How technological advances are strengthening supply chains
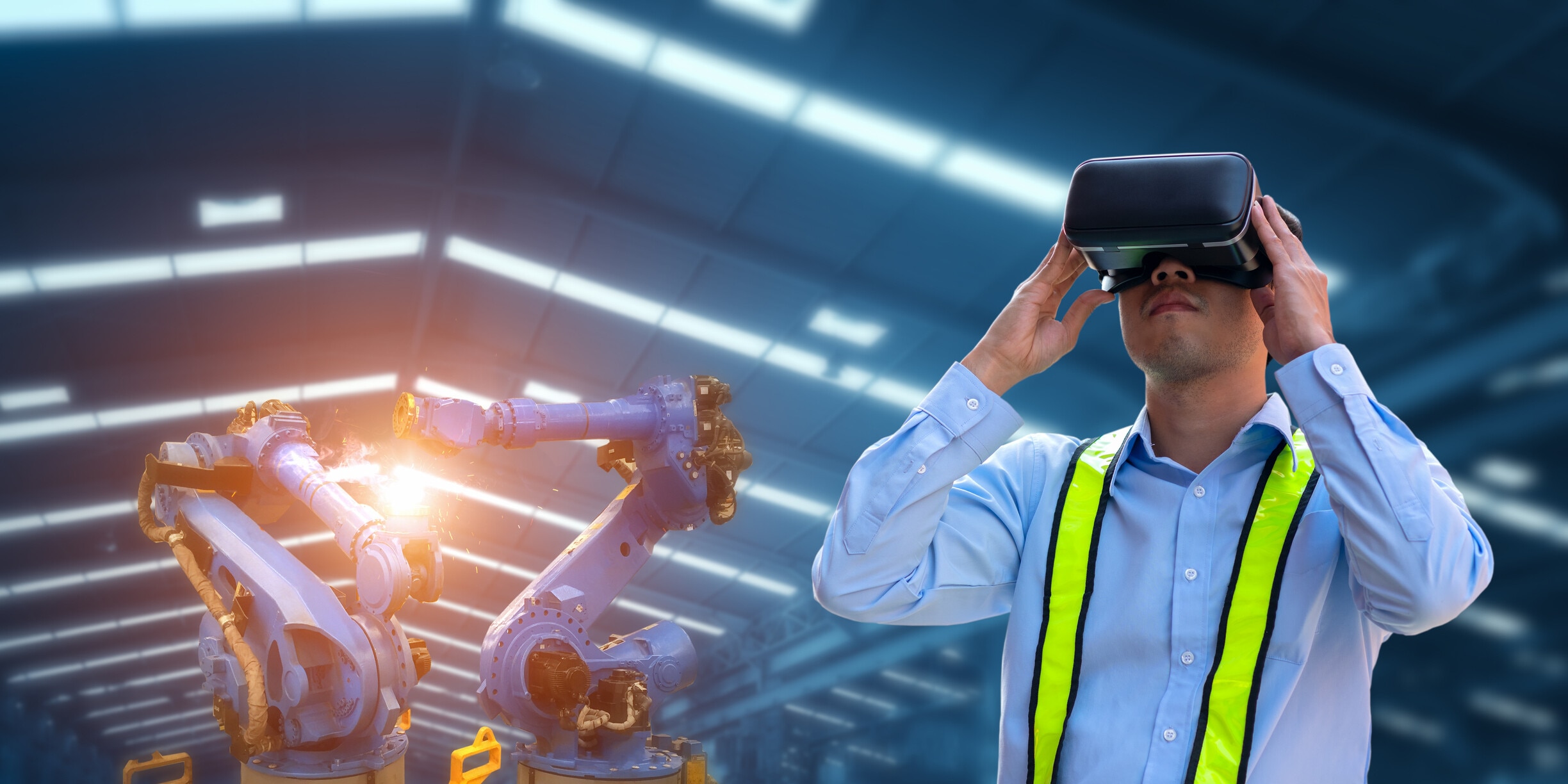
As industries seek to decarbonize, technological advances will also play a key role in managing changing supply chains.
Image: Getty Images/iStockphoto
Stay up to date:
Advanced Manufacturing and Supply Chains
- For decades, offshoring has been one of the primary strategies for many companies.
- Increasing labour productivity and higher demands on supply chain resilience have challenged that strategy.
- Technological advances are now reengineering manufacturing enabling reshoring with flexible value chains and a much more reliable, agile, and sustainable business.
Since the 1980s, many Western corporations have been offshoring their manufacturing to low-cost countries, offering cheap prices through exceptionally low wages, cheap real estate for manufacturing facilities combined with huge economies of scale. But with the accelerating progress in transformational technologies like robotics, advanced analytics, artificial intelligence (AI) and machine learning, companies are now breaking free from that dependency.
Combined with rising geopolitical tensions, this process is increasingly driving companies to look at strategies to make supply chains more resilient by moving production closer to home.
Thanks to technological advances like AI and robotics, the era of chasing the lowest wage rates possible has become a thing of the past, eschewed for a more sustainable business approach. Nowadays, what matters more is to secure sustainable, highly flexible production located as close as possible to demand while maintaining a reliable supply chain.
The benefits of automated production
Automated production with connected robots has made it possible to produce more with fewer resources compared to a traditional, “old-fashioned” factory. Some companies are already doing this.
In April 2020, Ericsson opened the doors to its brand new, fully automated 5G factory in Lewisville, Texas — the company’s first production plant on the US market. The 300,000-square-foot plant has since produced 5G and advanced antenna system radios to meet the demand for rapid 5G deployments in North America, which is Ericsson’s biggest market for 5G. Because of the high degree of automation at the site, enabled by 5G private network technology, output per employee has improved 2.2 times. Meanwhile, energy consumption was reduced by 24% and indoor water usage by 75% compared to a traditional factory, and the building is powered by 100% renewable electricity. With this type of return, it makes a lot of sense to invest in local production closer to customers, challenging the conventional thinking of labour cost as the major cost driver. As technology has developed, a more flexible supply chain has become a reality.
Technological advances redrawing global manufacturing
Geopolitical dynamics and the COVID-19 pandemic are without doubt two driving factors behind the new map of global manufacturing. However, technology development within robotics, 5G, data management and AI are the primary driving forces behind the reshoring and near-shoring trend.
The acceleration in the adoption of intelligent, digital technologies is growing across industries, from electric vehicle production to electrical batteries and solar panels. Another fitting example is the steel industry, up until recently characterized as a slow-moving, conservative business. In the wake of Russia’s invasion of Ukraine, European steel companies are now ramping up their capacity to break free from Russian dependence. With this ramp up they are increasingly adopting 5G for their networks to create a more reliant, agile and sustainable business.
Steel players have learned, since the outbreak of COVID-19, the importance of investing in technological agility to adjust for more flexible and resilient operations — i.e., the ability to shut down, restart and ramp up ironmaking and steelmaking capacity in response to ups and downs in demand. One such example is Luxembourg’s Arcelor Mittal, the second-largest steel producer in the world, which is transforming the way it operates through Industry 4.0 and 5G technologies that improve reliability, operator safety, productivity and quality in its factories.
How technological advances enable industrial decarbonization
As industries seek to decarbonize, technological advances will also play a key role in managing changing supply chains. Take, for example, the European steel industry. While the war in Ukraine has accelerated the move away from coal dependence, this is only possible because of advances like electric arc furnaces — a type of furnace that heats material using an electric arc instead of burning coal — and green steel, which uses hydrogen as an energy source.
Europe’s steel industry is aiming to cut carbon emissions by 55% by 2030 compared to 1990 levels and to achieve climate neutrality by 2050. To do so, technological developments enabled-by and combined with supply chain changes are key. Steel production is likely to relocate to countries that can offer green electricity instead of electricity made of coal.
Some players are already doing this. Swedish start-up H2 Green Steel plans to produce Europe’s first commercial green steel by 2025. The electricity used to make the hydrogen that powers the plant comes from local fossil-free energy sources, including hydropower from the nearby Lule river as well as wind parks in the region. Similarly, French start-up GravitHy plans to open a hydro-based plant in France in 2027, while Arcelor Mittal and the Spanish government are investing in green steel projects in northern Spain. German steel giant Thyssenkrupp has announced it aims to introduce carbon-neutral production at all its plants by 2045. All of this is enabled and advanced by technological innovations.
The current geopolitical uncertainties, the increasing demands on supply chain resilience and the urgent need to adapt to a net-zero transition have forced companies to re-evaluate their business models as global industry players.
Adapting to a new reality and embracing disruptive technological innovations is critical for those with the ambition to remain in business a decade from now.
Accept our marketing cookies to access this content.
These cookies are currently disabled in your browser.
Don't miss any update on this topic
Create a free account and access your personalized content collection with our latest publications and analyses.
License and Republishing
World Economic Forum articles may be republished in accordance with the Creative Commons Attribution-NonCommercial-NoDerivatives 4.0 International Public License, and in accordance with our Terms of Use.
The views expressed in this article are those of the author alone and not the World Economic Forum.
Related topics:
Forum Stories newsletter
Bringing you weekly curated insights and analysis on the global issues that matter.
More on BusinessSee all
Andrew Collinge and Katie Adnams
April 11, 2025
Ellen de Ruiter
April 10, 2025
Steve Reis and Jill Zucker
April 10, 2025
Marc Alexander Penzel
April 9, 2025
Naoko Tochibayashi and Mizuho Ota
April 8, 2025
Tariq Bin Hendi
April 8, 2025