This Swedish startup aims to build world's largest green steel plant
The steel industry, a major contributor to pollution, is facing a green revolution spearheaded by innovative startups.
Image: Pexels/Kateryna Babaieva
Adele Peters
Staff Writer, Fast CompanyStay up to date:
Advanced Manufacturing and Supply Chains
- Steel production is a dirty industry, but startups are working on making it more sustainable.
- H2 Green Steel uses hydrogen made from renewable energy to create steel, which significantly reduces emissions.
- The company is building a large-scale plant in Sweden that will begin production by the end of next year.
- Other companies are also developing green steel technologies, including Boston Metal, which uses electrolysis to create steel from iron ore.
Outside the small Swedish city of Boden, surrounded by a forest, a massive green steel plant is under construction. By the end of next year, if all goes as planned, the factory will begin making steel for customers like Ikea and Mercedes-Benz, using hydrogen made from renewable energy instead of coal. By the end of the decade, the plant plans to produce 5 million tons of green steel a year.
That’s still a tiny fraction of global steel production: The world makes nearly 2 billion metric tons of steel each year, for use in everything from high-rises and wind turbines to cars and office chairs. Right now, production is a huge source of emissions. Steelmaking is responsible for more than 2.6 billion metric tons of CO2 emissions annually, nearly three times as much as the aviation industry. But companies such as H2 Green Steel, the Swedish startup, want to prove that the industry can transform.
The startup, which announced this week that it raised more than $5 billion in new financing, is racing to build its solution as quickly as possible. “Others have chosen to start with pilot-scale operations,” says Karin Hallstan, who heads communications for H2 Green Steel. “Our view is that speed is of the essence and the world doesn’t need another pilot. It’s time for action at scale instead. The technology is proven and mature, and we proved the business case and the demand for green steel. That is why we are going straight for large-scale production.”
Most global steel production starts by putting iron ore from mines into huge blast furnaces, where coal is added to create a chemical reaction and make iron. “It’s about as dirty as you would expect,” says Hilary Lewis, steel director at Industrious Labs, a nonprofit focused on helping heavy industry decarbonize.
“Each blast furnace is approximately equivalent to a coal-fired power plant.” Some steel mills have more than one blast furnace. In the furnaces, the chemical reaction makes CO2. The furnace also has to be extremely hot, and that heat usually also comes from burning fossil fuels. The “pig iron” that comes out of the furnace then goes in another type of furnace to process it into steel, creating even more CO2 emissions.
A less common process uses something called a DRI furnace, which operates at a lower temperature and usually runs on natural gas or coal—but can also run on hydrogen. H2 Green Steel will be making green hydrogen at its plant, meaning that it will use renewable electricity to split water into hydrogen and oxygen. (Most hydrogen today is made from fossil fuels).
After it makes iron with its hydrogen-powered DRI furnace, it will process the iron into steel in another furnace that runs completely on electricity. A small amount of carbon is used in this step, but the total process cuts the emissions from steelmaking by 95%.
The method has worked in smaller demonstrations. Nearby in Sweden, a project called HYBRIT delivered the first sample of “fossil-free steel” to Volvo in 2021. The steel company SSAB, one of the partners behind that project, plans to bring a bigger volume of green steel to the market by 2026. ArcelorMittal, a global steel giant, also has green steel projects in development, including a steel mill in Portugal that aims to have a zero-emissions production process in place by 2025. But it will be difficult for the entire industry to transform.
The first challenge: There isn’t much green hydrogen available today. Making the green hydrogen will also require huge amounts of renewable electricity, so more renewables will have to be added to the grid. DRI furnaces also need high-purity iron ore, which isn’t available everywhere. (It’s possible to improve lower-grade ore, but it takes additional steps).
The city of Boden is well-suited for the technology—there’s abundant, affordable renewable energy in the area, and the right iron ore is available. Still, even with the right conditions, the process is expensive. H2 Green Steel charges its customers 25% to 30% more for its steel.
But many customers are willing to pay a green premium for now. Several large automakers have signed contracts committing to buy from H2 Green Steel as soon as production begins. Larger commitments from manufacturers to buy green steel would make a difference for the industry, says Lewis.
The difference in cost for consumers may not be noticeable. “The good news is most people don’t buy steel,” she says. “They buy products that use some amount of steel, like a car.” A car uses around a ton of steel, but using the green version might mean that consumers pay only $100 more for the vehicle.
The EU has an emissions trading system that currently doesn’t require steel manufacturers to pay for all of their emissions, but companies will be required to pay more in 2026, and the amount will keep ramping up until they pay for 100% of their emissions in 2034. “That means that dirty brown steel will become more expensive, finally beginning to level the playing field for cleantech solutions,” says Hallstan.
“The EU regulation could be used as a model for other parts of the world as well, as a way to speed up the shift to sustainably-produced steel.” The U.S. is using a carrot rather than a stick—funding from the Inflation Reduction Act is helping support both green hydrogen and new clean industrial facilities, which could potentially include new green steel plants.
Other promising new technology avoids the use of hydrogen completely. Electra, one early-stage startup, dissolves iron ore and then uses electrolysis to pull out pure iron. The process can use low-grade ores and works at a low temperature, saving energy. Boston Metal, an MIT spinoff, uses electrolysis to heat iron ore to 1,600 degrees Celsius, creating liquid steel.
“There’s no carbon anymore in the process for us,” says Adam Rauwerdink, senior vice president of business development at Boston Metal. “Electrons do all of the work.” At the company’s Boston-area lab, the technology runs indoors. “In the same building as our offices, you’re pouring molten steel, and you’re emitting just oxygen,” he says.
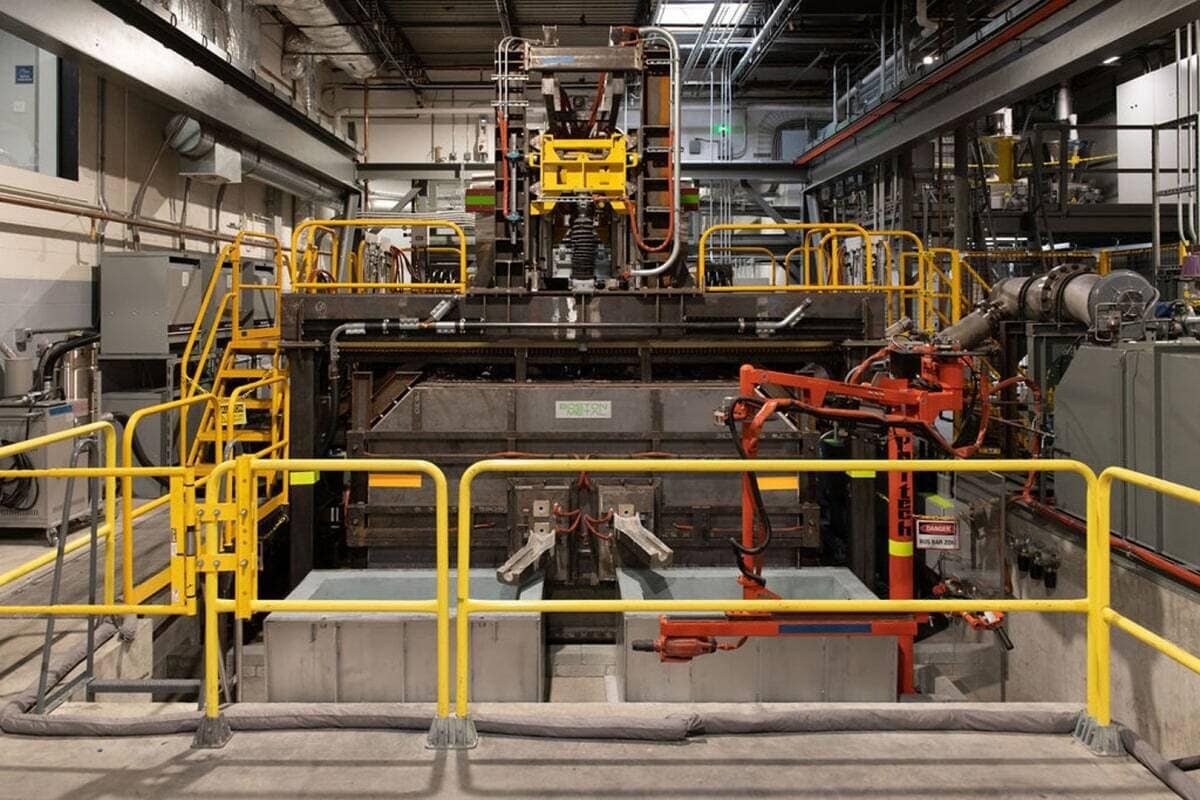
If the process runs on renewable energy, the steel is zero-emissions. The same technique can be used to extract other valuable metals from mining waste. The company is starting first with a project in Brazil that makes niobium, which sells for around 100 times more per kilogram than steel, helping Boston Metal deploy the tech faster while it prepares for the steel market.
The technology is modular—it’s possible to deploy a handful of the company’s units, which can each be as large as a shipping container, or put 200 together to make a full-size steel plant. The first demonstration plant, planned for 2026, will be a smaller unit at an existing steel factory.
Recycling more steel can also help, since scraps can be processed in electric arc furnaces running on renewable energy. But because there’s a limited amount of scrap available, we’ll also need huge amounts of new iron, and both DRI and electrolysis tech can help provide it.
It will take time for the world’s hundreds of steel plants to transform, in part because the equipment that exists now can last for decades. But every 15 to 20 years, traditional blast furnaces have to go through an expensive maintenance step that costs hundreds of thousands of dollars, and companies could switch to DRI technology instead of making the repair. (While carbon capture at traditional steel mills can also help, it doesn’t work perfectly and doesn’t do anything for air pollution or upstream emissions from extracting fossil fuels.) China, which produces the majority of the world’s steel, isn’t moving as quickly to transition to hydrogen as Europe.
Despite the challenges, it’s possible to decarbonize the industry by the middle of the century, says Jeffrey Rissman, who leads work on heavy industry at the consulting firm Energy Innovation and wrote a new book called Zero-Carbon Industry: Transformative Technologies and Policies to Achieve Sustainable Prosperity. There’s enough time to build new plants. The biggest key, Rissman says, will be making sure that enough new renewable energy is available to support the process.
The newest technology, like Boston Metal’s, might ultimately be the best solution, says Lewis from Industrious Labs, because it can avoid the challenge of having to make enough green hydrogen. But because DRI furnaces can run on hydrogen now, it makes sense for companies to move forward with it. “I think we need to be making investments today,” she says. “And I think there will be plenty of opportunity for some of these next generation technologies in the future.”
Don't miss any update on this topic
Create a free account and access your personalized content collection with our latest publications and analyses.
License and Republishing
World Economic Forum articles may be republished in accordance with the Creative Commons Attribution-NonCommercial-NoDerivatives 4.0 International Public License, and in accordance with our Terms of Use.
The views expressed in this article are those of the author alone and not the World Economic Forum.
Related topics:
Forum Stories newsletter
Bringing you weekly curated insights and analysis on the global issues that matter.
More on Manufacturing and Value ChainsSee all
Adegboyega Oyedijo and Temidayo Akenroye
April 18, 2025
Kiva Allgood and Sue Ellspermann
April 9, 2025