Creating a better future for garment manufacturing in Bangladesh
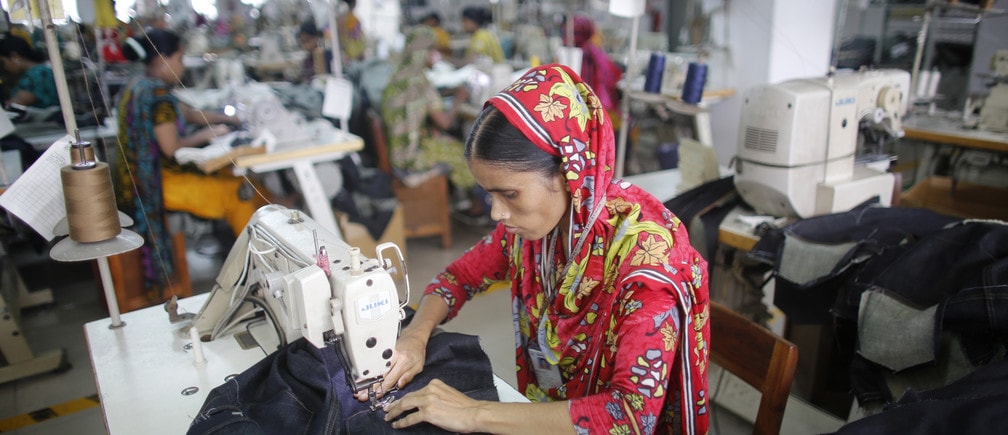
How automation can deliver value for customers and ensure no garment worker is left behind.
Image: REUTERS/Andrew Biraj
Stay up to date:
Future of Consumption
- Globalization, rising wages and customer demand have all played a role in the dramatic transformation of the garment manufacturing sector.
- Garment workers are being displaced by automation, especially in Bangladesh.
- By focusing on shared value, government and industry can ensure no one, particularly women in the garment supply chain, gets left behind.
What images come to mind when you hear the words “automated manufacturing”? Probably big industrial robots welding parts or slack-lined gantries zooming materials overhead. Chances are, these images were from automotive or electronics factories. But this is not the kind of automation you’ll see in a garment factory.
In the apparel sector, automation is still predominantly task-based, and it’s just starting to change the production process and the people who support it.
This stage of automation adoption maturity is the perfect place for innovative strategies to truly achieve shared value for workers.
The garment manufacturing industry began as a local business – and this worked well, with local consumer demand, a local labour force and local raw materials.
Industrialization brought the shift from hand-sewn clothing to a production model in which clothing was made in factories with help from machines. Even with sewing and cutting equipment doing more of the work, however, the dexterity required to handle the fabrics – for example, to fold seams and guide them under a mechanized needle for sewing, or to smooth a wrinkle in fabric before a piece was cut incorrectly – continued to be an important factor in the success of the human workforce.
As globalization gained traction and international trade agreements opened new possibilities for global value chains, brands searched for new locations where people with nimble, dexterous hands could be taught to make clothes for a fraction of the cost of a Western worker. Infrastructure including ports, roads, technical colleges and unions grew, and soon, a crop of Asian countries became home to the leading seamstresses to the world.
As wages are rising in these countries, supply chain executives now seek other regions of the world, such as East Africa, to develop a workforce at a lower wage rate and achieve the margins they desire.
The World Economic Forum, in collaboration with the United Nations Development Programme (UNDP) and A.T. Kearney, found the current garment manufacturing model faces a “perfect storm” of economic, social and environmental dynamics. It’s reshaping production and global value distribution, creating new opportunities – but also creating risks, especially for countries like Bangladesh.
On one hand, new global pacesetters of value chain design – companies such as Inditex and Alibaba – are leveraging emerging technologies to recalibrate consumer expectations towards wider choice, higher speed and superior service. Most consumers have moved away from seasonal shopping a few times per year in favor of purchasing clothes intermittently, based on trends. This change in consumer preference has big repercussions for apparel brands and manufacturers because the pressure to design, market and deliver something while a trend is still relevant shrinks the product development cycle from six months to six weeks.
On the other hand, the need to address the underlying drivers of environmental degradation is increasingly recognized by stakeholders in government, civil society and business. Gen Z shoppers are gravitating towards brands with strong sustainability programs and storytelling. Large multinational brands are factoring climate change or water shortages into risk models. And circularity is forcing greater strategy considerations into design for material reclamation at end-of-life as well as the growing resale market for clothes.
As more and more businesses turn to fast fashion, lead time dominates the discourse around sourcing. The other narrative? Sustainability, and in particular, discouraging excess consumption and promoting circularity and ethical choices by consumers.
Manufacturers must operate in the middle of this dichotomy. They have no choice but to innovate and continue optimising production capacity to create more value, add technology to improve efficiency and promote new sustainability strategies that include social impact.
In this context, automation is a key enabler of success. It’s set to take over much of the manual work involved in making clothes. Due to the nuanced dexterity required in material handling, limited investment in commercializing new equipment and lagging adoption of many forms of technology, however, the sector has been slow to fully automate production. But this is changing.
As automation gains momentum in apparel manufacturing, how can we ensure workers are not left behind?
What is the World Economic Forum doing about the Fourth Industrial Revolution?
A key capability increasingly recognized by managers is automation technologies to support human and machine collaboration. It’s no surprise garment manufacturers pinpoint digital literacies as critical skills for the future of work.
Digital literacies in apparel manufacturing should center around digital models: reading, changing, evaluating, troubleshooting and, at the top skill tier, creating. Now, 3D digital models (CAD) are necessary building blocks for producing a larger number of styles and sizes, and to support the ever-shrinking manufacturing timeline in the era of trend-focused shopping. Digital models are also necessary to bring sustainable apparel design to scale.
Currently, most workers in CAD departments in Bangladesh are male. They went to technical colleges or were promoted to digital jobs internally. Women are typically concentrated in the lower tiers of the supply chain, primarily clothing construction, and not likely to receive technical training. As a result, women are being left behind. But because they comprise 60.8% of the apparel supply chain, the industry must take care to ensure access to training.
The 3D.RC, a coalition of stakeholders including Target, VF Corporation and Under Armour, are developing standards for 3D skills. They’ve identified knowledge of clothing construction as a fundamental baseline skill for success in 3D. This means the slope to upskill the workers most in danger of being left behind might not be as steep as expected, since line workers understand clothing construction.
According to MIT’s Erik Brynjolffson, countries dependent on the garment sector will need to “leapfrog” traditional methods for reskilling workers in order to transition workers in time.
Bangladesh signaled they want to reskill at least 1-2 million workers – and they want to try innovative approaches to get there. The country is experimenting with new human computer interaction methods for training workers, like gamified training in digital modeling. With support from the C&A Foundation and Microsoft, Shimmy Technologies will scale the technology via factory training programs.
Accept our marketing cookies to access this content.
These cookies are currently disabled in your browser.
The path forward
In December 2019, Bangladeshi policy, government and business leaders came together to recognize the need for coordinated effort to seek innovative solutions from unconventional partners.
"Nearly 30% of the workers have been displaced from the sweater sub-sector of the readymade garment sector because of automation. We should impart skills training to them so that they can make themselves competent for advanced jobs," said Bangladesh Garment Manufacturers and Exporters Association vice-president Faisal Samad.
While innovative upskilling concepts are promising, they’re a drop in the bucket of what’s needed to upskill this population in time. Brands, manufacturers, agencies and technology providers must collaborate on education, skills development and R&D, and work to ensure local reskilling hubs progress at a speed that provides these workers a just transition.
It’s not too late to discover a model for shared value in this sector, but we must intervene now. If we do, the apparel sector might just be the industry that gets reskilling right.
Don't miss any update on this topic
Create a free account and access your personalized content collection with our latest publications and analyses.
License and Republishing
World Economic Forum articles may be republished in accordance with the Creative Commons Attribution-NonCommercial-NoDerivatives 4.0 International Public License, and in accordance with our Terms of Use.
The views expressed in this article are those of the author alone and not the World Economic Forum.
Forum Stories newsletter
Bringing you weekly curated insights and analysis on the global issues that matter.
More on Forum InstitutionalSee all
Victoria Masterson, Stephen Hall and Madeleine North
March 25, 2025
Lorez Qehaja
March 19, 2025
Madeleine North
January 28, 2025