but it was an interesting statement that they view that one of the ways to solve these ethical problems is get rid of the people.
Robots don’t complain about work conditions. We used to talk about “lights out” factories with robots. You don’t need to have the lights on when the robots are working. So, I don’t think it’s going to replace [a human workforce] but I think that there’s going to be a rebalancing and a different, increased role of technology. But it affects these sourcing decisions in some cases in a major way. It needs to be considered as part of an overall evaluation of where to go and how to go there.
What’s Next:
We got about 35, 40 companies and we held a meeting in December to review the preliminary results. One of the main conclusions was: We have to continue doing this and expand the sample, and get more companies involved. Some of the companies have actually said they want to help us get more companies — their own customers — to be involved. And they’re going to go out and solicit them to do that. We’re growing the sample and we’re getting more and more companies to participate. We want to, by the end of this year, have a large enough sample — and this is not just China-specific, but this would be all regions of the world.
One of the hypotheses that people put forward is there is no overall global strategy anymore. It’s all very regional. What even a multinational does in China is going to be very different than what it does in North America or what it does in Europe. By asking these questions in different parts of the world, you’re going to get a very different perspective. So, we’ve expanded this to be more truly global in terms of where and what companies, and by increasing the sample, maintaining the basic analysis, the basic survey, which seems to be validated quite well and quite sound, but just to grow it.
And then, I guess long term, we’ll write it up, both at an academic level for publication and also at a level where we can communicate this to the business community and the political community, which we plan to do. But I think this could be an ongoing research project, could keep us busy for years.
Republished with permission from Knowledge@Wharton, the online research and business analysis journal of the Wharton School of the University of Pennsylvania.” Publication does not imply endorsement of views by the World Economic Forum.
To keep up with the Agenda subscribe to our weekly newsletter.
Author: Morris Cohen is a Wharton professor of operations and information management. Hau L. Lee is at Stanford.
Image: Workers on the assembly line replace the back covers of 32-inch television sets at Element Electronics in Winnsboro, South Carolina. REUTERS/Chris Keane
Don't miss any update on this topic
Create a free account and access your personalized content collection with our latest publications and analyses.
License and Republishing
World Economic Forum articles may be republished in accordance with the Creative Commons Attribution-NonCommercial-NoDerivatives 4.0 International Public License, and in accordance with our Terms of Use.
The views expressed in this article are those of the author alone and not the World Economic Forum.
Forum Stories newsletter
Bringing you weekly curated insights and analysis on the global issues that matter.
More on Economic GrowthSee all
Aengus Collins
May 14, 2025
Rya G. Kuewor
May 13, 2025
Tea Trumbic and Dhivya O’Connor
May 13, 2025
Navi Radjou
May 8, 2025
Dave Neiswander
April 28, 2025
Alem Tedeneke
April 25, 2025