The Fourth Industrial Revolution and the factories of the future
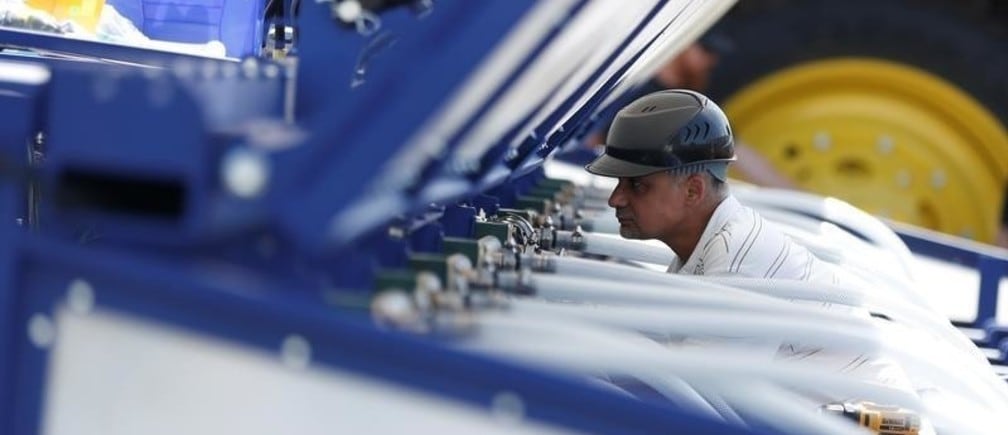
Image: REUTERS/ Stephen Lam
Stay up to date:
Innovation
After a decade of flat productivity, the arrival of the Fourth Industrial Revolution (4IR) is expected to create up to $3.7 trillion in value to global manufacturing. A few years back, experts noted that the changes associated with the 4IR would come at an unprecedented rate yielding incredible results for those who truly embraced them.
Still, the hockey stick of benefits has not kicked in yet – while all companies are making efforts to adopt technology, most of the production industry (~70%) remains in pilot purgatory (where technology pilots last for extended periods of time, and companies do not take the final step of scaling up viable technologies). Less than 30% of manufacturing companies are actively rolling out Fourth Industrial Revolution technologies at scale.
The World Economic Forum, in collaboration with McKinsey, has undertaken a global search and assessment for “4IR production lighthouses” – sites representing the most advanced sub-section of the companies who are actively deploying 4IR technologies at scale. Leveraging these lighthouse sites, we will create an inclusive learning platform with aims on becoming the next “go-to” system for advanced manufacturing and bring the world closer to capturing the lion’s share of the benefits.
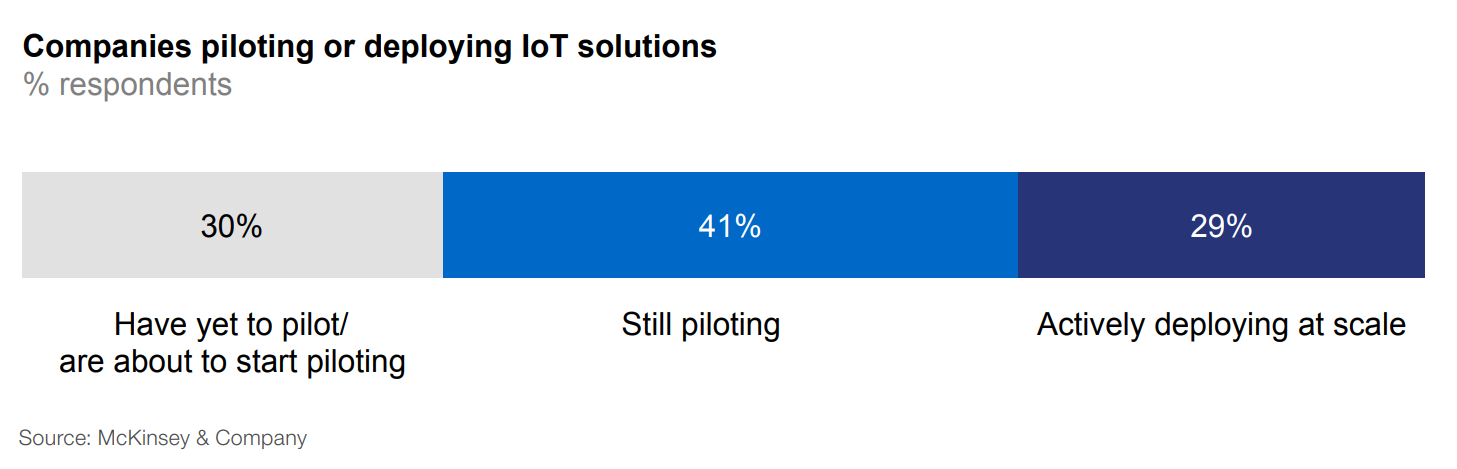
Most manufacturing lines still look a lot the same way they did 10, 20 or even 30 years ago. Operators clock in, have a brief conversation with their crew and shift supervisor, and then operate a machine or tool for 8-12 hours before heading home. Depending on the day, the machine may break and need maintenance or an adjustment, the line settings may need to be modified for a specific product or run, or the operator may need to step away to resupply the line or be trained on a new procedure.
In 4IR transformed manufacturing sites – production lighthouses – this is no longer the case.
Manufacturing has changed for the sites that are leading the 4IR technology adoption and are willing to undertake the necessary organizational, operational and financial transformation. For those sites, things look and feel a little bit differently. They:
• Leverage cameras and wearables to facilitate entering buildings, checking out at the company store and even receiving urgent messages
• Hold conversations around line and shift performance informed by digital smart whiteboards displaying real-time metrics and supported by machine learning for root cause problem-solving of issues
• Monitor the status of machinery both in real-time as well as digitally, predicting likely failure points and flagging to the relevant parties
• Allow production machines to learn from their own mistakes and adjust their settings to improve their long-term quality output every few seconds
• Use mixed reality tools to diagnose breakdowns – literally “x-raying” machines to identify the source of issue, adjust settings in a standardized way and receive training
Importantly, the majority of these tools highlighted above have been implemented at scale in select factories, and we are on a mission to find them, learn from them and improve the adoption and diffusion of 4IR technologies. The long-term goal is to replicate, with a global platform of 4IR lighthouse sites, the phenomenon experienced with the Toyota Production System a few decades ago. Companies from all industries and from all over the world would travel to Japan to learn about the Toyota Production System (TPS), to then return home and deploy these best practices.
We are building something similar. Imagine a new global learning platform which aims to share, across the manufacturing community, the best practices for technology adoption and diffusion of 4IR technologies.
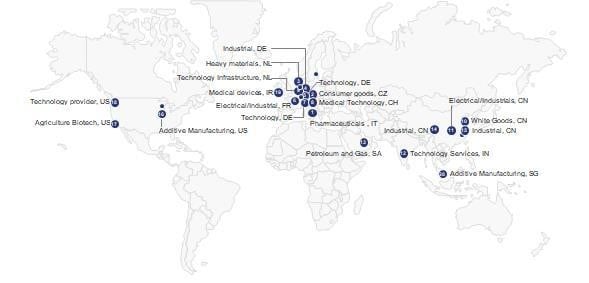
So far ~30 sites have responded to the worldwide call to action:
The study of leading production/manufacturing has revealed two critical truths: 1) the financial and operational impact achieved by the at-scale, concurrent deployment of multiple technologies is substantial; and 2) the success factors in deploying these technologies vary from case to case but are typically driven by both technical and organizational factors. Each of the three highlighted examples dealt with known pain-points across the manufacturing industry in a radical and innovative way.
Below, we highlight three examples that stood out from our search for the most advanced manufacturing lighthouses. Although in each case we highlight one particular scenario, in each of the leading 4IR production sites we identified and visited, 4IR has truly been imbued into the ethos of the site. Sites have defined a vision of themselves for the future, established a road map to get there and have multiple (>5) 4IR use cases already deployed.
A French-headquartered global specialist in energy management and automation is in the early stages of a large-scale digital transformation across its ~200 sites worldwide. In support of this effort, it began its journey in 2017 with a select number of sites, each with dedicated project teams, meant to test, pilot and deploy at scale while building the road-map for the rest of the organization. Roughly one year into the journey, one site in France is reaping the benefits of 14 mature 4IR use-cases, like augmented reality for operators and maintenance, data analytics to improve performance and prevent breakdown, and the use of autonomous vehicles to automatically resupply production line whenever components are running out.
They credit their success to their ability to deal with the “fear of the unknown.” The site in France achieved this by first building a digital model of their future-state factory. A brick-by-brick digital copy of their current factory – co-created with the operators – on which the 4IR technologies were overlaid. Over a multi-session process, operators wore the Virtual Reality glasses and hand remotes and saw, reflected and discussed the transformation of the factory and their roles. It suddenly became easy and acceptable to voice questions and concerns – the unknowable had become known.
By the time the physical implementation of the technologies arrived at the shop floor, the biggest hurdle, mindset, was behind them.
A Swiss-headquartered digital solutions company has been focused on maintaining competitiveness through the intelligent application of forward-looking technologies. In a process that dates back several years, one of its plants in Germany is yielding improved operational and financial results from the implementation of 18 mature 4IR use-cases. It has achieved this by: 1) leveraging the internal technology ecosystem within the company, 2) using a dedicated project team and bench of experts and 3) implementing only financially viable technologies that adhere to strict pilot protocols. The factory, a largely automated site already using robots developed in house, faced substantial cost and capacity constraints in the face of a changing market. Where before it used to produce batches in the millions of units and with low level of variation, market demand increasingly asked for the opposite – smaller batches and higher variation. The product, a mini-circuit breaker, is the type of product that consumers use and live by, but rarely give a thought to unless it fails. Found in homes, it prevents short circuits, overcurrents and overloads without ever bothering the end user. Quality is paramount.
The site’s dedicated 4IR team set out to identify and implement a cost-effective technology that would support a production line that required perfection. They found their solution in the deployment of standard-issue cameras throughout the production line that scan the component for quality throughout the production line. Given the nature of production (a new component is finished every six seconds), speed is essential. After every scan, data is fed back into machine-learning algorithms designed by the company’s broader corporate capabilities and informed by the testing know-how of the site to adjust production lines settings while in batch. This means, that quality improves in every consecutive item made. In practical terms, it means that the site’s quality improved 4% by the end of the day, every day. All without a missing a beat and allowing operators to shift to higher value-added work.
The Fourth Industrial Revolution has both the potential to improve the value proposition of traditional industry, as well as create entirely new business models and opportunities. At one large US-based logistics company that has implemented six mature 4IR use-cases (and 15 developing), this is particularly true. Through an investment in a startup leveraging several coordinated 4IR technologies in a green-field setting, it aims to provide on-demand manufacturing capabilities, near the end consumer, and starting from batch size one. This new business model responds to mega-trends such as mass customization, and demand for shorter lead times.
This new business model is being implemented in a Chicago site that started by hosting a digital copy of high value spare parts. The type of parts that large industrial companies typically held in inventory typing up space, money and resources with little benefit – just in case. What the manufacturing site can now do is print the part on demand and close to the end consumer, such that long lead times, tied up capital and discontinuation of parts/OEMs are a thing of the past. The long-term goal is reducing the $1.8 trillion of inventory held in the US alone.
We are a long way away from fully capturing the benefits of the 4IR in an inclusive and holistic way. To do this, technology adoption and diffusion across the ecosystem needs to improve dramatically. The key lesson learned is that each of the identified lighthouses have achieved that status through the implementation of several concurrent technologies
Organizations from across the public and private sector have highlighted the need for a neutral learning platform to navigate the complex journey of the Fourth Industrial Revolution in manufacturing. Our goal is to create such a neutral platform, which provides the best technical and organizational insights with respect to 4IR technologies in manufacturing to accelerate the delivery of the benefits. Such a platform will also facilitate collaborative action and new partnership between companies and governments.
Currently, lighthouse candidates are being studied to develop a library of best practices to be leveraged by the Forum’s members. Official recognition of the lighthouses is expected at the Forum’s Annual Meeting of New Champions to be held 18-20 September in Tianjin, China.
Our search will continue up and through Davos 2019 as we continue to seek the answer to the questions:
• What are the world’s most advanced manufacturing sites?
• What other examples of 4IR technologies widely in use today?
• What are the structures, and processes successfully supporting the adoption and diffusion of 4IR technology?
Don't miss any update on this topic
Create a free account and access your personalized content collection with our latest publications and analyses.
License and Republishing
World Economic Forum articles may be republished in accordance with the Creative Commons Attribution-NonCommercial-NoDerivatives 4.0 International Public License, and in accordance with our Terms of Use.
The views expressed in this article are those of the author alone and not the World Economic Forum.
Related topics:
Forum Stories newsletter
Bringing you weekly curated insights and analysis on the global issues that matter.
More on Fourth Industrial RevolutionSee all
Clas Neumann
June 16, 2025
Gareth Francis
June 12, 2025