The internet of things will disrupt manufacturing for ever, but are you ready?
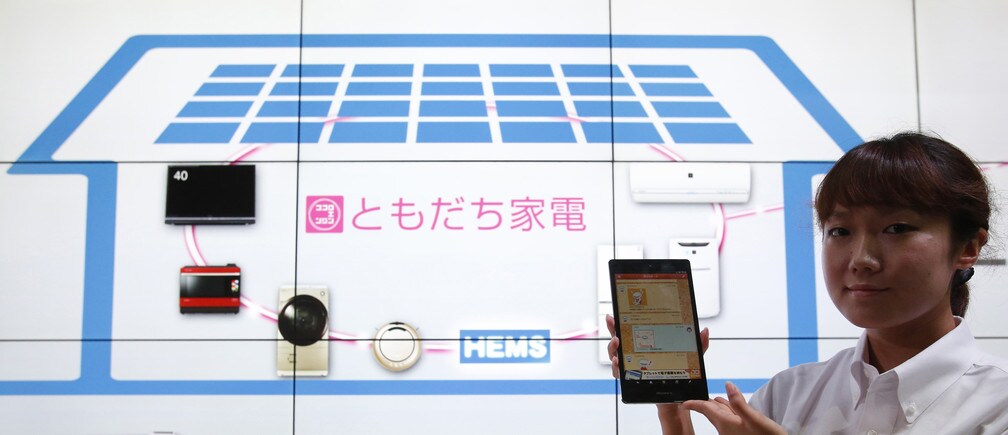
Smart technology is increasingly used to control household appliances
Image: REUTERS/Yuya Shino
Stay up to date:
Advanced Manufacturing
Digitization is a major driving force of our time, turning our world inside out. Smart and connected systems are increasingly pervading all types of applications. The internet of things (IoT) is already starting to affect environments of all kinds – homes, cities, travel, logistics, retail and medicine, to name just a few – and it will not stop at our factory gates, either.
According to a recent estimation by McKinsey, the potential economic impact of IoT applications in 2025 is between US$ 3.9 and $11.1 trillion, of which $1.2 to $3.7 trillion is allotted to IoT applications within the factory environment. Also known as smart manufacturing, or Industrie 4.0 in Germany, these are fully networked manufacturing ecosystems driven by the IoT.
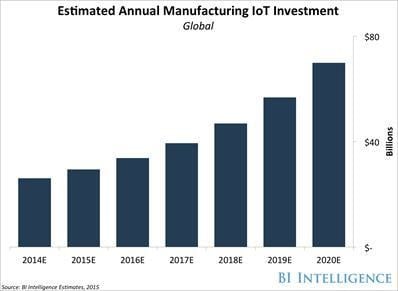
In a future where all “factory objects” will be integrated into networks, traditional control hierarchy will be replaced by a decentralized self-organization of products, field devices and machines. Production processes have to become so flexible that even the smallest lot size can be produced cost-effectively and just in time to the customer’s individual demands. Customers are driving this development too, as they can design and order products at the click of a mouse. They can also expect their products to be delivered within a few days – or even hours – and don’t want to wait weeks for goods to travel from far regions of the world where labour costs are lower.
Despite this huge potential, the introduction of IoT technologies in the rather traditional domain of manufacturing will not happen abruptly: investment cycles are long, and robustness of processes and technologies outweigh the striving for innovation. Too many questions have to be answered first.
As IoT technologies penetrate ever more deeply into our factories, down to the smallest piece of equipment, technology providers and factory planners must find solutions to four main problems:
- How to assure the interoperability of systems
- How to guarantee real-time control and predictability, when thousands of devices communicate at the same time
- How to prevent disruptors, or competitors, taking control of highly networked production systems
- How to determine the benefit or return on investment in IoT technologies.
To compensate for technological uncertainty and financial risks, adequate pilot environments are needed. Here, smart manufacturing technologies and strategies can be implemented, evaluated and showcased for the first time. This is why almost every big IT or automation technology provider has built its own smart manufacturing lab, where it can test and demonstrate proprietary solutions. But they are missing one important point: smart manufacturing is a network paradigm affecting wide-ranging areas from automation to IT, from digital planning of a product to its recycling, and from smart sensors to business applications.
There is no single-solution provider that can cover all of these aspects at once. So, for holistic solutions to emerge, there has to be a network of technology providers joining forces and competences to develop compatible solution blocks that fit the future requirements of technology users.
One possible set-up for such centres, where holistic smart manufacturing solutions are developed, is an association in which partners from industry and research work together. Such a network can include large multinational enterprises, small and medium-sized companies, as well as highly experienced research centres. An important goal of such a collaboration model is to test innovative factory technology under realistic conditions and to move it as quickly as possible from the laboratory to the marketplace.
The strength of such an association lies in its set-up as a “neutral” platform: it connects technology providers and users, regardless of their competitive situation in the business world. This means that companies with overlapping business and competence areas work together, regardless of their size, history and economic situation. Here, they can develop general standards that are independent and thus not tied to a specific company or brand, and they can offer proprietary technologies and business models for use in open ecosystems.
Technology providers with complementary business or competence areas can also benefit from the networking opportunities that arise when different domains are connected, for example, at the interface between classic automation technology and IT systems, such as big data applications or digitization of maintenance processes. The network is complemented by research partners. Their role is to work on the necessary research projects and push the results into applications. Furthermore, they coordinate the collaboration of all partners.
One such collaboration model has been realized by SmartFactoryKL in Kaiserslautern, Germany, since 2005. Their implementation of a highly modular production line based on Industrie 4.0 standards can be considered the first best practice example for multi-vendor collaboration. The paradigm of smart manufacturing has awakened the vision of highly efficient, customer-driven factories that seamlessly connect to smart ecosystems. But, until then, we still face numerous challenges. Proving that smart manufacturing solutions are feasible from a technical perspective is only half the job.
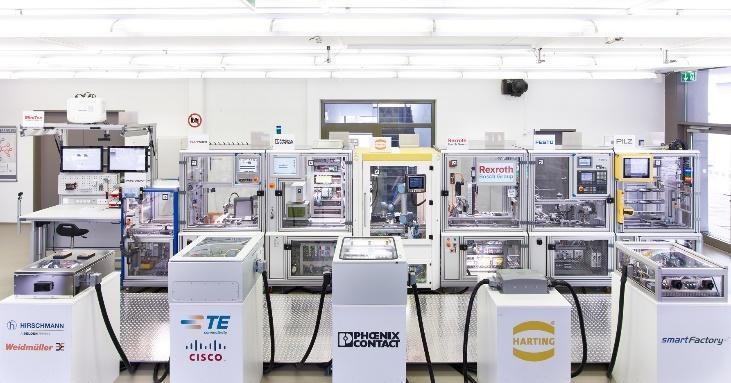
One of the biggest problems today is the lack of technology acceptance and system interoperability. Widely accepted standards are a crucial requirement for the next industrial era, but they are far from easy to achieve. First, it requires a significant market demand driven by customers' needs – this is the market pull. Secondly, it needs a critical mass of companies, which collaborate and agree on common and marketable solutions – this is the technology push.
Of course, no industrial revolution has ever taken place in haste. Instead, the changes developed over a period of several decades in an evolutionary transition driven by technological advances and market demands. It is highly likely that the current movement towards smart manufacturing will end up being an evolution which lasts decades. If we want to speed up these developments, we need to establish more inter-organizational networks and test environments as catalysts.
Don't miss any update on this topic
Create a free account and access your personalized content collection with our latest publications and analyses.
License and Republishing
World Economic Forum articles may be republished in accordance with the Creative Commons Attribution-NonCommercial-NoDerivatives 4.0 International Public License, and in accordance with our Terms of Use.
The views expressed in this article are those of the author alone and not the World Economic Forum.
Forum Stories newsletter
Bringing you weekly curated insights and analysis on the global issues that matter.
More on Manufacturing and Value ChainsSee all
Benedikt Gieger and Alfredo Ramos Plasencia
July 7, 2025
Aarushi Singhania and Kiva Allgood
July 4, 2025
Michael Donatti and Laura Fisher
July 3, 2025
Kaiser Kuo
June 26, 2025