Could 3D printing revive Africa’s industrial sector?
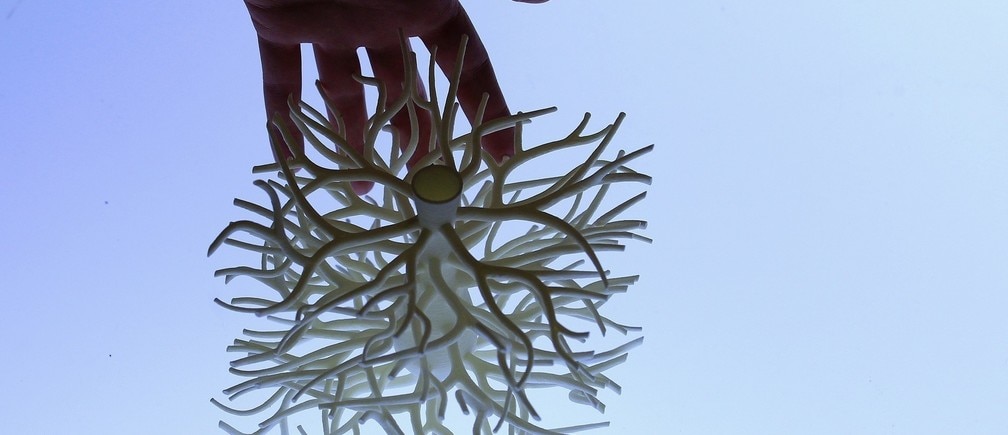
Stay up to date:
Digital Communications
Toby Lankford, who describes himself “a developer/ tinkerer that loves aerial and personal robotics, living off grid, and growing good food naturally with robots” has a project that should be of interest to Africa’s endangered rhinos and elephants.
He is working on a 3D printed drone that he hopes can be used as a bush plane to assist in stopping the poaching of Africa’s wildlife.
With drones, it’s like we’re living in the Wild West of 3D printing, if this and other news over the past week is anything to go by. In Britain, a 3D printed drone was launched from a British military warship over the weekend and successfully flew to shore, a demonstration that could pave the way for futuristic spy drones that could be printed at sea.
The drone, largely made of nylon, is cheap and quick to make; the print run takes 48 hours in total, including time for cooling. It potentially heralds a new way of waging war – armies in the battlefield could print their own custom-made weapons, vehicles and replacement parts as needed, reducing the need for imports or relying on factories back at home.
In the US, the Food and Drug Administration just approved the first 3D printed drug, a medication for epilepsy that allows it to dissolve more quickly, which means that a high drug load – up to 1,000mg – can be delivered in a single dose. More importantly, it opens the door for medication to be more effective by being tailored for individual patients.
It’s already happening with prosthetic limbs. In Uganda, 3D printing is being used to create custom-made prosthetic limbs for amputees. In the past, the all-important plaster cast sockets that connect artificial limbs to a person’s hip took about a week to make, and were often so uncomfortable people ended up not wearing them.
Plastic printed ones can be made in a day and are a closer, more comfortable fit. It also makes huge savings, with the cost expected to come down from $5,000 to $250 per prosthetic fit – 95% cheaper.
There’s all kinds of nifty, astonishing, and crazy 3D printed products under design right now; the recent explosion in the technology is thanks to an clutch of 3D printing patents that expired in early 2014 and made it available for the broad market.
NASA is working on a 3D printed “tree”, which, instead of a whole tree, is a cellular array that mimics plant cells and secretes organic materials such as wood, rubber or cellulose.
The team believes they can pull of a proof-of-concept deadline by October, and are hoping to create unique materials like carbon-reinforced wood, or wood infused with copper nano-wires, which means that perhaps one day there will be no need for unsightly electricity posts and wires everywhere to transmit power; trees themselves could just act as transmission lines.
Early this year, Hans Fouche of South Africa printed a lawn mower in just nine hours, and followed it up with a vacuum cleaner that doubles up as a flowerpot. Fouche’s inventions came just months after Togolese inventor Afate Gnikou actually assembled a 3D printer from electronic waste collected from dumpsites around the capital Lomé.
3D printing works by translating digital information into physical objects; computer software directs molten metal, plastic or other material to build an object layer by layer.
The technology turns traditional manufacturing upside down; instead of massive factories running on expensive equipment, it makes possible light, decentralised, “guerilla” manufacturing.
Like mobile phones, and possibly, renewable energy, 3D printing could be the killer app that enables Africa to leapfrog into a new age of industrial production, revive an industrial sector that has stagnated in many African countries over the past few decades, and provide many much-needed jobs.
In 2010 sub-Saharan Africa’s average share of manufacturing value added in GDP was 10%, unchanged from the 1970s, while the region’s share of world manufactured exports has fallen from 0.3% in 1980 to 0.2% in 2010.
Advanced manufacturing is part of a bigger trend that is re-shaping the industrial sector into a very different structure from the dank sweatshops that have typically characterised manufacturing.
The coming together of digital technologies and industrial activity is happening along different lines, including automation and robotics, data-driven supply chains and work flows, crowdsourcing in industrial innovation, and digitally driven manufacturing techniques, of which 3D printing is a part of.
Marco Annunziata, chief economist of General Electric, recently described three aspects of the “new industrial age” – first, there is the Industrial Internet, which merges “big data with big iron”, integrating cloud-based analytics with industrial machinery, resulting in greater efficiency and reduced downtime.
For example, a digitally-integrated wind farm could allow turbines to communicate with each other, and respond in a coordinated way to changes in environmental conditions: as the force and direction of the wind changes, the turbines can modify the pitch of their blades in a coordinated manner to maximise power output for the entire wind farm, as opposed to every wind turbine optimising its own output in isolation.
Second, there’s Advanced Manufacturing, which links design, product engineering, manufacturing, supply chain, distribution, and servicing into one cohesive and intelligent system.
And finally, there’s the “Global Brain”, as Annunziata calls it – the collective intelligence of human beings across the globe, integrated by digital communication networks. Essentially, instead of spending painstaking hours developing a product yourself, you could simply ask other people to design it for you.
It short-circuits the need for highly skilled internal capacity, which could be exactly what the continent needs – Africa is suffering from a skills shortage, particularly the technical jobs such as prototyping and industrial design.
Less than 10% of Africans of university-age are enrolled in higher education; Unesco estimates that in countries like Namibia, Zimbabwe and Tanzania, there is one qualified engineer for a population of 6,000 people, compared to one engineer per 200 people in China.
Tapping into the global pool of knowledge could help African countries to make up for skills shortages and just focus on the manufacturing process itself.
But like green energy, the pitfall could be in the politics. There’s always been power in government shaping of industrial policy in a country, and in the African context, it has often encouraged rent-seeking and political favouritism, as opposed to sound business decisions.
Most African countries followed a similar industrial policy from independence – there was the import substitution phase in the 60s and 70s, where governments sought to reduce dependence on international imports by deliberately supporting domestic industries to produce goods for local consumption.
In countries like Guinea and Tanzania, it meant nationalising industries and bringing them under direct government control; and in freer countries like Kenya, it meant protecting local industries from foreign competition through import tariffs, exchange controls, price controls and other protectionist measures.
But in the end, these controls created a business environment that reduced the need to innovate and made the industries uncompetitive. Most countries dismantled these protections in the 1980s and 90s, liberalised their economies and abandoned the import substitution model. In Tanzania, for example, by the year 1990, 22 out of the country’s 24 textile factories had closed.
Many countries are now courting foreign direct investment, offering incentives like tax holidays and export processing zones – with varying success. Ethiopia’s state-led industrial model is one of the relatively successful ones, industry value added share to GDP has been about 14% in the past decade.
Still, there’s now a chance for young African entrepreneurs to side-step that whole political minefield, and with a modest capital investment, create quality, innovative products that can compete on the global stage.
This article is published in collaboration with Mail & Guardian Africa. Publication does not imply endorsement of views by the World Economic Forum.
To keep up with Agenda subscribe to our weekly newsletter.
Author: Christine Mungai is a journalist with Mail & Guardian Africa.
Don't miss any update on this topic
Create a free account and access your personalized content collection with our latest publications and analyses.
License and Republishing
World Economic Forum articles may be republished in accordance with the Creative Commons Attribution-NonCommercial-NoDerivatives 4.0 International Public License, and in accordance with our Terms of Use.
The views expressed in this article are those of the author alone and not the World Economic Forum.
Related topics:
Forum Stories newsletter
Bringing you weekly curated insights and analysis on the global issues that matter.
More on Geographies in DepthSee all
Yusuf Maitama Tuggar
July 10, 2025
Kaiser Kuo
June 24, 2025
Kaiser Kuo
June 19, 2025
Aimée Dushime
April 18, 2025
Samir Saran and Anirban Sarma
April 17, 2025
Nada AlSaeed
April 16, 2025