Are 'mangineers' the future of lean manufacturing?
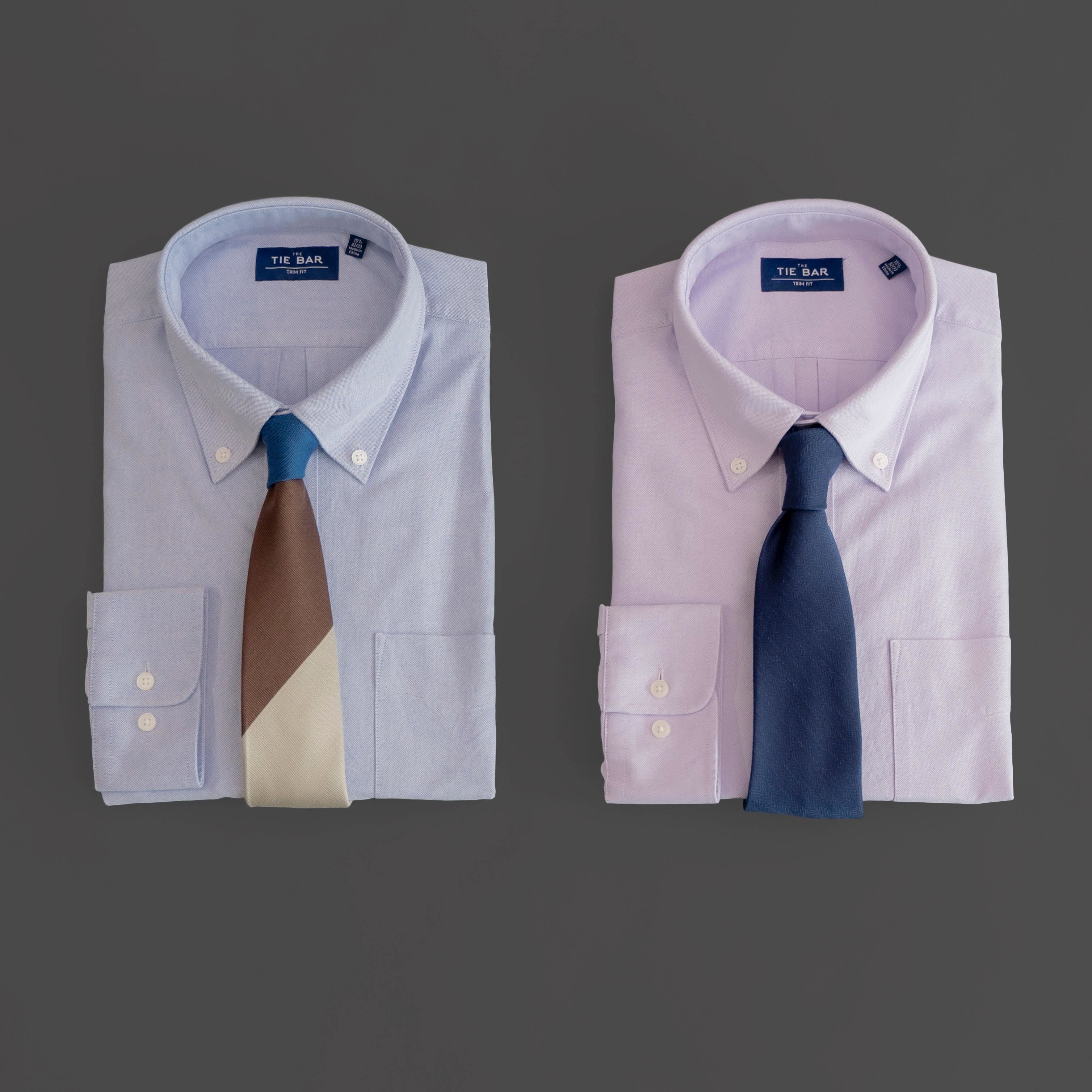
Mangineers: the best of both worlds
Image: Benjamin Rascoe / Unsplash
Stay up to date:
Advanced Manufacturing
- The pandemic has forced many manufacturers to accelerate their efforts to increase operational efficiency.
- A Hong Kong-based apparel manufacturer has been training new engineering recruits in management - this new, combined role is known as a 'mangineer'.
- This has re-engineered operations across the company's factory and maximised its efficiency.
The painful impacts of the COVID-19 have been felt by markets across the globe. Textile and apparel manufacturing is among the industries that have been hit heavily by the pandemic, due to a drop in customer demand, cost-control pressures and troubled trade relationships. To shore up their resilience, many companies have been trying to introduce innovations to increase agility and efficiency in operations.
One apparel manufacturer has been exploring innovative approaches to staying 'lean'; that is, minimizing waste in manufacturing while simultaneously maximizing productivity.
Esquel Group, one of the world’s biggest shirt makers, realized early on the challenges involved in meeting increasing customer requirements for a broad range of product to be delivered in shorter lead times. Esquel Specialty Spinning (ESS) – part of Esquel Group's vertically integrated supply chain that supplies the group's global factories and other customers with specialty yarns – has been experimenting with and implementing lean and agile operational concepts for many years. One key ingredient in the success of ESS' flagship operation in Guilin, China, is what Esquel calls the 'mangineer' programme.
Championed by Tian Ye, Managing Director of ESS, the mangineer concept welds together the traditional roles of a manager and an engineer. The result is a new cohort of trained professionals who wear many hats; they are capable not just of overseeing routine machine operations, but can also supervise quality control, ensuring production safety, and – above all – onsite, cross-functional project management.
Operational efficiency is the key to competitiveness
Designed to meet the demands of increasingly complicated and ever-changing production scenarios, the mangineer programme hinges on two principles – decentralized management and centralized control.
1. Decentralized management empowers each mangineer with responsibility for all aspects of production in his or her designated zone within the factory, including planning, machinery operation, quality assurance and resolving technical issues. Every mangineer is equipped with the skillset and authority to manage all scenarios without supervision. Compared to the traditional model, decentralized management greatly cuts down the time and labour needed for each task, saves manufacturing costs, and elevates productivity. For example, to change a machine setting, the traditional process involves 10 steps and requires coordination among different departments, which takes an average of 59 minutes. With mangineers taking up the task, there is no need to coordinate between departments; the process can instead be boiled down to four steps and completed within 25 minutes.
2. The centralized control system of the factory, upon detecting any problems in the automated production process, will dispatch onsite mangineers to the location where problems occur, based on their skills and workloads, as well as the urgency of the task. This combines process automation with the flexibility of human intervention. The agile system manages an optimal balance between staff capacity and efficient troubleshooting. Mangineers are subsequently assessed based on comprehensive key performance indicators (KPIs) that take into account labour intensity and employee happiness. If this was to be done traditionally, tasks would have to be assessed and assigned manually to different departments, and precious time would be wasted on cross-functional communication and approvals.
The combination of these two approaches has reengineered the production process across the entire Guilin factory, maximizing its operational efficiency.
A few years into the mangineer programme, output per capita at ESS in Guilin has increased by 329%, from 30kg to 130kg/day. The headcount per 10,000 spindles has reduced by 74% from 146 to 38, which is well above the industry benchmark. The time spent upgrading employees’ skills has decreased by 70%, while their take-home pay has steadily increased.
Cultivating the right team with well-rounded skills
In 2015, Esquel recruited more than 150 college graduates to the programme, most of whom came from engineering backgrounds. These fresh talents received one year of basic skills training, and then underwent a simulation workshop to acquire hands-on experience of different production scenarios. Their engineering skills were put to the test when they handled the setup of all newly imported machines before production began at the factory in 2018.
To motivate the mangineers, the programme constantly assesses them through an advancement ladder that consists of five rungs. Top-performing mangineers at the highest rungs were rewarded with exchange programmes at other Esquel factories and more managerial responsibilities.
We believe the mangineer concept could be a cornerstone for the future of apparel manufacturing.
Accept our marketing cookies to access this content.
These cookies are currently disabled in your browser.
A sustainable company cannot become what it aspires by remaining where it is
Faced with ever increasing socio-economic uncertainties, modern manufacturers need to constantly reinterpret the concept of 'lean' so that it is resilient to changes. With a goal to move closer to zero emissions, Esquel is also working hard to bring together lean and green, by implementing technologies that reduce its energy and water consumption in its operations.
The mangineer programme could have application potential for companies across a vast array of industries in search of leaner and more agile models. Inspired by Esquel’s success, two leading machine manufacturers based in Europe, both suppliers to Esquel, have just embarked on the journey to set up their own mangineer programmes.
As the world painfully yet slowly recovers from the pandemic, the manufacturing industry will become less siloed, and major players will need to broker systematic changes to thrive. Programmes like the mangineer might just have the potential and potency to revolutionize the manufacturing industry and shape the future of work.
Don't miss any update on this topic
Create a free account and access your personalized content collection with our latest publications and analyses.
License and Republishing
World Economic Forum articles may be republished in accordance with the Creative Commons Attribution-NonCommercial-NoDerivatives 4.0 International Public License, and in accordance with our Terms of Use.
The views expressed in this article are those of the author alone and not the World Economic Forum.
Related topics:
Forum Stories newsletter
Bringing you weekly curated insights and analysis on the global issues that matter.
More on Manufacturing and Value ChainsSee all
Ulrich Scherbel
April 1, 2025
Nii Simmonds and Nii Ahele Nunoo
March 6, 2025
Benedikt Gieger and Dominik Metzger
March 3, 2025
César Dugast and Ana Luiza Sanches
March 3, 2025