How low-carbon aluminium can accelerate the journey to net zero
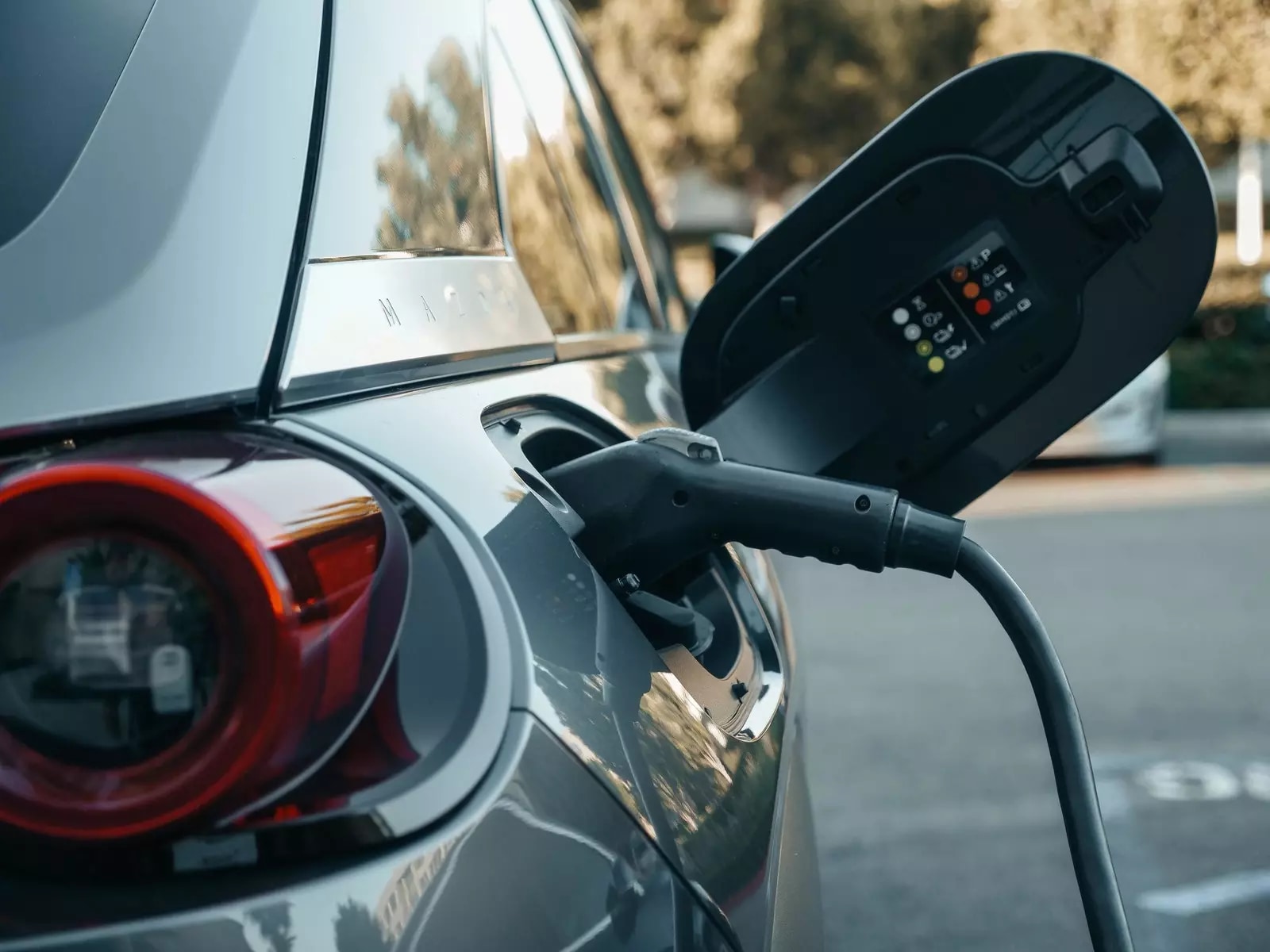
Using low-carbon aluminium in the production of electric cars could make the automotive industry greener.
Image: Pexels/ Kindel Media
Stay up to date:
Automotive and New Mobility
Listen to the article
- Electric cars might have zero emissions in use, but their manufacturing process has a larger environmental footprint than most people appreciate.
- Using low-carbon aluminium in the production of electric cars could make the automotive industry greener.
- To pave the way for zero-emissions production, like-minded actors across the value chain need to work together on material selection, recycling, transparency and traceability.
As the world is transitioning to electric mobility, the next big challenge for the automotive industry is to achieve emission-free car production. Because, while electric cars have zero emissions in use (assuming they are powered by renewable energy), they are far from climate neutral. People often overlook the fact that each car consists of approximately 50,000 components, each contributing its own emissions during production. That means that for an electric car to be genuinely zero-emission, all these 50,000 components must be emission-free too.
According to Polestar and Rivian’s recent Pathway report, the automotive industry must take action in several areas to hit 1.5 °C targets. Fully switching the entire global car park to battery electric vehicles (BEV) will not be enough; neither will powering all these vehicles with fossil-free energy. The only possible – but challenging – pathway to remain below 1.5 °C involves reducing supply chain emissions.
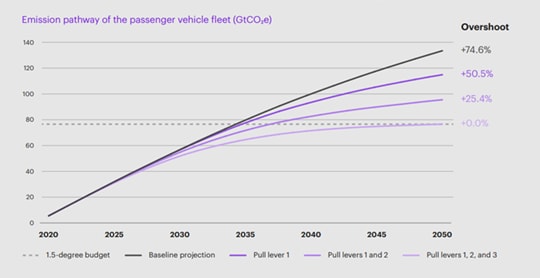
Today, steel, aluminium and plastics represent more than 80% of the embedded emissions of a car. And, perhaps surprisingly, the carbon footprint from materials is 40% larger for an electrical vehicle (EV) than for a traditional combustion engine car (ICE), much of that difference due to the battery. This means careful material selection is key, both to reduce emissions and increase recyclability, as well as considering dilemmas concerning the extraction of raw materials and its impact on people and nature.
Regulations going beyond tailpipe emissions
Governments around the world are aware of this and are introducing new measures targeted at the automotive industry, going beyond simply measuring tailpipe emissions. For example, by 2025, the EU will establish a common standard for assessing the full lifecycle CO2 emissions of cars. This is great news for the climate, but will require investment and technological developments from suppliers to the automotive industry, as well as the car companies themselves.
So how can we better work together across the supply chain to ensure responsibly sourced and zero-emission materials that can meet these new regulations and create true zero emission cars? It starts by looking at aluminium.
Using low-carbon aluminium in cars
Aluminium is becoming increasingly important as a lightweight material in electric vehicles, as it can reduce emissions and weight without compromising safety. A study by Hydro that investigates the environmental impact of a car throughout the entire lifecycle shows that lightweighting (using aluminium for a car’s structure can lessen weight by 30% compared to steel) and using low-carbon aluminium can make the automotive industry greener, as illustrated in the graph below. The complete recyclability of aluminium also means that single-use materials can be avoided. Today, more than 90% of aluminium contained in a scrapped car is recycled.
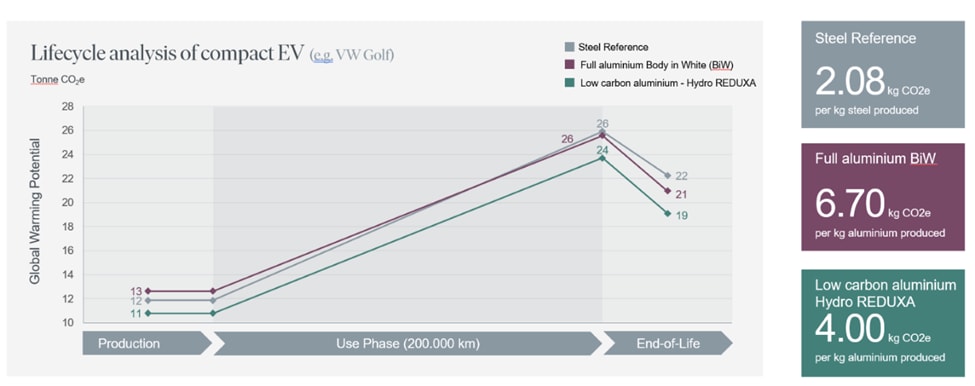
This means low-carbon aluminium has an important role in producing true zero-emission cars. But to pave the way for zero-emissions production, like-minded actors across the value chain need to work together on material selection, recycling, transparency and traceability. However, sustainability is not only about climate, but includes people and nature, too. Automotive makers and suppliers must also work together to ensure the materials are sourced in a responsible way for people and planet, considering the following:
1. Access to low-carbon materials that accelerate cuts in emissions
Considering that a car consists of approximately 50,000 components, each contributing its own emissions during production, access to low-carbon, responsibly sourced and recycled materials for all of these is key. And it matters where and how aluminium is produced. While the global average of aluminium is 18,6 kg CO2 per kilo of aluminium, this can go down to almost zero if we use post-consumer scrap aluminium as the raw material for the new component. The source of energy used to produce and remelt aluminum also matters. An aluminium plant powered by coal, as is common in several regions of the world, has five times higher CO2 emissions than one powered by renewable sources.
2. Demand traceability and radical transparency throughout the value chain
Today, there is a lack of transparency in the value chain when it comes to material and production footprint. It is important to understand where aluminium comes from, what energy source was used in its production, and if recycled, whether it consists of process scrap that has never been in use, or post-consumer scrap, that is aluminium that has had a useful life in a product and a footprint close to zero – in other words, whether it is truly recycled. That is why we need purchasers to ask for responsibly sourced aluminium with a proven low-carbon footprint, and suppliers to provide trustworthy information about the entire value chain. To create more sustainable solutions, we also need radical transparency regarding the origin of materials; common industry standards; regulations that drive and incentivize more post-consumer scrap; and more technological developments.
3. Ensure a just transition for all stakeholders
All materials have an environmental footprint; especially for raw materials requiring extraction, there are dilemmas when it comes to biodiversity and human rights. Since the shift to electric mobility is metal- and mineral-intensive, transparency and traceability are key to drive change in the industry.
Because, when problems are brought to light, they become difficult to overlook. The most important way we can drive change together is for buyers to know what questions to ask, and to ensure an open dialogue about the dilemmas and issues at play.
Accept our marketing cookies to access this content.
These cookies are currently disabled in your browser.
Don't miss any update on this topic
Create a free account and access your personalized content collection with our latest publications and analyses.
License and Republishing
World Economic Forum articles may be republished in accordance with the Creative Commons Attribution-NonCommercial-NoDerivatives 4.0 International Public License, and in accordance with our Terms of Use.
The views expressed in this article are those of the author alone and not the World Economic Forum.
Forum Stories newsletter
Bringing you weekly curated insights and analysis on the global issues that matter.
More on Climate ActionSee all
Tom Crowfoot
May 7, 2025
Nii Ahele Nunoo
May 6, 2025
Alfredo Giron
May 6, 2025
Denise Rotondo and Chris Leong
May 5, 2025