Could “green” beer benefit the environment?
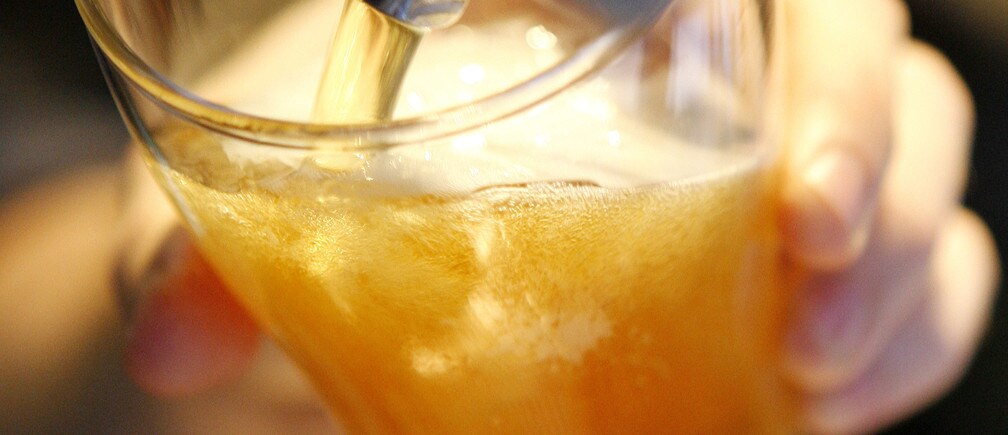
Green beer may not sound too appealing, but in Mwanza, it’s going down a treat. A locally produced “greener” brew not only slakes thirst but is reducing the carbon footprint of the country’s second largest city.
Tanzania Breweries Limited is tapping biomass energy to produce more sustainable beer while cutting its fuel costs.
“We have adopted new technology which has enabled us to use rice husks as fuel for our boilers instead of heavy furnace oil,” said Sunday Kidolezi, manager for the firm’s Mwanza utility in the north of the East African country.
The husks are considered a waste product by local farmers. Growers tend to leave them piled in huge mounds, burn them outdoors or dump them in the forest, making them a source of climate-changing carbon emissions.
According to Kidolezi, more than 60 percent of the Mwanza factory’s electricity now comes from the husks, which it buys from farmers. Furnace oil accounts for just 10 percent of the energy the company uses, with the balance coming from the national grid.
As a result, the brewery has halved carbon emissions at its Mwanza plant, to 4,451 tonnes in 2014 from 8,909 tonnes in 2012, while saving $400,000 a year on oil purchases, Kidolezi said.
The company now plans to use rice husks as fuel in its other breweries in Dar es Salaam, Mbeya and Arusha, he added.
Agricultural biomass remains a largely untapped source of electricity in Tanzania that could significantly cut costs and help solve the problem of an erratic power supply that has crippled the country’s manufacturing sector, experts say.
Tanzania has many renewable energy sources, including wind, solar, biomass, small-scale hydropower, geothermal and tidal energy. The government is trying to promote a range of clean technologies to diversify its sources of energy.
“Agricultural waste is one of the cleanest renewable energy sources that can substantially displace fossil-fuel use. However, it’s yet to be fully utilised,” said Julius Ningu, director of environment in the Vice President’s Office.
The beer industry is a major economic force in Tanzania, responsible for 413 billion Tanzanian shillings ($191 million) in government revenue in 2014-15 alone, and providing thousands of jobs.
But the effects of climate change have made the industry’s future less certain as warmer temperatures, droughts and extreme weather affect the production of maize, a critical ingredient in Tanzania’s beer brewing.
While the government is supporting the development of drought-resistant maize varieties, many companies also are trying to cushion their businesses financially by investing in renewable energy and sustainable water use.
Through recycling and other conservation measures, Tanzania Breweries has managed over five years to reduce its water use in Mwanza by 40 percent to 1,200 cubic metres a day, said Kidolezi.
The brewery is one of 35 companies in the country’s Lake regions that are promoting an environmental management initiative dubbed “resource-efficient and cleaner production”, which aims to reduce energy costs and protect the ecosystem of Lake Victoria, which borders Mwanza to the north.
SUGAR CANE AND SISAL
In the face of spiralling production costs that are hurting the manufacturing sector, industries other than brewing are also adopting renewable energy sources to produce electricity.
According to the Confederation of Tanzania Industries, energy costs account for 20 percent of industrial production, but efficiency initiatives can save manufacturers up to 40 percent of their energy bill.
Major sugar producers in Tanzania already use sugar cane residues (bagasse) to provide heat and electricity for their own factories, and sometimes sell surplus power to the national electricity supply company, TANESCO.
The sugar factories in Mtibwa, Kilombero and Kagera use more than 455,000 tonnes of bagasse each year to generate more than 64 percent of their energy needs.
The bagasse is burned to generate steam in high-pressure boilers, and the steam is converted to electricity, most of which is used for sugar processing.
Katani Limited, a sisal fibre company based in Tanga, has developed a technology to convert sisal plant residues into biogas to generate electricity for its own use, as well as compressed gas for domestic use. Scientists say cooking gas from sisal waste is more efficient and cheaper than charcoal.
Prior to this, the company was throwing away around 90 percent of sisal waste during its production processes.
This article is published in collaboration with Thomson Reuters Foundation trust.org. Publication does not imply endorsement of views by the World Economic Forum.
To keep up with the Agenda subscribe to our weekly newsletter.
Author: Kizito Makoye is a freelance correspondent for the Thomson Reuters Foundation.
Image: A bartender prepares a beer in a bar. REUTERS/Daniel Munoz/Files.
Don't miss any update on this topic
Create a free account and access your personalized content collection with our latest publications and analyses.
License and Republishing
World Economic Forum articles may be republished in accordance with the Creative Commons Attribution-NonCommercial-NoDerivatives 4.0 International Public License, and in accordance with our Terms of Use.
The views expressed in this article are those of the author alone and not the World Economic Forum.
Forum Stories newsletter
Bringing you weekly curated insights and analysis on the global issues that matter.