3 challenges the aluminium industry should solve to decarbonize faster
The aluminium industry urgently needs to decarbonize with demand expected to grow 40% by 2030.
Image: REUTERS/Fabian Bimmer
Martin Feth
Managing Director and Partner, Global Climate & Sustainability Lead Materials, Boston Consulting Group (BCG)Jelena Aleksić
Industry Decarbonization, Metals Lead (Steel and Aluminium), FMC, World Economic ForumStay up to date:
Mining and Metals
- The aluminium industry is making strides to decarbonize its indirect and direct emissions through electricity decarbonization, clean technology deployment and increased recycling.
- Different routes to decarbonization require varying levels of capital expenditure, which should be better linked to associated decarbonization results and emissions cuts.
- Applying consistent definitions and carbon footprint measurement methodology reflecting decarbonization ambition and progress could bring further investments.
From scientific calculations to extreme weather and changing consumer preferences, there are numerous reasons pointing to the need for the heavy metals industry to decarbonize. The global aluminium industry contributes around 2% of global greenhouse gas emissions and a total of 1.1 billion tonnes of CO²e (carbon dioxide equivalent) emissions per year.
It’s an industry in urgent need of cleaning too: the demand for aluminium is expected to grow 40% by 2030, causing further emission increase. As the world’s second largest metals industry after the steel industry, the aluminium industry is catching the decarbonization drift.
To drive this necessary change, some of the biggest corporate buyers of aluminium, including members of the World Economic Forum’s First Movers Coalition, have made voluntary public commitments to direct at least 10% of their overall primary aluminium volume purchases by 2030 to deeply decarbonized aluminium. This aluminium is produced with 80% less emissions than the global industry average. Alongside such a strong demand signal, these buyers are pledging to pay for a decarbonization-driven green premium, thereby rewarding ambition, progress and investments in the breakthrough technologies necessary to achieve deep decarbonization.
Yet, there is an apparent lack of large, capital investment into breakthrough technologies for deep, sector-wide decarbonization. Why?
Aluminium industry decarbonization pathways and associated costs
Aluminium industrial processes with the largest energy consumption and associated carbon footprint are:
1. Highly energy-intensive electrolysis as the primary method of aluminium smelting;
2. Production of carbon anodes used in the electrolysis process;
3. The Bayer process of refining bauxite to alumina;
4. The extraction of bauxite ore itself.
Producers with historic access to renewables, such as hydropower, are already well-positioned to benefit from green claims and resulting green premiums, and are currently supplying the market with around 30% of total primary production. The price, availability and intermittent current of renewable energy, however, pose significant competitiveness challenges to those producers without legacy access to renewables, thereby slowing the transition to decarbonization.
The path to reducing direct emissions from complex production processes requires breakthrough technologies and substantial investment in terms of time (test pilots), money (large capital expenditure, no price parity) and people (new skills development). The incentive to take this route lies in the ability to further upscale novel technologies – protected by intellectual property rights; and current incremental primary aluminium quantities, representing only a single digit percentage of global primary supplies, to the point of cost parity with fossil-fuel alternatives that can then meet ever-growing demand for decarbonized primary aluminium. Until then, the green premiums are formed on a willing-buyer-willing-seller basis resulting from a substantial mismatch between high demand and low supply of deeply decarbonized aluminium.
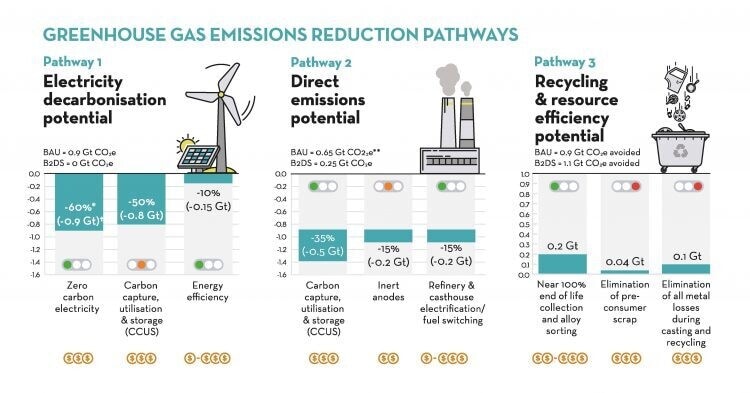
Aluminium recycling, set to grow its share in total aluminium production is also seen as a big decarbonization lever for the industry. The production of recycled aluminium, which uses 95% less energy than the production of primary aluminium makes the secondary aluminium green by the nature of its production.
Converting the 1.5 billion tonnes of aluminium ever produced into scrap to grow recycled aluminium inevitably requires further investments in new technologies and processes for collection, sorting, selection and segregation of scrap. However, these investments are far lower than the investments required for direct emissions reductions and new breakthrough tech, which requires billions. Moreover, this route to decarbonization is constrained by the availability of scrap.
Distinguishing among different types of decarbonized aluminium, their associated decarbonization costs, green claims and related green premiums should create a level playing field that would spur meaningful large investments in sector decarbonization.
Three fundamentals for successful aluminium sector decarbonization
The three immediate challenges the industry faces are linked to the use of low-carbon terminology, carbon footprint methodology and a green premium for deploying decarbonization technology:
1. Introducing a clear definition of decarbonized variants of aluminium
The term low-carbon is currently assigned to primary aluminium made with renewable energy sources and the use of breakthrough technologies, but is equally used for secondary aluminium, where the source and type of scrap and its associated carbon footprint is not always disclosed.
Despite fundamentally different decarbonization pathways and different associated costs, the producers of primary and secondary aluminium use the same or similar terms such as green, near zero, ultra-low, and low-carbon aluminium to annotate different products with different embodied emissions and emissions cuts. As a result, the green premium for low-carbon aluminium is not necessarily awarding direct emissions cuts.
2. Consistent application of carbon footprint methodology
An important part of industry progress towards emission reduction will further depend on consistent application of sector-specific carbon footprint measurement methodology. For different primary aluminium products to be comparable based on their carbon footprint, a reliable application of a single methodology at the product level, using unified emission boundaries, is fundamental.
The most widely used carbon footprint methodology known as "cradle-to-gate", encompassing emissions from the mining process to the smelter cast house (scope 1, 2 and 3 upstream emissions) should be required as the single carbon footprint methodology for aluminium. This would level the playing field and encourage industry consolidation around the comparable product carbon labelling.
3. Green premium as a function of decarbonization progress and ambition
The net-zero transition across industries is believed to require an average annual spending of $9.2 trillion by 2050. Several breakthrough technologies contributing to deep decarbonization of primary aluminium are expected to bring the most substantial cuts of direct sector emissions. Early innovators and adopters should be compensated for their investments in new and related technologies – and the related implementation risks – through decarbonization-driven green premiums.
To achieve substantial decarbonization in the industry, nominal "green aluminium" labels are not going to be enough. Yet, distinguishing between the different types of green aluminium and the different decarbonization-driven green premiums they require, favouring emissions cuts and embodying green ambitions and progress over the mere product emissions results, just might.
Don't miss any update on this topic
Create a free account and access your personalized content collection with our latest publications and analyses.
License and Republishing
World Economic Forum articles may be republished in accordance with the Creative Commons Attribution-NonCommercial-NoDerivatives 4.0 International Public License, and in accordance with our Terms of Use.
The views expressed in this article are those of the author alone and not the World Economic Forum.
Forum Stories newsletter
Bringing you weekly curated insights and analysis on the global issues that matter.
More on Climate ActionSee all
Gabriel Onuh
May 21, 2025
Jack Hurd and Florian Vernaz
May 21, 2025
Christie Burley and Lindsey Prowse
May 20, 2025
Dipali Khandelwal and Hemlata Chauhan
May 19, 2025
Shyam Bishen and Lorna Friedman
May 19, 2025