Here’s why human-robot collaboration is the future of manufacturing
Manufacturing is faster, cheaper and safer when humans and robots work together.
Image: REUTERS/Stringer
Stay up to date:
Future of Work
- COVID-19 has highlighted the need to create more resilient supply chains and the importance of human workers.
- Automation alone can be expensive and inflexible, because robots are typically designed to carry out just one precise task.
- The best choice is to pair robots with human workers, combining the strength and speed of industrial robots with the creativity and ingenuity of humans.
The COVID-19 pandemic has dealt a heavy blow to manufacturers around the world. Lockdowns and travel bans have disrupted production as well as supply chains. New outbreaks in factories and other workspaces have highlighted the need to better protect workers’ health and safety. In a March 2020 survey by the National Association of Manufacturers (NAM), 53% of manufacturers anticipated a change in operations due to COVID-19.
This need for transformation goes beyond the immediate coronavirus crisis. The manufacturing industry is under pressure to respond to ever-changing market needs. Modern demands of mass customization, higher product variability and quality expectations, and faster product cycles are creating complex challenges for manufacturers, whose economics are best suited to much longer product cycles and limited variability.
If manufacturers want to compete in a fast-evolving global market, they will need to fundamentally transform the way they produce goods. Now is the time to tackle these long-standing challenges by pairing human skill and creativity with the strength and speed of robots.
What is the World Economic Forum doing to help the manufacturing industry rebound from COVID-19?
The challenges of automation
Today’s industrial robots maneuver heavy and dangerous workpieces at high speeds, and cannot safely operate near humans. That’s why most manufacturing process steps are either fully automated or fully manual. However, this black-or-white approach to automation introduces new problems.
One is that automation is expensive and time-consuming to design. The precision robots enable is a double-edged sword—each process step requires specific coding and relies on uniform and predictable parts and tools. If anything is slightly off, the machine cannot function correctly and the production line must be stopped. Due to these inefficiencies, excessive automation can increase costs and lengthen production schedules.
On the other hand, relying solely on human workers to handle large, unwieldy parts can make their work straining, slow-moving, and dangerous. Constant, repetitive motions can lead to repetitive stress injuries. Additionally, exhausted and uncomfortable workers are more liable to make mistakes, decreasing quality and productivity.
Working together
The idea of a fully automated “lights-out factory” with no production workers—one requiring only machine programming and maintenance—has proven to be a dead end. So much of what happens in a factory requires human ingenuity, learning, and adaptability. As products have become more varied and customized to local markets and customer needs, the economics of full automation make no sense. The immense engineering costs and time required to bring up a fully automated line for a complex product can never be amortized before the product needs to be changed.
The best choice is to combine the strength, precision, and speed of industrial robots with the ingenuity, judgment, and dexterity of human workers. This way, human workers can take on tasks that require flexibility, while the robots handle tasks that make the best use of their strength and speed.
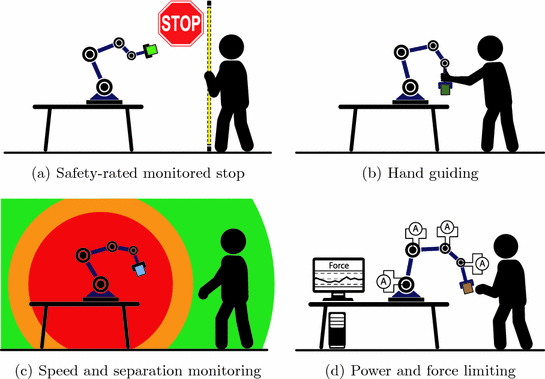
Manufacturing processes are faster, more efficient, and more cost-effective when humans and robots work together. In a study conducted by MIT’s Julie Shah, idle time is reduced by 85% when people work collaboratively with a human-aware robot compared to when working in all-human teams. Our own work at Veo finds that the cycle time for a simple assembly task can be roughly halved using human-robot collaboration as opposed to only humans. In a case study of solutions for packing boxes onto pallets conducted with Advanced Robotics for Manufacturing (ARM), we found that a collaborative approach cuts cycle time by almost two-thirds compared to a fully manual approach.
Additionally, while excessive and rigid automation today makes retooling an onerous and lengthy process, the flexibility of human-robot collaboration allows manufacturers to easily adapt to shifting demand with new products and processes. In our palletizing case study, we find that the fully automated process can take days or even weeks to reprogram and fit with additional fixturing—this downtime is costly. The collaborative approach benefits from the inherent adaptability of human workers, and only requires a day or perhaps a few days for some reprogramming of the palletizing robot arm.
Changes ahead
The advantages of robot-human collaboration were already known before the COVID-19 pandemic, but the crisis has made it even more necessary to join forces. Factories that are flexible enough to keep up with market demands could have the ability to quickly pivot from producing automotive components to medical equipment and back again. Factories that don’t have this flexibility as part of their design would struggle with such rapid change.
What’s more, as manufacturers begin to reopen their facilities, they will need to implement safe social distancing practices. Processes built for human-machine collaboration will be a major advantage. For example, a process step that involved two or more production workers working closely together may be split into multiple process steps, or it may turn into a process step that involves one worker and one robot.
We will likely also see more supply diversification. Instead of sourcing a component from a single supplier, a manufacturer may instead solicit smaller orders from a variety of suppliers in different locations to mitigate potential supply chain shocks (like those seen in March as the pandemic moved across Asia). These new lines will each have shorter runs of particular components. It makes little sense to design and implement expensive, fully automated systems for such short runs. Instead, the solution is to employ human workers and use automation efficiently.
Manufacturers can use this as an opportunity to reevaluate their production processes. Now that enabling technologies for safe human-robot collaboration are becoming widely available, it’s the perfect time to restructure factories around collaborative automation that helps keep workers safe and improve factory economics. Many auto and durable goods manufacturers are already taking steps to incorporate systems for safe collaboration, such as Veo FreeMove. Now it’s time for the rest of the manufacturing industry to follow suit.
Some imperatives remain clear: the improvement of living standards and the improvement of working conditions are crucial. As the pandemic has shown, advancements such as modern medical devices depend on increased productivity in manufacturing and continued advances in the quality, availability, and suitability of manufactured goods. This can be accomplished together with improved safety and ergonomics for production workers by making machines aware of and responsive to the presence of workers around them.
Don't miss any update on this topic
Create a free account and access your personalized content collection with our latest publications and analyses.
License and Republishing
World Economic Forum articles may be republished in accordance with the Creative Commons Attribution-NonCommercial-NoDerivatives 4.0 International Public License, and in accordance with our Terms of Use.
The views expressed in this article are those of the author alone and not the World Economic Forum.
Related topics:
Forum Stories newsletter
Bringing you weekly curated insights and analysis on the global issues that matter.
More on Emerging TechnologiesSee all
Elena Fersman
May 14, 2025
Rya G. Kuewor
May 13, 2025
Tea Trumbic and Dhivya O’Connor
May 13, 2025
Anurag Sinha
May 9, 2025
Jake Okechukwu Effoduh
May 7, 2025