Here's how green steel could lower trucking industry emissions
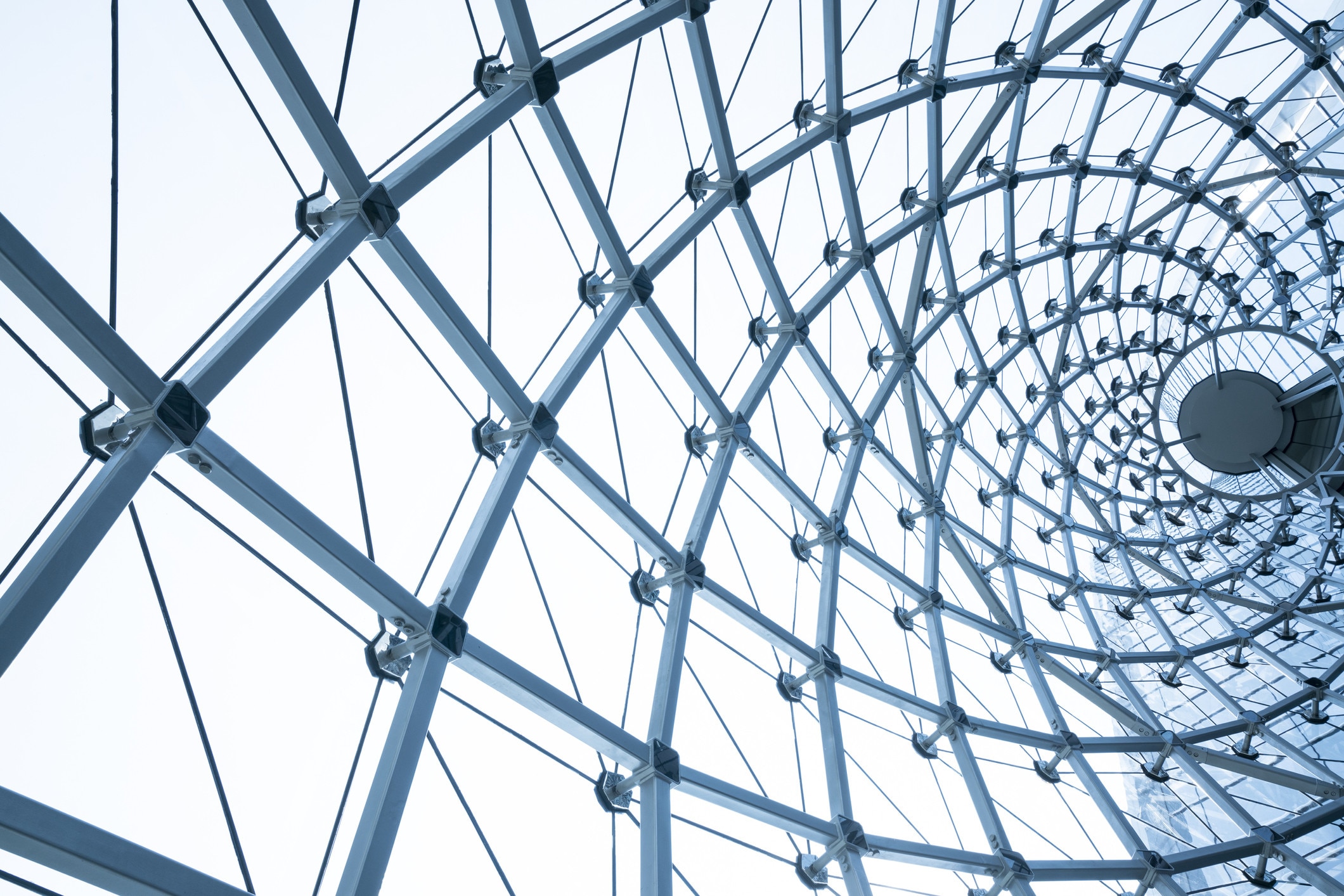
Buyers fear there won’t be a sufficient supply of green steel to go around.
Image: Getty Images/iStockphoto
Stay up to date:
Mining and Metals
- Steel is absolutely essential across a variety of industries and in our daily lives, but its production is responsible for 8% of total carbon dioxide emissions.
- "Green steel" could be the answer to this problem and betting on it now is risky — but that hasn't stopped some key players in the trucking industry moving first.
- World Economic Forum’s First Movers Coalition aims to encourage more industry heavyweights to boldly pursue the net-zero transition.
Steel is one of the most versatile materials on earth — used in the manufacture of countless everyday tools, from razor blades and bicycles to trucks and wind turbines. But manufacturing this shiny, ductile metal is a dirty, old-fashioned process that’s changed little in the past 150 years.
Given that steel accounts for around 8% of total global carbon dioxide emissions, finding cleaner, commercially viable ways to make it is a vital task. To meet global net-zero goals, steel industry emissions must fall by at least half by 2050, according to the International Energy Agency.
Carbon debt shifts from tailpipe to supply chain
Trucking has a large appetite for steel, with about five metric tons of the metal in each vehicle. Roughly 23 million heavy buses, trucks and light commercial vehicles were produced worldwide in 2021, and demand is expected to grow. These volumes position the sector well to drive change in the steel industry.
Meanwhile, more vehicles are going electric. Scania, for example, has a target to electrify half the trucks it sells by 2030. But as these battery electric vehicles (BEVs) run on green electricity, so the share of each truck’s life-cycle carbon emissions coming from the manufacturing process climbs to around 85%. This means that, within just a few years, the carbon debt of leading truck makers will shift from the tailpipe to the supply chain.
Three millennia of technology — transformed in a decade
So how should companies go about sourcing “green steel”?
There are a dozen or more different technologies being trialed to get around the root of the problem — that making steel the traditional way uses a lot of fossil fuels.
Some innovations employ natural gas as a transition fuel, others propose to intercept emissions from smokestacks using carbon capture and storage. Greater use of scrap in conjunction with renewables is also a green option. But in a sector awash with acronyms, one of the most promising technologies to make new, high-quality flat steel from iron ore is known as “H2 DRI + EAF.” To the uninitiated, this may require a bit of explaining, and a (very) brief trip back in time — to the Iron Age.
About 3,000 years ago, our ancestors discovered that heating rock rich in iron over a charcoal fire rendered a liquid metal that, when cooled, became malleable. Most of today’s iron is made using the same principle: melt the ore (with lime) in a huge blast furnace powered by coking coal to over 1,600°C, and out comes the liquid iron. The problem is that the oxygen released by the ore binds with the carbon in the coke to emit huge quantities of CO2 — between one and three metric tons of the gas for every metric ton of steel produced. And global steel production is close to two billion metric tons a year.
This is where DRI, or “direct reduced iron,” comes in. The coke is replaced as a combustion fuel by hydrogen, which creates iron while emitting water as a byproduct instead of carbon dioxide. For this process to qualify as “green steel,” it’s essential that the hydrogen itself is produced with non-fossil energy — and a lot of it, as we shall see. The second phase is to heat the iron again (without coke) to decrease its carbon content and thereby form steel, a process little changed since the 1850s. For this stage, the EAF, or “electric arc furnace,” replaces the usual, more carbon-intensive “basic oxygen” furnace.
First movers on the dancefloor
While most major steel producers in developed markets are experimenting with DRI-EAF processes, the technology remains expensive and niche. This is where the World Economic Forum’s First Movers Coalition (FMC) aims to make a difference. The FMC is a global initiative to harness the purchasing power of companies to decarbonize seven “hard-to-abate” industrial sectors that account for 30% of global emissions. As the technology to achieve this decarbonization is very much in its youth, the “first movers” are — to adopt a youthful analogy — the first to hit the dancefloor, demonstrating there is demand and encouraging a supply of partners to join them.
Scania’s first move, for example, is a commitment from its European operations to ensure 100% of its steel purchases are green by 2030, sending a strong demand signal to steel suppliers that there is a market for this product. It sounds bold — and risky. You’re effectively agreeing to pay a supplier a premium price for a product that doesn’t yet exist in the form you need it. It’s enough to keep any chief procurement officer awake at night.
So how can these risks be hedged? There are a number of ways. You can enter into advance purchase or offtake agreements with your future suppliers of green steel. These don’t necessarily have to specify a fixed price in advance, but they do seek to define which indices and mechanisms should be used to determine that price. This helps share the risks between supplier and purchaser.
Another model is to invest in the companies that are developing the technology. For example, Scania has invested in H2 Green Steel, a startup that’s targeting a 95% reduction in CO2 emissions compared to traditional steelmaking. The advantage of this model is that you can work with the supplier on research and development to ensure the product is optimal for your application. Whichever model you choose, the aim is to give innovative companies peace of mind so they can continue to develop the technology that hard-to-abate sectors so badly need.
What’s the World Economic Forum doing about climate change?
The risks of investing in green steel may seem huge…
The challenges on this journey should not be underestimated. Volume and price are two critical metrics.
Buyers fear there won’t be a sufficient supply of green steel to go around. Suppliers fear that if they move too fast (and the technology is leaping forwards in orders of magnitude), they risk flooding the market. But like at any school dance, everyone has to take a risk with their first moves or go home. Nothing ventured, nothing gained.
And then there’s the price. How much higher it might be is hard to foresee. Swedish steel manufacturer SSAB has put the initial green premium at 20-30%, though this should come down as volumes increase. Whether truck makers can pass on that premium to customers is another question. But look at it this way: if a buyer is sufficiently climate-aware to opt for a BEV, it would make sense for it to be concerned about the carbon footprint of the materials too.
There is also the known unknown of regulation. Governments are increasingly taking measures to tax carbon-intensive industrial processes or incentivize low-carbon alternatives. Europe, for example, has since 2005 put a price on carbon with its Emissions Trading System (ETS) and recently proposed a Carbon Border Adjustment Mechanism. Meanwhile in the U.S., President Biden’s Inflation Reduction Act offers billions in tax credits for climate-friendly technologies including renewables and green hydrogen.
Renewables are a key part of this puzzle. A huge amount of non-fossil energy — whether renewable or nuclear — is needed to run the electrolyzers that manufacture the green hydrogen demanded by the DRI-EAF process. To produce the entire global supply of steel using green hydrogen would require — according to one estimate — nearly doubling the world’s annual fossil-free electricity capacity. Sweden, Scania’s home, is well-placed in this regard, as more than 90% of its grid is already fossil free. But a shortage of clean power in developing markets is hampering the large-scale adoption of green steel technologies.
…but the opportunities are bigger still
Amid all these challenges, let’s not forget the great opportunities here. Principal among these is the need for industry to secure the materials of the future.
In any war-gaming of the global economy over the coming decades, there is not one scenario where climate change will go away or where materials made with fossil fuels will continue to be both cheap and available. Everything points towards a world without carbon emissions, where the pressures on our climate put a squeeze on supplies of materials and increase the risk of regulatory penalties. We’re already seeing the signs — from the EU’s incipient legislation to questions in tender bids around the life-cycle emissions of industrial products.
Getting started on developing green emissions materials is clearly the right thing to do. It’s a way to future-proof your business, while helping deliver the untold benefits to our climate, to nature and to society that a lower-carbon world brings.
Jonathan Walter and Andrew Alcorta contributed to this article.
Accept our marketing cookies to access this content.
These cookies are currently disabled in your browser.
Don't miss any update on this topic
Create a free account and access your personalized content collection with our latest publications and analyses.
License and Republishing
World Economic Forum articles may be republished in accordance with the Creative Commons Attribution-NonCommercial-NoDerivatives 4.0 International Public License, and in accordance with our Terms of Use.
The views expressed in this article are those of the author alone and not the World Economic Forum.
Forum Stories newsletter
Bringing you weekly curated insights and analysis on the global issues that matter.
More on Manufacturing and Value ChainsSee all
Maximiliano Frey
May 21, 2025
Jane Thoning Callesen
May 20, 2025
Madeleine North
May 13, 2025