How are aircraft manufacturers handling increased demand?
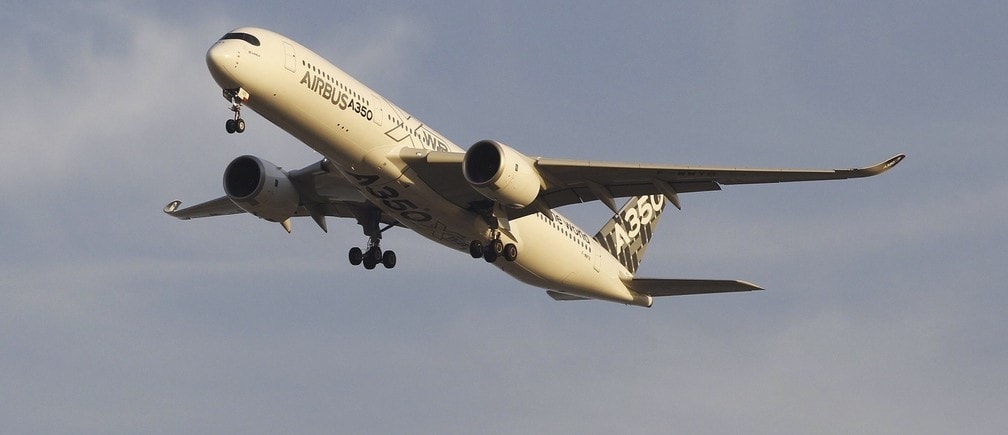
The two major commercial aircraft manufacturers, Airbus and Boeing, literally cannot build aircraft quickly enough: despite ramping up output by a combined 41% since 2010, the companies are still sitting on a nine-year backlog. They and their suppliers are thus racing to add production capacity across global, complex and highly regulated supply chains while current levels of demand remain strong.
The industry has not always handled such prosperity well. Nearly 20 years ago, Boeing attempted to double aircraft deliveries over an 18-month period and broke the production system. Factories building 737s and 747s stood idle in the fall of 1997 until the mess was sorted out, while an embarrassed Boeing reported a $2.6bn forward loss.
The goal, therefore, is to add capacity, but not too fast—and not too much. Notwithstanding an unprecedented string of rising aircraft deliveries, the aviation industry has historically operated in 10-year cycles, with 7-year, steady upswings followed by 3-year, crushing collapses. Aircraft factories are not unlike aircraft carriers in that sense: changes of pace or direction are possible, but they take some time.
Aircraft manufacturers must thus play a delicate game of meeting demand as aggressively as possible without risking over-exposure if the market suddenly turns. Not an easy task, but there are signs that the industry is finally learning how to cope with demand despite the complications of a widely distributed supply chain.
The latest version of the venerable 737, equipped with a pair of fuel-saving new engines, the CFM LEAP engine, offers a good example. Rather than create a satellite facility elsewhere to produce the wings, Boeing redesigned the existing jigs and tools of its factory in Renton, US, to handle the new production without disturbing the existing facility, which is currently running at full capacity. By preserving the factory’s existing footprint, Boeing avoids the risk of creating excess production capacity.
Advanced manufacturing techniques are also entering the industry. Last year, for example, GE invested $50m in its Auburn plant in Alabama to produce 3D-printed fuel nozzle discs for the LEAP engine. The goal is to produce 40,000 pieces a year by 2020—from just 1,000 today—according to the company. Boeing is also pushing robotic technology by automating riveting and bucking tasks on the 777X. Robots are not replacing workers, but they are minimising the number that must be hired to build aircraft at faster rates.
Finally, manufacturers are making smarter deals with their suppliers. Boeing, for example, is aggregating purchases of certain common parts and raw materials to obtain volume pricing, rather than have subtler suppliers fight one another for access to everyday items such as fasteners. GE Aviation, meanwhile, has formed eight joint ventures with suppliers in two years, locking up access to critical capacity and technology such as with Parker Aerospace for the fuel nozzles, Woodward for the fuel systems and Turbocoating for thermal barrier coatings on ceramic matrix composites.
An airliner, as the saying goes, is really about 1 million parts flying in close formation. That also describes the supply chain, and, so far, the parts are keeping up with the accelerating production rates.
This post first appeared on GE LookAhead. Publication does not imply endorsement of views by the World Economic Forum.
To keep up with the Agenda subscribe to our weekly newsletter.
Author: Stephen Trimble is an author and journalist on aviation issues.
Image: An Airbus A350 XWB aircraft flies over Ataturk International Airport during the Istanbul Airshow in Istanbul September 25, 2014. REUTERS/Osman Orsal.
Don't miss any update on this topic
Create a free account and access your personalized content collection with our latest publications and analyses.
License and Republishing
World Economic Forum articles may be republished in accordance with the Creative Commons Attribution-NonCommercial-NoDerivatives 4.0 International Public License, and in accordance with our Terms of Use.
The views expressed in this article are those of the author alone and not the World Economic Forum.
Stay up to date:
Supply Chain and Transport
Forum Stories newsletter
Bringing you weekly curated insights and analysis on the global issues that matter.
More on Supply Chains and TransportationSee all
Michael Fröbel and Prince Arora
December 17, 2024