Why the next big thing in 3D printing may be really tiny
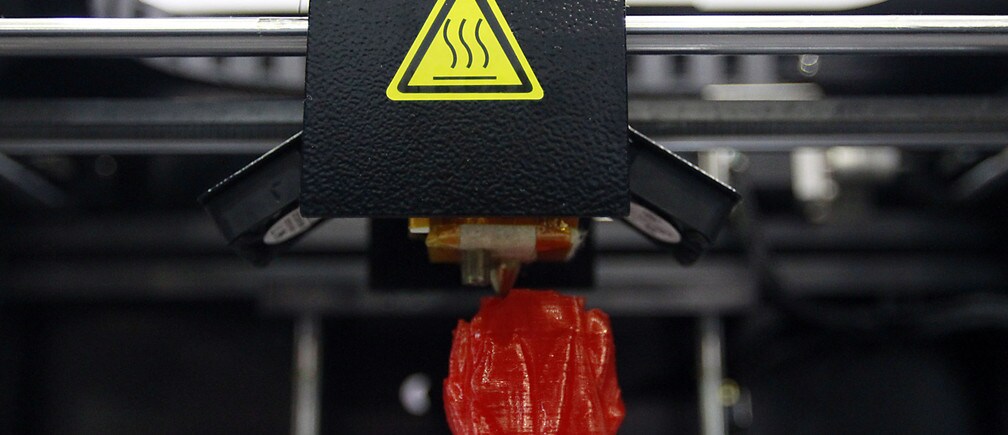
A wedding ring holding a piece of moon rock. Hydroponic garden structures tailored to any shape desired. Jet engine fuel nozzles. An Aston Martin template. These are but a few examples on the growing roster of 3D-printed structures that steadily made tech headlines over the past two years. With home 3D printers now selling for less than $500 and a market expected to reach US$16.2bn by 2018, 3D printing (3DP) is here to stay.
Although the idea of 3DP everything from guitars to cell phones to hip replacement parts is starting to enter the cultural zeitgeist, the technology’s capabilities have yet to reach their full potential. And, as demonstrated by researchers such as Jennifer Lewis of Harvard University, those abilities could one day stretch to scales both big (buildings, space) and small (at the nano and atomic levels).
Ms Lewis and her research group are focusing on creating, layer by layer, precise structures as small as one micrometre, developing the necessary chemistry, materials, software and machines to 3DP a range of objects on a level that most mortals would deem, quite simply, “really tiny”. In 2013, for example, her lab successfully employed silver nanoparticles to print microscopic electrodes for small lithium-ion batteries.
Some of the group’s most promising work involves 3DP biological cells; end products ultimately could be used in regenerative medicine. They’re not alone in pursuing this direction. A Princeton University lab has already printed a bionic ear that combines electronics with biological tissue, while a team at the University of Cambridge managed to print retinal cells. Similarly, outside the world of 3DP, researchers in Singapore and in Cambridge have coaxed stem cells into creating self-organized structures that could eventually become a section of liver or brain.
Ms Lewis’s lab, however, was the first to develop ways to 3DP complex, thick biological tissues networked with hollow tubes for blood vessels. Achieving such complex structures at the microscale requires overcoming hurdles, including the thermal or structural fragility of the materials involved as they undergo pressure inside the printing nozzle.
For products such as semiconductors, buttressing traditional materials with microscopic carbon fibres can provide a workaround. For fragile vascular cells, the lab develops inks that capitalise on the protective and viscoelastic properties of colloidal gels. Some of those inks contain a precise ratio of gelatin material and either mouse or human skin cells. When under pressure, the inks flow out of the nozzle continuously while retaining their shape, thus enabling the printing of tissue.
The layers destined to become hollowed-out tubes for vascular cells contain an ink that extrudes in a solid, gelatinous state at room temperature but liquifies when chilled. After printing complex tissue that includes layers of this ink, the researchers cool the tissue and vacuum out the liquified ink, which leaves the hollow tubes embedded in the structure. Those can then be filled with cells that normally constitute blood vessels.
The ability to create the complex and the tiny in this manner may be at the heart of the bio-printing medical 3DP market, which could reach $3-5bn in value in 10 years, according to market research firm IDTechEx.
But going big will be equally important to the long-term viability of 3DP. Key to scaling up will be the further development of lightweight, strong, flexible and dynamic materials. High-performance polymers are already in use for items such as 3D-printed jet engine parts. To get to the large scale, however, materials will also need to meet stringent thresholds, such as building-performance standards for live, dead, seismic and wind loads as well as for insulation and fire prevention. They will also have to withstand moisture, heat and other environmental elements that can expand, shrink and erode the construction.
With that in mind, the architects behind the 3D Print Canal House project in Amsterdam have been printing with bioplastics made of 80% vegetable oil that melts at 170 degrees Celsius. It’s not clear yet if such a plastic would be suitable for houses not meant as research projects. What will be also be necessary when printing houses and office buildings is the enabling of post-construction alterations to wiring or the correction of unforeseen problems in the structure. Conduits for electrical, plumbing and air-conditioning, for example, will need to be taken into account. So, too, will the opportunity for walls to be embedded with sensors. In the future, Internet-of-Things-ready 3DP construction could ultimately deliver interactive, circuit-embedded walls, temperature-adjusting radiant floors and optics-enhanced windows.
Another hurdle to overcome to enable viable, large-scale additive manufacturing is speed of production. Currently, up to four hours may be needed to print a single wedding ring in wax. Car manufacturers such as Ford Europe have also gone on record noting that the technology is still too slow and expensive to implement additive printing for high-volume mass production. (The industry does employ 3DP to make prototype parts, which can be printed in four days vs four months and for $3,000 vs $500,000, however.)
When it comes to building construction, achieving speed at scale might simply be a question of building enormous printers, following the example set by University of Southern California Professor Behrokh Khoshnevis. He has, over the past 10+ years, created a system to print 400-sq-ft structures and is developing huge 3D printers with the hopes of building a 2,500-sq-ft, multi-level home out of concrete in 24 hours. Already, Chinese company Win Sun claims to have used four printers measuring 150(l)x10(w)x6.6(h) metres each to print 10 200-sq-metre concrete houses.
The biggest prohibiting factor in going large may be cost, however, and recycling might play a role here. Using construction and material waste, the Win Sun project in China claims to have created a quick-drying concrete that enables it to 3DP a 650-sq-ft house for less than $5,000 – earlier this year, it showcased its first 3D printed 6-stories house in Suzhou Industrial Park. London-based Studio Swine is going even further, developing ways to recycle plastics floating in the ocean into 3DP materials. One man’s trash may soon become everyone’s treasure.
This article is published in collaboration with GE Look Ahead. Publication does not imply endorsement of views by the World Economic Forum.
To keep up with the Agenda subscribe to our weekly newsletter.
Author: Holly Hickman writes for GE Look Ahead.
Image: A figurine is printed by Aurora’s 3D printer F1 during the 2014 Computex exhibition at the TWTC Nangang exhibition hall in Taipei. REUTERS/Pichi Chuang
Don't miss any update on this topic
Create a free account and access your personalized content collection with our latest publications and analyses.
License and Republishing
World Economic Forum articles may be republished in accordance with the Creative Commons Attribution-NonCommercial-NoDerivatives 4.0 International Public License, and in accordance with our Terms of Use.
The views expressed in this article are those of the author alone and not the World Economic Forum.
Stay up to date:
Fourth Industrial Revolution
Related topics:
The Agenda Weekly
A weekly update of the most important issues driving the global agenda
You can unsubscribe at any time using the link in our emails. For more details, review our privacy policy.
More on Emerging TechnologiesSee all
Matt Price and Anna Schilling
November 20, 2024