Could 3D printing be the future of architecture?
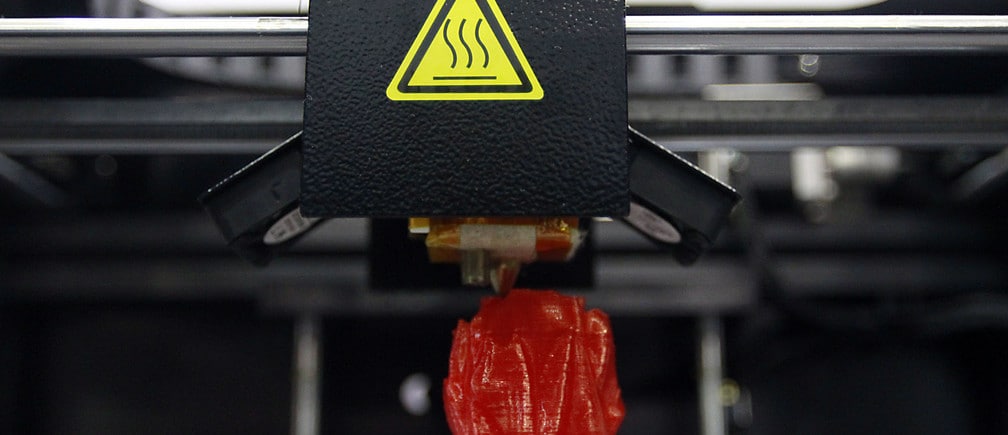
Stay up to date:
Media, Entertainment and Sport
Standing over 13 feet (4 metres) high in the Chicago Cultural Center, the monolithic Rock Print installation with its rough, yet elegant contours confirms that collaboration inspires “State of the Art Architecture” – the theme of the inaugural Chicago Architecture Biennial. Born out of a 2012 University of Chicago conference that brought architects, engineers, material scientists, and physicists together, Rock Print demonstrates a principle called, “jamming.” Jamming refers to aggregate granular materials, like gravel that are quite literally crammed together in such a way that they hold their form and shape like a solid even though their molecular properties are closer, in terms of behaviour, to a liquid substance. “Jamming” together, researchers from Gramazio Kohler Research, ETH Zurich and Skylar Tibbits’ Self-Assembly Lab at the Massachusetts Institute of Technology (MIT) produced, Rock Print – a zero waste and fully reversible architectural installation for the inauguration of the Chicago Architecture Biennial that opened on 3 October 2015.
Inspired by 3D print technology
“Rock Print is a proof of concept that takes current robotic fabrication technology and applies it to a full-scale architectural project,” said Andreas Thoma, ETH Zurich. Petrus Aejmelaeus-Lindstroem, lead researcher for the project at ETH Zurich added, “The project shows the capacity of a 3D printing process to create a geometrically-complex construction using two simple components found in everyday life – string and rocks.” The environmentally conscious ETH and MIT installation team used a custom robotic fabrication setup to lay down nearly 5 miles (9.1 km) of a recycled textile string in a complex pattern guided by a specifically designed algorithm. Like making lasagne, the string is alternated with layers of a loose standard concrete aggregate (rocks) from the Swiss company, Misapor. The company makes self-insulating concrete using crushed glass, additives, and a heating process that expands the glass into a foam-like aggregate of mostly air. While the foam glass is a fraction of the weight of conventional gravel aggregate, Rock Print weighs in at slightly less than one tonne (970 kg to be exact). The weight is a delicate balance – a lighter weight material is necessary for an indoor installation, but the structure of the installation depends on weight to provide strength to the compressional forces that maintain its shape and to compensate for the relatively weak tensional forces.
New possibilities for the future of architecture
Matthias Kohler, who also serves as the Director of the National Competence Centre in Research (NCCR) Digital Fabrication, commented on how 3D printing technology may influence architecture in the future stating, “3D printing technology is an inspiration for the future of architecture as it brings together resource efficient additive building principles with new possibilities for design. Such technology enables production of complex forms and intricate details of building elements at a minimal cost. Today’s commercially available 3D printing technologies are not yet suitable for the scale needed for architecture or its economic and structural demands.”
The Rock Print installation challenges and expands the scope of 3D printing to an architectural scale by introducing robotic fabrication and the use of inexpensive, reconfigurable bulk construction materials. This radical approach attempts to open new possibilities for future architecture – using advanced digital fabrication technology to build with sustainable and locally available materials. Kohler says, “There is still a lot of interdisciplinary research needed to fully understand and leverage future digital fabrication principles at a full building scale, but after ten intensive years of research in the field, I am positive that such new principles will not only lead to exciting architecture projects, but also to a new digital building culture – possibly to a socially relevant transformation of our built environment.”
This article is published in collaboration with ETH Zurich. Publication does not imply endorsement of views by the World Economic Forum.
To keep up with the Agenda subscribe to our weekly newsletter.
Author: Marianne Lucien is the International Communications Officer at ETH Zürich News.
Image: A figurine is printed by Aurora’s 3D printer F1 during the 2014 Computex exhibition. REUTERS/Pichi Chuang.
Don't miss any update on this topic
Create a free account and access your personalized content collection with our latest publications and analyses.
License and Republishing
World Economic Forum articles may be republished in accordance with the Creative Commons Attribution-NonCommercial-NoDerivatives 4.0 International Public License, and in accordance with our Terms of Use.
The views expressed in this article are those of the author alone and not the World Economic Forum.
Forum Stories newsletter
Bringing you weekly curated insights and analysis on the global issues that matter.
More on Emerging TechnologiesSee all
Michelle You
April 10, 2025
Ellen de Ruiter
April 10, 2025
Nii Simmonds and Obinna Isiadinso
April 9, 2025
Katia Moskvitch
April 9, 2025
Marc Alexander Penzel
April 9, 2025