What is steel scrap and how can it help us reach net zero?
Recycled steel scrap is a low-emitting source of the metal - here's how we can improve its collection and production to help decarbonize the industry.
Image: Reuters/Fayaz Aziz
Stay up to date:
Mining and Metals
Listen to the article
- Demand for steel is still growing, especially in the developing world.
- Recycled steel scrap is a low-emitting source of the metal – but the majority of available material is already collected.
- Further optimizing steel scrap recovery will be crucial in decarbonizing steel production.
From bridges to cars to paper clips, steel is ubiquitous in our material world. It is one of the enabling materials that has led to unprecedented living standard rises and progress for humanity. Yet, as with all other emitting economic sectors and material groups, the steel industry needs to decarbonize to meet the climate challenge. Its success as a material means global crude steel production is over 1.9 gigatonnes, but it accounts for an estimated 3 gigatonnes of CO2 emissions annually (albeit this is lower-emitting than most other materials potentially used for the same applications).
Steel is made from either primary sources: that is, extracting iron ore from nature and transforming it into pure iron; or from secondary sources, that is, remelting steel scrap into new steel, or a combination of both. This secondary-source steel scrap is the discarded steel that becomes available from manufacturing waste generation and from recovered steel in buildings, infrastructure, equipment, vehicles and products discarded at their end of life.
The amount of steel scrap available globally is finite, constrained by the rate of disposal by society. In contrast, the availability of iron ore-based steel is expandable, as mine activity can be increased to meet growing steel demand.
Innate circularity
Steel has excellent circularity properties. Whereas other materials are often downcycled at their end of life, for many applications, steel scrap can be turned back repeatedly into new steel, retaining its original properties. The magnetic properties of steel make it easy to segregate steel scrap from mixed waste streams.
Global emissions from steel are primarily generated while producing steel from primary source iron ore, as coal and natural gas are generally used as energy and reductant. Producing steel from secondary source steel scrap uses mainly electricity and emits significantly less. In fact, producing steel from secondary source steel scrap with clean electricity results in a very low-emitting circular material.
This bodes well for steel as the world transitions to a carbon-neutral circular economy, as steel will be increasingly favoured over other materials in overlapping applications with less circular and less carbon-neutral potential.
Global hunger for steel
The truth is that today much of the steel scrap that can be potentially recovered is recovered. Steel scrap has high intrinsic value as a substitute for the costly and emitting process of extracting iron ore and turning it into steel. Due to this intrinsic value as an input to make new steel and its ease of segregation, we estimate that globally 85-90% of steel arising from manufacturing processes waste and end-of-life buildings, infrastructure, equipment, vehicles and products is currently recovered as steel scrap to produce new steel.
The challenge to society is that steel demand is much greater than the steel scrap that is available to make new steel, with only an estimated quarter of steel demand met from steel scrap. Only when the world has sufficient buildings, infrastructure, equipment, vehicles and products to meet the needs of a fully developed world, will we be on a path to phase out iron-ore-based steel production and achieve full circularity generating sufficient steel scrap to meet demand. This will take time: though steel deployed in many mature economies has plateaued, there is still strong demand growth for steel in the developing world as they converge with developed world standards. The world is also in the middle of a transition to a carbon-neutral economy that will accelerate the replacement of many energy and manufacturing assets, infrastructure, and buildings globally. This will temporarily boost demand for materials, including steel.
We forecast global crude steel demand will increase from 1.9 billion tonnes in 2021 to over 2.6 billion tonnes annually by 2050 under current consumption patterns, even after considering significant material efficiency gain. Though by 2050 end of life steel scrap’s share in total steel production will have increased significantly, it will only account for around 44% global steel production. This is a challenge not only for steel but for all material groups.
Dealing with the steel scrap challenge
While recognizing the increasing role steel scrap-based production will have in decarbonizing the steel industry, in the horizon of 2050, we need to focus on decarbonizing iron ore-based steel production, as it will continue to be the primary source of steel over the coming decades. Decarbonizing iron ore-based steel production will require unprecedented levels of innovation and investment.
In this context, is there anything we can do further regarding steel scrap to support decarbonization, or do we have to wait decades for steel scrap to become increasingly available to replace iron ore-based steel production? The answer is that many things can and should be done today.
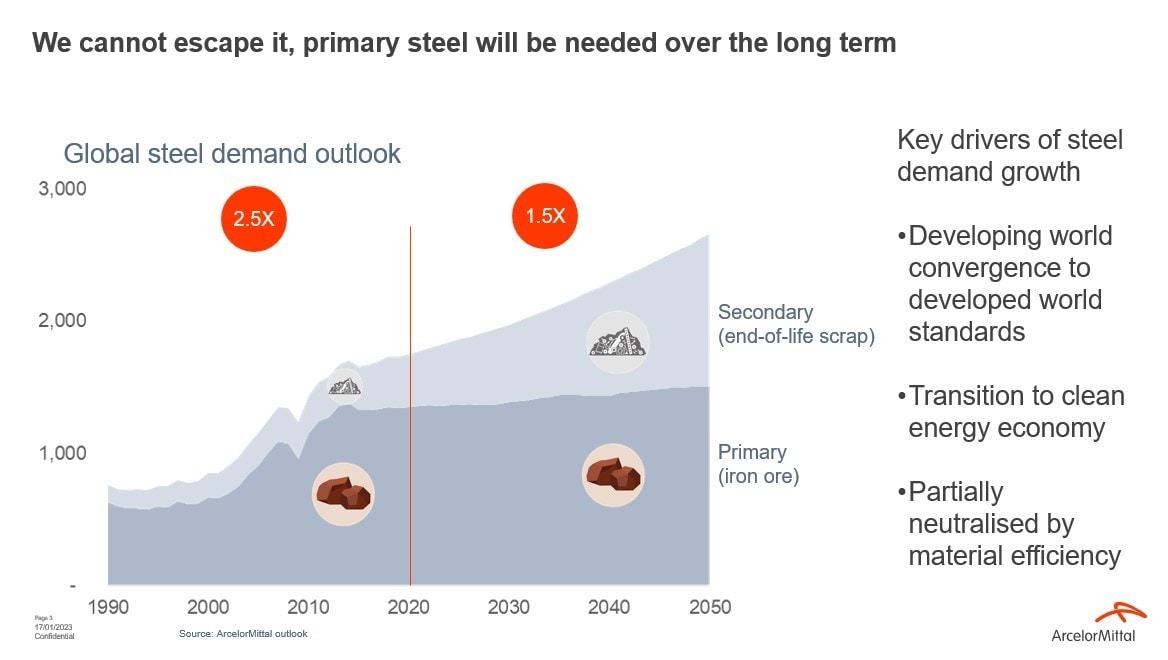
As mentioned, it is estimated that around 85-90% of steel scrap potential is recovered. This is a very high level of recovery, but based on the circularity and carbon-neutral credentials of scrap-based steel, we should strive towards even higher recovery rates. This can be done through improved waste management systems and innovative steel scrap recovery processes that can help bring recovery levels even higher.
Steel production from steel scrap is low-emitting if we use clean electricity in the main crude steel-making step, the electric arc furnace. Still, there are further decarbonization steps that steel scrap-based production can take to eliminate all remaining emissions. These include replacing fossil carbon injection in the electric arc furnace for biogenic carbon, and replacing natural gas use for heating in the steel rolling process with electrified heating or clean hydrogen.
We also need to expand the use of scrap-based steel in certain steel applications that have limitations today. For example, a producer of high-strength steel for a vehicle body that needs to meet crash safety standards would be reluctant to use general scrap-based steel, as the chemical specifications are tight and cannot be guaranteed with the use of current scrap-based steel. In such cases, efforts should be placed on better sorting of steel scrap from different waste streams to improve quality. Also, the pre-treatment of steel scrap to improve chemical composition should be developed and incentivized. Additionally, from the product point of view, specifications on steel applications should be adjusted where possible to increase the amount of steel-scrap-based content feasible for a product.
How is the World Economic Forum facilitating the transition to clean energy?
The steel industry has a significant challenge ahead to decarbonize the industry. Though increased scrap use alone will not be sufficient to meet a carbon-neutral steel industry by 2050, optimizing the use of steel scrap will be key to overall success.
Accept our marketing cookies to access this content.
These cookies are currently disabled in your browser.
Don't miss any update on this topic
Create a free account and access your personalized content collection with our latest publications and analyses.
License and Republishing
World Economic Forum articles may be republished in accordance with the Creative Commons Attribution-NonCommercial-NoDerivatives 4.0 International Public License, and in accordance with our Terms of Use.
The views expressed in this article are those of the author alone and not the World Economic Forum.
Related topics:
Forum Stories newsletter
Bringing you weekly curated insights and analysis on the global issues that matter.
More on Energy TransitionSee all
Roberto Bocca
May 9, 2025
Kesang Tashi Ukyab and Leo Simonovich
May 9, 2025
Nii Ahele Nunoo
May 6, 2025
Denise Rotondo and Chris Leong
May 5, 2025
Don McLean
May 1, 2025
Benjamin Denis and Justine Roche
April 30, 2025