The green plastic made from biodiesel waste
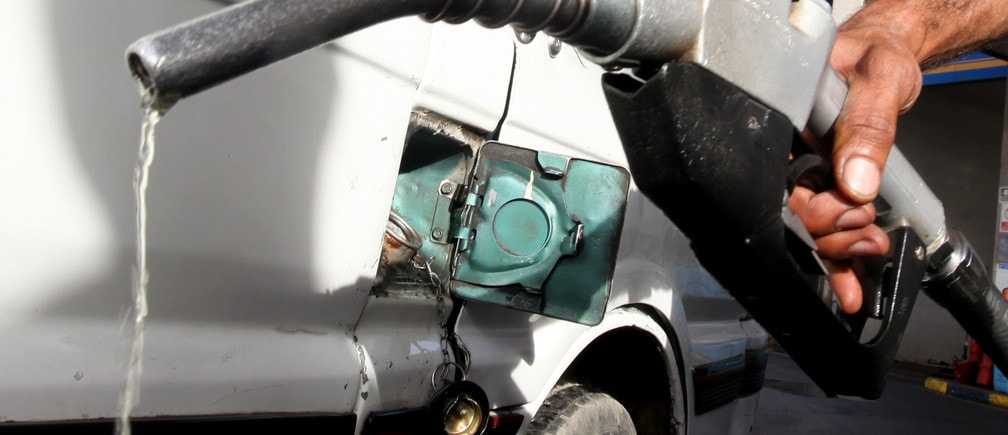
Stay up to date:
Innovation
Plastic waste is one of today’s major environmental concerns. Most types of plastic do not biodegrade but break up into ever smaller pieces while remaining a polymer. Also, most types are made from oil, a rapidly dwindling resource. But there are promising alternatives, and one of them is polylactic acid (PLA): it is biodegradable and made from renewable resources. Manufacturers use PLA for disposable cups, bags and other sorts of packaging. The demand for PLA is constantly rising and has been estimated to reach about one megaton per year by 2020.
The research groups of ETH professors Konrad Hungerbühler and Javier Pérez-Ramírez at the Institute for Chemical and Bioengineering are now introducing a new method to produce lactic acid. The process is more productive, cost-effective and climate-friendly than sugar fermentation, which is the technology currently used to produce lactic acid. The new method’s greatest advantage is that it makes use of a waste feedstock: glycerol.
Waste product of biofuel manufacturing
Glycerol is a by-product in the manufacturing of first-generation biofuels and as such is not high-grade but contains residues of ash and methanol. “Nobody knows what to do with this amount of waste glycerol”, says Merten Morales, a PhD student in the Safety and Environmental Technology group of professor Hungerbühler. This waste substance is becoming more and more abundant, with 3 megatons in 2014 expected to increase to over 4 megatons by 2020. Because of its impurity, glycerol is not suitable for the chemical or pharmaceutical industry. Moreover, it does not burn well and is thus not a good energy source. “Normally, it should go through waste water treatment, but to save money and because it is not very toxic, some companies dispose of it in rivers or feed it to livestock. But there are concerns about how this affects the animals.”
Making use of this waste feedstock by converting it into lactic acid already constitutes an advantage that makes the new method more eco-friendly. In this procedure, glycerol is first converted enzymatically to an intermediate called dihydroxyacetone, which is further processed to produce lactic acid by means of a heterogeneous catalyst.
High-performance catalyst
The researchers of the Advanced Catalysis Engineering group of professor Pérez-Ramírez designed a catalyst with high reactivity and a long life span. It consists of a microporous mineral, a zeolite, whose structure facilitates chemical reactions within the pores. The close collaboration between the two research groups allowed the catalyst to be improved step by step while at the same time performing the life cycle assessment of the procedure as a whole. “Without the assessment and comparison with the conventional method, we might have been happy with an initial catalyst design used for our study, which turned out to be less eco-friendly than fermentation”, explains Pierre Dapsens, a PhD student in the Pérez-Ramírez group. By improving several aspects of the catalyst design, the researchers were finally able to surpass sugar fermentation both from an environmental and an economic point of view.
Industrial processes are often turned “sustainable” simply by switching to a renewable resource. “However, taking the whole process into account – from the source of the feedstock to the final product and including waste management – you will often find that a supposedly sustainable production method is not necessarily more sustainable than the conventional one”, adds Cecilia Mondelli, a senior scientist in the Advanced Catalysis Engineering group who is also involved in the study.
20 per cent less CO2
Taking into account the energy saved by using the waste feedstock glycerol and the improved productivity, the new procedure reduces the overall CO2 emission by 20 per cent compared to fermentation: per kilogram of lactic acid produced, 6 kilograms of CO2 are emitted with the new method compared to 7.5 kilograms with the conventional technology. Also, by lowering the overall cost of the process, the researchers calculated a 17-foldincrease of the profit possible by using the new process. “Our calculations are even rather conservative”, says Morales. “We assumed a glycerol feedstock of relatively good quality. But it also works with low-quality glycerol, which is even cheaper.” Thus, manufacturers could increase their profit even further.
“Although today’s major bioplastic companies are based in the US, the process is relatively simple and could be implemented in other countries that produce biofuel and the by-product glycerol”, concludes Dapsens.
Literature reference
Morales M, Dapsens PY, Giovinazzo I, Witte J, Mondelli C, Papadokonstantakis S, Hungerbühler K, Pérez-Ramírez J: Environmental and economic assessment of lactic acid production from glycerol using cascade bio- and chemocatalysis. Energy & Environmental Science, 5 November 2014, doi:10.1039/C4EE03352C
Published in collaboration with ETH Zurich
Author: Angelika Jacobs is a Science Editor at ETH News
Image: A worker fills the tank of a car at a petrol station in Cairo, March 12, 2013. REUTERS/Mohamed Abd El Ghany.
Don't miss any update on this topic
Create a free account and access your personalized content collection with our latest publications and analyses.
License and Republishing
World Economic Forum articles may be republished in accordance with the Creative Commons Attribution-NonCommercial-NoDerivatives 4.0 International Public License, and in accordance with our Terms of Use.
The views expressed in this article are those of the author alone and not the World Economic Forum.
Related topics:
Forum Stories newsletter
Bringing you weekly curated insights and analysis on the global issues that matter.
More on Climate ActionSee all
Lee Poh Seng and Heng Wang
May 12, 2025
Jean-Claude Burgelman and Lily Linke
May 9, 2025
Tejashree Joshi
May 8, 2025