What are the challenges of managing a supply chain?
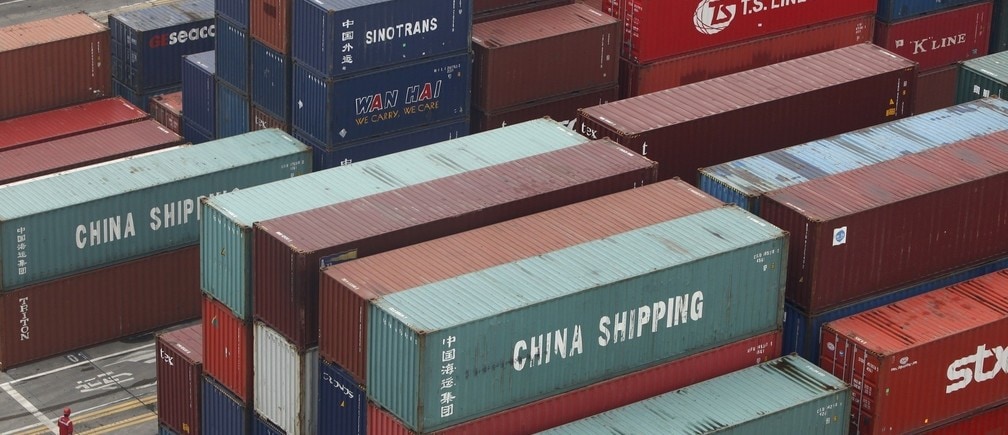
This article is published in collaboration with the Bill and Melinda Gates Foundation.
Managing a supply chain is easy, right? After all it simply requires perfectly matching supply and demand, then getting the product in the hands of the customer. Why then is it so hard to achieve such a simple concept?
The power of real time data
Matching supply and demand requires knowing the levels of supply and demand in real time. It’s simple to understand, but a lot more complicated to achieve. The solution though can be easily stated: data visibility. If people managing the supply chain know what demand is and what their supplies are, at any moment, at each level in the system, they can begin to effectively match supply and demand. However, achieving data visibility remains a major challenge.
In Ethiopia, the Pharmaceuticals Fund and Supply Agency (PFSA) maintains the vaccine supply chain and is taking significant steps to ensure real time data and information on supply and demand can be available at any time. Working with the USAID | DELIVER PROJECT and the Bill & Melinda Gates Foundation-funded Vaccine Supply Chain Transition project implemented by John Snow Inc. (JSI), PFSA now has visibility for vaccine supply data at central and regional hub levels and can use this information to deliver vaccines to district level.
The Health Commodity Management Information System (HCMIS), currently manages the supply chain for essential medicines across the country, and a new module within the system is being used to provide ready data on the vaccine stock on hand, expiration dates, and other key metrics. The HCMIS Vaccine Management platform, which is being rolled out across the country, has a customizable dashboard that puts real time supply chain data in the hands of decision makers who need it most.
Currently, the vaccine management features of the HCMIS have been introduced at the central level and at three of the PFSA Hubs in Bahir Dar, Mekelle, and Jimma. And deployment is currently in progress to the more than 61 woredas (districts) in the Tigray and Afar regions served by Mekelle Hub. Based on the results there, the transition team will determine if and how to roll out the system to other woredas around the country.
Where the system is already in place, EPI officers and other staff are already seeing an impact on how they do their work. Where before they used paper records and manual counts for vaccine stock management, now they can view stock levels within the HCMIS and use the system to issue vaccines to their health facilities. As one user in Tigray Region said, “You just have to click and you know the stock status.”
Optimizing vaccine delivery
The PFSA management of vaccine supply chain is also creating new opportunities to improve how vaccines are distributed throughout the country. Now that it’s easier to measure stock availability and project needs, the PFSA is focused on improving the delivery of vaccines.
In the past, regional, zonal, woreda, and health facility staff collected vaccine supplies from the level above. Now, PFSA is delivering vaccines from the central cold room to their regional hubs, and then to the zones and/or woreda (district) level using refrigerated trucks. Distributing vaccines to numerous sites presents a logistical challenge. By using state of the art supply chain analysis and design, and techniques from the commercial sector, we’re able to meet the challenge.
Alongside JSI, the PFSA has conducted a distribution analyses to determine the most efficient direct distribution and transportation network for each PFSA hub. The results of the analysis were immediately put to use in a number of PFSA hubs and the information has increased efficiency in the system and improved the ease and speed of moving vaccines between levels. Additional money that would have been spent traveling to pick up the vaccine from the regional cold room each month can now be allocated to other important activities.
Given these successes, PFSA is looking to extend their work in the coming year to determine what resources would be needed for direct delivery to health facilities–the ultimate goal of the vaccine supply chain transition.
Publication does not imply endorsement of views by the World Economic Forum.
To keep up with the Agenda subscribe to our weekly newsletter.
Authors: Paul Dowling is Country Director for John Snow Inc.’s Vaccine Supply Chain Transition Project in Ethiopia. Al Shiferaw is MIS Director for John Snow Inc.’s Vaccine Supply Chain Transition Project in Ethiopia.
Image: A worker walks in a shipping container area at the Port of Shanghai. REUTERS/Aly Song.
Don't miss any update on this topic
Create a free account and access your personalized content collection with our latest publications and analyses.
License and Republishing
World Economic Forum articles may be republished in accordance with the Creative Commons Attribution-NonCommercial-NoDerivatives 4.0 International Public License, and in accordance with our Terms of Use.
The views expressed in this article are those of the author alone and not the World Economic Forum.
Stay up to date:
Trade and Investment
Related topics:
Forum Stories newsletter
Bringing you weekly curated insights and analysis on the global issues that matter.
More on Financial and Monetary SystemsSee all
Rishi Kapoor
December 20, 2024