The automobile industry needs to steer in this direction for future success
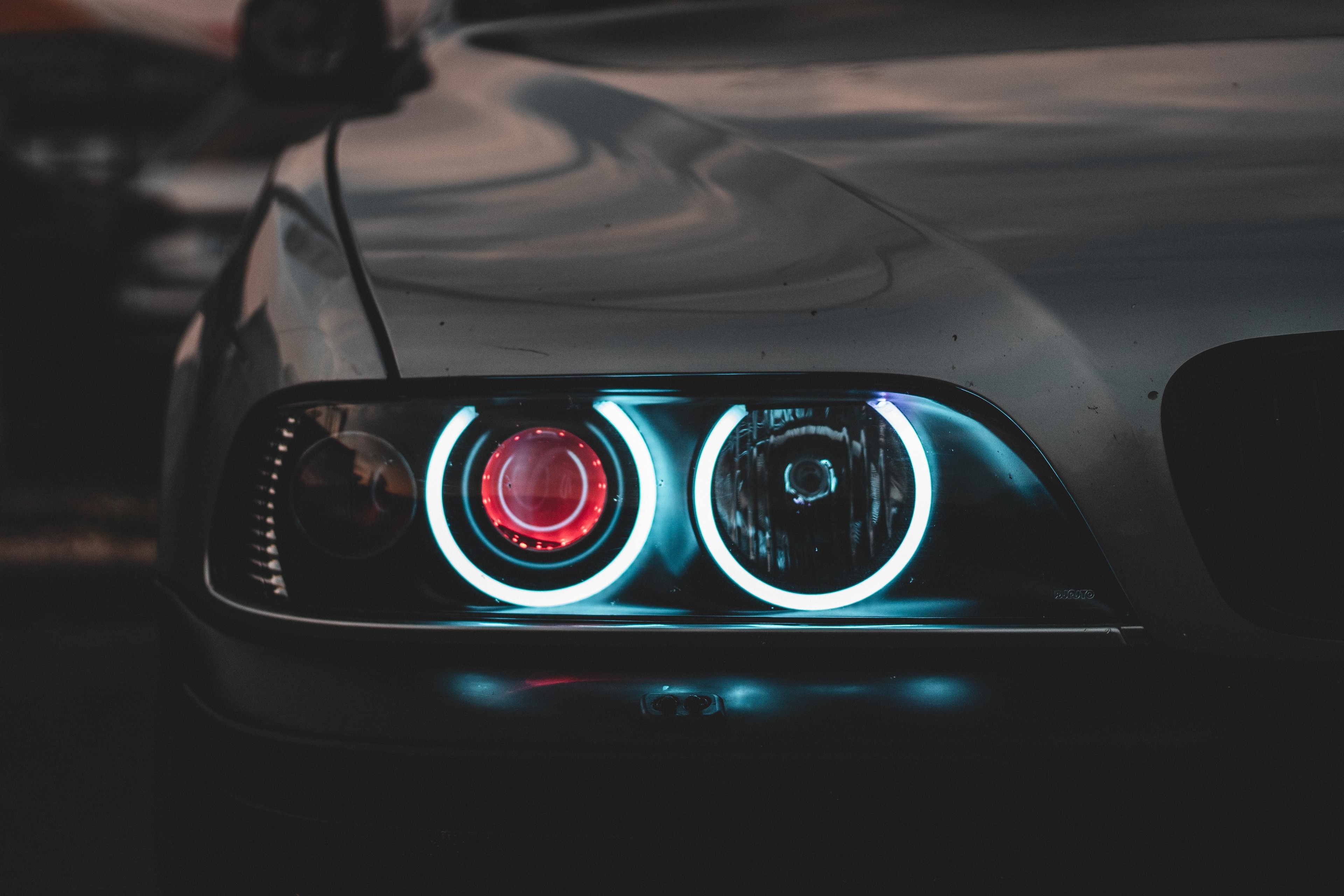
Using 3D printers to produce car parts can increase efficiency, reduce costs and make supply chains more resilient.
Image: Richard Biros/Unsplash
Noel Nevshehir
Director, International Business Services and Global Strategic Partnerships, Automation AlleyStay up to date:
Mobility Solutions
- The automotive industry needs to become digitalised.
- Manufacturers will enjoy increased efficiency and productivity by embracing Industry 4.0.
- Automotive manufacturers and downstream suppliers need to implement change management strategies.
Automotive companies have spent the best part of a century investing billions into their enterprise systems. It's now time they kept pace with the digital revolution of Industry 4.0. What's more, this is critical to their survival.
Original equipment manufacturers (OEMs), and tier 1 manufacturers in particular, must begin to acknowledge the responsibility they have in supporting their downstream suppliers in becoming Industry 4.0 proficient.
The digital transformation of today requires a complete culture shift, involving automakers and auto suppliers investing in change-management strategies that realign the entire supply chain.
In January 2020, General Motors announced it was investing $2.2 billion into its Detroit-Hamtramck assembly plant, since renamed Factory ZERO (zero crashes, zero emissions and zero congestion).
This was a start; the aim was to produce a variety of all-electric trucks and SUVs. However, the pandemic should have served as a greater wake-up call for the industry than so far seems the case.
The raw computational power and foundational technologies supporting Industry 4.0 include artificial intelligence and Big Data, the Internet of Things (IoT), cloud computing, augmented and virtual reality, advanced robotics, 3D printing and cybersecurity.
Change management strategies that automotive manufacturers and downstream suppliers can implement include small, option-like bets and modest investments with the potential for large payoffs.
”Manufacturers that go down this path enjoy increased efficiency and productivity, improved product quality and processes, operating cost reductions, greater supply chain visibility, accelerated innovation and speed to market of new products, services and technologies.
Embracing this tech also revolutionises the role labor plays in the economy.
No pain, no gain
Creatively destructing a company in the face of new realities can be painful. But it is entirely necessary, and especially so considering the shorter lifecycles of today’s technologies as they grow even more sophisticated, complex and exponential.
History proves the long-term benefits of adopting new technologies and processes, and those benefits far outweigh their initial barriers. Change management strategies that automotive manufacturers and downstream suppliers can implement include small, option-like bets and modest investments with the potential for large payoffs.
Change needs to trickle through though, and not be an avalanche of inputs. In this way, people and systems will prove able to absorb new technologies gradually and accept new ways of doing things without being overwhelmed by complexity. Once a company realises returns on their investments, it can incrementally integrate further technologies and processes.
3D printers for automotive suppliers
One example of this approach working successfully is Automation Alley’s Project DIAMOnD, which has seen 300 3D printers distributed to manufacturers across Oakland and Macomb Counties – a Southeast Michigan region filled with automotive suppliers of all sizes and levels of sophistication.
Project DIAMOnD has created the largest independent and distributed 3D-printing network in the world operating on a blockchain technology platform to address the urgent need to move companies to Industry 4.0.
One of the firms involved, Rochester Hills, Michigan-based Air & Liquid Systems – a tier 2 automotive supplier with 40 employees and an annual revenue of $20 million – is using its 3D printer to print a part that was previously made of stainless steel and cost $100. It now costs them only $1 to make out of carbon fiber.
Their printer is placed near the engineers to make them more curious about what else they can create, shifting the way they think about production and their business. For the company CEO, Jim Miller, it was exciting to see the culture change of integrating into manufacturing new technology that positions the organization for gains on its journey to Industry 4.0.
Similarly, Josh Tucker of Shelby Township Michigan-based Tucker Induction System, was surprised by how quickly his company was able to produce 3D-printed parts that proved to withstand tension, heat, and other forces seen in real-world scenarios.
The company is a Tier 3 automotive supplier with 17 employees and an annual revenue of $3 million. They are now 3D printing some parts that were previously produced using subtractive manufacturing methods and also using 3D printing to develop completely new solutions. “This technology is not just for prototyping. You can actually print parts and put them out in the field,” Tucker said.
The hope is that rapid advancements in technology will shift some manufacturing back to the US.
”Investment in digital technologies to upgrade or enhance legacy systems, like the 3D printing examples above, are not only good for increased efficiency and cost reductions, but also for supply chain resilience.
Supply chain benefits
We have seen how trade disputes, COVID-19 and other unforeseen circumstances have caused supply bottlenecks for auto manufacturers in the areas of rare earth materials, semiconductors and personal protective equipment. It has reversed some of globalisation’s gains, while hastening the insourcing of production.
It will take years for the US to reconstruct a domestic ecosystem of suppliers and a network of skilled workers hollowed out during the trend to offshore production. The hope is that rapid advancements in technology will shift some manufacturing back to the US and create a multitude of well-paying local jobs.
The implications for the world economy are also enormous. According to ING, 3D printing alone is projected to reduce global trade flows by 40% by 2040.
Domesticate or diversify?
A recent article in The Economist suggests that the “way to make supply chains more resilient is not to domesticate them, which concentrates risk and forfeits economies of scale, but to diversify them.” This is especially true in the case of auto companies that are obliged to build in the countries where they sell their production. That said, this view may hint at some blind spots regarding the degree to which natural disasters, diseases and trade wars have disrupted supplies chains.
What is indisputable is the urgency for manufacturers to embrace the emerging technologies their competitors have already deployed in factories.
The pandemic has provided forward-thinking business leaders with the ammunition they may have needed to create change from within, in response to extenuating circumstances imposed from without.
Indeed, many enterprises have vaulted their digital transformation forward five years in the matter of 14 months during the pandemic crisis — a silver lining that was just aspirational at the end of 2019. For its part, the auto industry and its largest suppliers need to lead their broader supply chain to a sustained transformation to Industry 4.0, despite the fact that the pandemic – and the urgency it wrought – is starting to ebb.
Don't miss any update on this topic
Create a free account and access your personalized content collection with our latest publications and analyses.
License and Republishing
World Economic Forum articles may be republished in accordance with the Creative Commons Attribution-NonCommercial-NoDerivatives 4.0 International Public License, and in accordance with our Terms of Use.
The views expressed in this article are those of the author alone and not the World Economic Forum.
Forum Stories newsletter
Bringing you weekly curated insights and analysis on the global issues that matter.
More on Fourth Industrial RevolutionSee all
Mohammad Isham Jaafar and Gong Yingying
July 22, 2025
Neeka Mashouf and Leila Mashouf
July 15, 2025