How digital twins will troubleshoot – and even help design – the buildings of the future
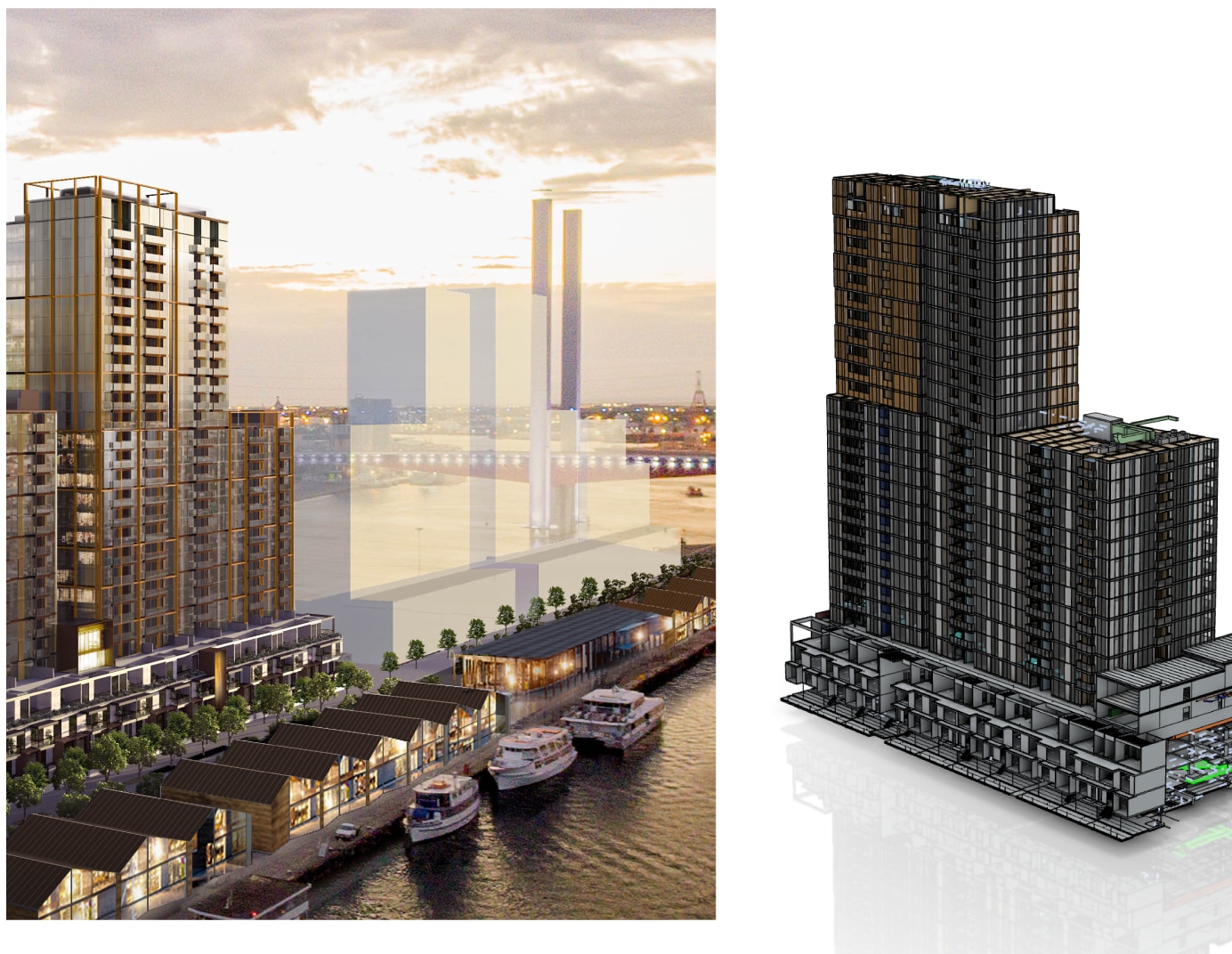
Digital twins are exact replicas of physical buildings to be constructed – allowing their optimization.
Image: Lendlease
Stay up to date:
Real Estate
• Real-estate productivity is falling as demand for buildings is increasing.
• With proven benefits in other industries, the real-estate industry is beginning to adopt the use of digital twins in construction.
• Digital twins can save millions in construction costs and help test the viability of new materials.
It’s widely recognized that the real-estate industry needs to change its practices. Our productivity has fallen by 19% during the past 50 years, while the average productivity of all other industries has increased by 153%. Our inability to lock in productivity gains has occurred at the same time demand for our services is increasing exponentially - especially as more people move from rural to urban areas. With the overall growth of the world’s population, another 2.5 billion people will need accommodation in urban areas by 2050. Cities around the world are challenged with building quality property fast enough, building affordably while managing the impact of cities on the natural environment.
During the past decade, a wide range of digital solutions have emerged, with the ambition of improving productivity and quality by automating our largely manual, disaggregated and complex design, procurement and construction processes. The amount of investment into construction tech has grown exponentially, with $10 billion in investment funding from 2011 through early 2017. Technologies like building information modelling (BIM) are increasingly used throughout the industry globally. These solutions have enabled the start of the digital journey, but more is needed for the industry to realize the benefit of this investment.
So how have other industries managed to produce better-quality products, faster, while reducing cost? The automotive, aerospace and industrial sectors have been realizing impressive benefits by using digital twin technology for decades. In the case of construction, for example, a digital twin of a building is a digital version of its physical counterpart, right down to the smallest detail. The digital twin matches the behaviour and performance of its physical twin. Building materials in digital twins behave as their physical counterparts do. These digital buildings can therefore be analyzed under various scenarios and optimized, essentially performing a digital rehearsal to fully resolve the building design and perfect its performance before it is physically built. Digital twins were initially used in aerospace and have been gradually adopted in other sectors.
General Electric (GE) has used digital twins to fundamentally change their process of designing, manufacturing and maintaining their products, including engines, power generation, oil and gas and medical imaging equipment. By doing so, GE has increased the reliability of some of their products by 93-99.49% in less than two years, reduced reactive maintenance by 40% in less than one year and avoided $11m in lost productivity costs . For example, GE Transportation (now Wabtec) has created the Trip Optimizer, a digital twin of its Evolution locomotive. The digital twin simulates the most efficient speed and acceleration profile of the train based on the weather conditions, the topography of the train tracks and the train’s scheduled arrival time. GE’s Train Optimizer enables fuel savings of 3-17%, or up to 32,000 gallons per engine annually.
In recent years, digital twin use has increased in property and construction, where the technology has demonstrated an impressive range and scale of benefits. A digital twin was developed for One Sydney Harbour, a Renzo Piano-designed residential development using the “approved for construction” design documents created by the design consultant teams, including models, 2D drawings, specifications and product tech data. The digital twin enabled unresolved design details and errors to be identified and resolved to a much finer level of detail than would have been achieved through a purely traditional approach and in a much shorter time frame. Digital twins used this way have saved millions of dollars in construction costs and reduced construction durations by months, while increasing the quality of the finished product.
Aside from the obvious efficiency of the technology, of even more value is that digital twins also allow us to explore a wide range of potential solutions that may never have been considered traditionally, enabling a step-change improvement in the quality and performance of buildings. For instance, the predictive nature of the digital twin can be used to test the suitability of new materials.
Digital twin technology was recently used to test and determine the viability of building a multistorey complex from sustainable timber in Melbourne, Australia. While this timber had been used previously in construction, it had not been tested in buildings of this height: namely, a 29-storey apartment tower. Digital twins therefore enable ongoing innovation in materials and sustainable designs to be modelled, and can even disclose the carbon footprint of a building before it is built. This is very important because the built environment accounts for 25-40% of the world’s total carbon emissions and buildings consume 25-40% of global energy. Given the volume of new property that needs to be built to accommodate the increase in urbanization, it’s important that the sustainability performance of property and construction improves; otherwise, meeting the demands of increased urbanization could have a disastrous impact on our environment.
Digital twins are particularly powerful when used in conjunction with “generative design”. Rather than using technology to help people design the building, the design is generated by automation software, in response to the design brief. Building options generated this way aren’t simply drawings. They are a fully resolved solution from an engineering, performance and financial perspective, meaning that they are buildable, compliant and financially viable.
Lendlease recently launched Podium, a digital platform for the real estate industry that harnesses the power of digital twins and generative design. Using the software, Lendlease has generated digital twins of buildings within several days, a process which would traditionally take a team of designers months to complete. Digital twins have therefore proven to make an important leap in productivity. Any improvement in productivity in the industry will have a major benefit for the world economy. Inefficiencies in property and construction are bad for the global economy, because they drive up the cost of construction, increasing the cost of infrastructure, property and houses. According to a recent study, a 1% reduction in construction costs would save society about $100 billion annually.
What is the World Economic Forum doing to support the Future of Real Estate?
The power of digital twins has been obvious since the early 2000s. So why are they only now starting to be used in property and construction? Over the years, digital twin technology has become more affordable, more powerful and vivid, creating more powerful simulations and increasing the value of the insights they bring. The power of digital twins in our industry is now becoming self-evident: We believe that digital twins can help us achieve cost savings of up to 20% and a hundredfold improvement in speed to market on new projects, creating significant social, economic and sustainability benefits.
Don't miss any update on this topic
Create a free account and access your personalized content collection with our latest publications and analyses.
License and Republishing
World Economic Forum articles may be republished in accordance with the Creative Commons Attribution-NonCommercial-NoDerivatives 4.0 International Public License, and in accordance with our Terms of Use.
The views expressed in this article are those of the author alone and not the World Economic Forum.
Forum Stories newsletter
Bringing you weekly curated insights and analysis on the global issues that matter.
More on Emerging TechnologiesSee all
Anurag Sinha
May 9, 2025
Jake Okechukwu Effoduh
May 7, 2025
Ti Hwei How
May 7, 2025
Adam Skali and Clementina Colombo
May 5, 2025