Factory workers face a major COVID-19 risk. Here’s how AI can help keep them safe
Monitoring social distancing and the use of protective gear can help shield workers from coronavirus.
Image: REUTERS/Anushree Fadnavis
Stay up to date:
Emerging Technologies
- When India emerged from COVID-19 lockdown in May, keeping factory workers safe from infection became an urgent priority.
- Artificial intelligence solutions such as big data analysis can help businesses monitor social distancing and the use of protective gear, and facilitate contact tracing in the event of a worker testing positive.
- Smart technologies could allow factories, offices, shops and airports to re-open safely.
When India emerged from COVID-19 lockdown around the end of May, my company’s artificial intelligence branch received urgent calls from business leaders all over the country and beyond. They needed fast, reliable and affordable solutions to protect their workers’ health and prevent coronavirus from spreading in their factories. My group, Bharat Light & Power (BLP Group), specializes in renewable energy but also owns an artificial intelligence platform, BLP Industry.AI, that develops smart technologies such as big data analytics and machine learning. Now businesses wanted to know how they could tap the power of these technologies to re-open their factories safely.
Among the businesses contacting us was one of the largest fast-moving consumer goods (FMCG) companies in the world. Providing a secure manufacturing environment, and giving employees the confidence to return to work, was going to be crucial for the supply of ordinary products used daily by millions, such as soaps, toothpaste, detergents or cereals. Since the risk of infection was particularly high in crowded indoor spaces, manufacturers also had a public health duty to prevent factory outbreaks that could spread to the rest of society. Few of them had ever faced such a complex challenge before, one with deep implications for pandemic control but also human resource management, productivity, and global supply chains.
As we worked with our partners to quickly develop the solutions they needed, we learned lessons that could serve businesses everywhere, and make the world’s factories safer and more resistant to current and future shocks.
AI for early warning
I originally set up Industry.AI after one of our windmills burned down, creating significant losses. The idea was to use big data analytics and machine learning tools to predict failures in wind turbines before any major damage was caused. From there, Industry.AI grew to provide similar predictive technologies and other artificial intelligence (AI) algorithms to corporations around the globe. These highly sophisticated early-warning systems served us well when it came to fighting COVID-19.
Floor managers and supervisors typically face a number of problems as they try to stop the spread of the virus. Firstly, it is impossible to constantly monitor in person that workers are wearing the required protective gear, such as masks and visors, and that they and external visitors are observing social distancing rules. Some companies require employees to report daily whether they are unwell, or have visited a containment zone, but monitoring these self-declarations is cumbersome. Supervisors are also supposed to monitor the temperature of every employee, quickly isolate those with a high fever, and implement full contact tracing for anyone testing positive for COVID-19. But aside from the practical difficulties, the sheer cost of these measures would crush any small and medium-scale company.
We have developed three broad solutions to help these businesses. They provide immediate protection during the coronavirus crisis, all the way from early detection to containment measures, but can also be applied in other common safety scenarios, such as detecting fires.
Camera feeds and cloud technology for monitoring
The first solution centres on a cloud-based system that deploys a combination of visual analytics models, mathematical models, and neural network models to analyze existing video feeds from cameras from the factory floor, offices, malls or airports.
Some of these feeds are ordinary videos of employees at work, which are uploaded to the cloud. Algorithms analyze the images in real time, and issue an alert to the safety officer in charge if a worker does not wear appropriate safety gear, or breaks social distancing guidelines. Another option is to install thermal cameras. Thermal imaging feeds display body temperatures in different colours, with orange and red indicating higher-than-average temperatures. Algorithms can analyze these thermal images and trigger an alert when a person is potentially running fever.
The algorithms also analyze the data for trends and patterns that help managers form a broader view of the situation on the factory floor, and detect and fix any systemic security gaps or unsafe processes.
What is the World Economic Forum doing to help the manufacturing industry rebound from COVID-19?
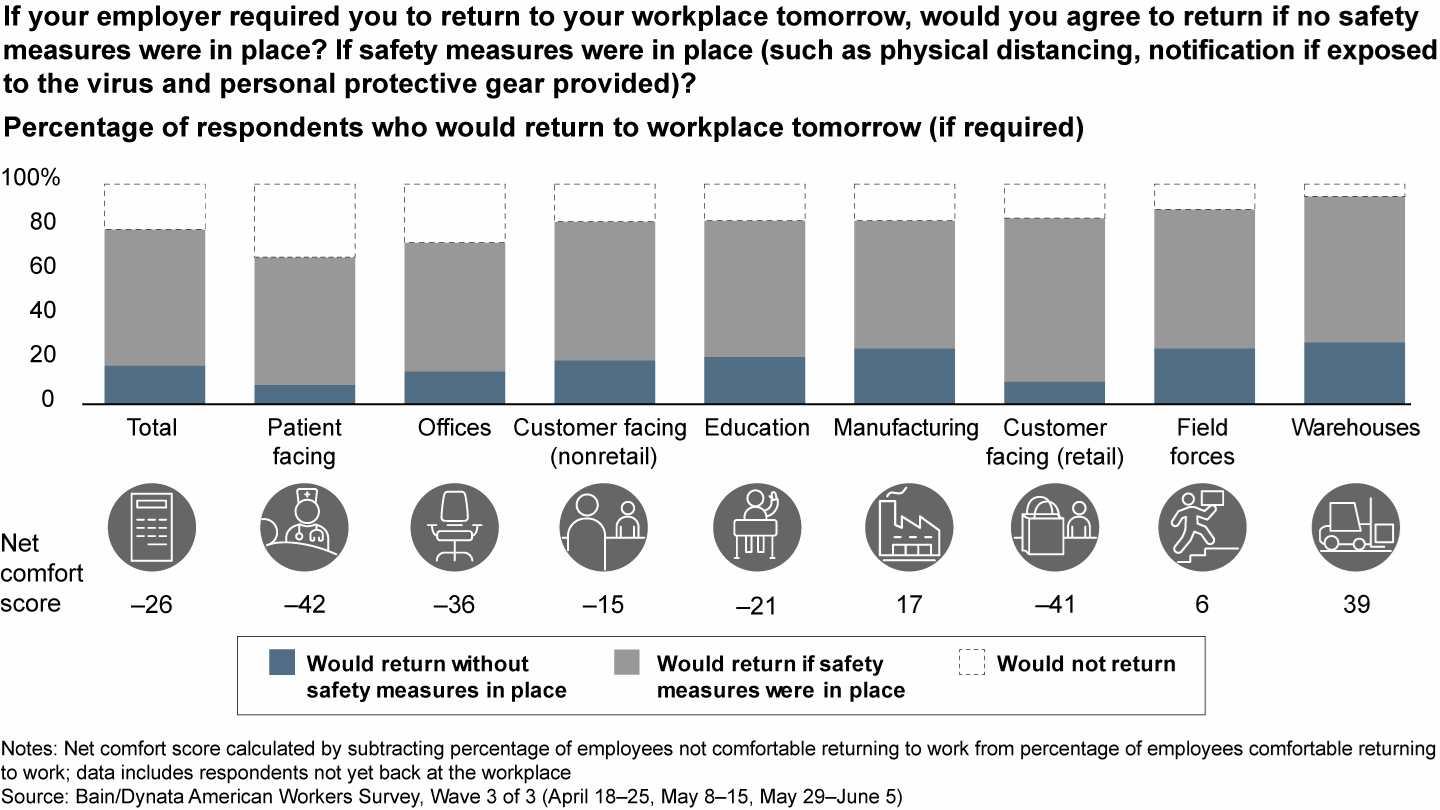
Mobile phone technology for safety
Our second solution is based on mobile phone technology that enables phones to communicate with each other. This system provides real-time alerts when social distancing rules are breached, and tracks employees’ temperatures every few hours to detect potential fevers. The same technology facilitates fast contact tracing if anyone tests positive, by listing all those who have been in close proximity to the infected person, as long as they all carry mobile phones.
Such contact tracing in workplaces can support government efforts to protect the public. For example, India’s government has rolled out a mobile contact tracing and self-assessment application called Aarogya Setu, which was downloaded 100 million times in the first 40 days. Other governments around the world have launched similar tools, but their uptake varies considerably between countries. This makes it all the more important for private enterprises to conduct contact tracing in their own workforce in order to ensure factories don’t have to shut down due to coronavirus, which would result in lost production.
Wearable devices
The third solution is based on wearable devices such as wristbands or smart ID cards. These objects vibrate whenever a worker breaches social distancing rules, and also transmit the relevant data to the cloud if permitted and required by the organization for analytics. The technology is normally used to locate workers, machines and materials on the factory floor, and ensure an optimal workflow for maximum productivity. In the current crisis, it has been adapted to fulfil a vital public health function.
The vibrating wristband provides a clear signal to the worker, who may not have been aware of stepping too close. It also informs the safety officer in charge and can help them identify the root cause of recurring patterns and problems. For example, space constraints or the factory’s layout may encourage workers to come too close to each other during specific parts of the manufacturing process. Universities and schools are exploring using these technologies, taking into account strict privacy norms.
Together, these technologies cover the chain of potential coronavirus transmission in the workplace, all the way from prevention to contact tracing in the case of an outbreak. However, they also come with challenges of their own. Some, such as technological challenges, can be solved in the development process. Others, such as privacy, need to be addressed at the development stage as well as during the implementation of these technologies, in order to make people feel comfortable using them.
Using data responsibly
Any technology that continuously monitors people, their behaviour and their health raises obvious concerns around privacy and the use of sensitive personal data. Through our dialogue with our partner companies, we came up with several ways of reducing those concerns.
First of all, the technologies are only being applied within the confines of a factory or a particular office. They are not used for any purpose other than monitoring safety adherence and early COVID-related symptoms, and are not shared with anyone else. All data is anonymous, and only the safety or health officer or appointed administrators of that company have access to it. The camera feed is not stored on any server. Any alerts are deleted within a certain period of time as per the companies’ privacy policy.
Safeguarding workers’ privacy is not just a moral obligation. It also has practical consequences when it comes to implementation and compliance. Workers will only embrace these technologies if they feel that the sole goal is to protect their health and that of wider society, not to coerce or control them. Successful human resource management and a positive company culture built on trust play a critical role in helping workers understand the scope and benefits of these smart tools. In an environment of trust and cooperation, employees will be more ready to accept that it is in everyone’s best interest to adopt them.
Beyond COVID
It is heartening to see corporations develop partnerships and come together in a time of crisis. In this case, the partnership between a few large corporations, with an agile technology company, and subsequent pilot programs with other industries, resulted in scalable and frugal solutions to be tested and rolled out in a short period of time.
These tools have been implemented in our clients’ factories all over India and beyond, but could also be adapted to offices, shops and airports, monitoring customers and travellers as well as the people working in those spaces. Companies are already evaluating how they could be used to boost worker safety in other scenarios beyond the coronavirus pandemic.
There are fears that the pandemic may return in waves, and the vaccines may not be ready for all virus mutations. In this situation, industries will have to support each other, and help governments accelerate the adoption of next-generation technology in many areas of life. The disruption of supply chains has forced companies to speed up their digital transformation plans to improve not just workers’ safety, but also organizational productivity and decision-making. AI can help with these processes, too, transforming modern manufacturing and creating the secure, resilient and productive workplaces of tomorrow.
Accept our marketing cookies to access this content.
These cookies are currently disabled in your browser.
Don't miss any update on this topic
Create a free account and access your personalized content collection with our latest publications and analyses.
License and Republishing
World Economic Forum articles may be republished in accordance with the Creative Commons Attribution-NonCommercial-NoDerivatives 4.0 International Public License, and in accordance with our Terms of Use.
The views expressed in this article are those of the author alone and not the World Economic Forum.
Related topics:
Forum Stories newsletter
Bringing you weekly curated insights and analysis on the global issues that matter.
More on Manufacturing and Value ChainsSee all
Benedikt Gieger and Alfredo Ramos Plasencia
July 7, 2025
Aarushi Singhania and Kiva Allgood
July 4, 2025
Michael Donatti and Laura Fisher
July 3, 2025
Kaiser Kuo
June 26, 2025