Data from Denmark reveals crucial insights about the spread of automation – read more
The automation of production processes is an important topic on the policy agenda in high-wage countries, but evidence of the economic effects of automation at the firm level is limited.
Image: REUTERS/Luisa Gonzalez
Lene Kromann
Assistant Professor, Department of Management & Organizational Studies, University of Western OntarioStay up to date:
Future of Manufacturing
Increasing competition from low-wage countries has led many manufacturing firms to close or offshore parts of the production process. It has been argued that this may jeopardise continued welfare improvements. Helper et al. (2012) argue that the (US) manufacturing sector is the major source of commercial innovation and is responsible for the lion’s share of export earnings. The downsizing of the manufacturing sector is a cause for concern among policymakers in high-wage countries. They have been searching for clever ways to bring back manufacturing production and jobs. New technologies and automation are often considered possible solutions to the challenges. It is expected that many technological innovations that can potentially contribute to productivity will be developed in the future (Council of Economic Advisers 2016). It is also expected to benefit activities outside manufacturing through the ‘servitisation’ of products and closer connections to design and innovation, which allows for positive effects for the total economy (Bruegel 2017).
Existing work on automation
Recent studies on automation have mainly focused on the relation between automation and employment. However, a few empirical papers study the relationship between industrial robots and performance include Graetz and Michaels (2018) and Kromann et al. (2019), and both papers find that the industry-level adoption of industrial robots has raised productivity.
There is almost no systematic empirical evidence for the potential economic effects of automation at the firm level for recent years. There is a small stream of existing literature on automation – Dunne (1994), Doms et al. (1997), and Bartelsman et al. (1998) – that focuses on an earlier wave of automation during the 1980s and early 1990s. These papers mainly describe differences between plants or firms that adopt automation technologies and those that do not. Bartel et al. (2007) study a more recent period, namely, 1997-2002, but focus on one narrowly defined industry – US valve manufacturing – and find that investments in automation improve the efficiency of production.
New measures of automation
A deeper understanding requires firm data. For a new paper (Kromann and Sørensen 2019), we have gathered a new dataset that measures automation in Danish manufacturing firms. Thereby, we can present empirical evidence for the adoption of automation technology across manufacturing firms. Based on observations from firm visits, two important measures that describe automation stand out. These are the stock of automated capital and the share of production processes that is automated. We label the latter measure the automation score and the purpose of this measure is to capture that automated capital can be used more or less efficiently by the firms, depending on how well it is implemented and integrated into the manufacturing system. The survey was developed so that these two aspects could be measured. The motivation for including the automation score in the survey was that managers, suppliers of automation equipment, and industry experts claimed that the share of production processes that is automated is an important aspect of automation that is not necessarily captured by standard measures of capital. This claim is strongly supported in the empirical analyses.
Findings
We start by examining the adoption of automation across manufacturing firms. We find that the use of automation is modest in many firms. In 2005, almost 40% of the firms’ investments in machinery and equipment targeted for automation were at approximately 10% or lower. In 2010, almost half of the firms still relied to a high extent on manual production processes. At the other end of the spectrum, there are firms that devote all their investments in machinery and equipment to automated capital and have high automation scores. The results are seen in Figure 1. This leads us to conclude that there is high variation in the adoption of automation technologies across firms – a conclusion that also holds within sub-industries, different types of production, and firms with high and low export intensity.
Figure 1 New capital investments and automation in firms
a) Distribution of the percentage of new capital investments in machinery and equipment targeted at automation
b) Distribution of the automation score for 2005 and 2010
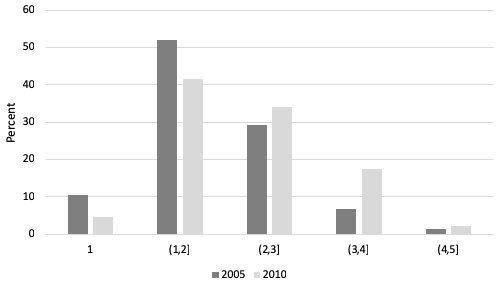
Note: Based on 474 firms used in Section 4
Source: Authors’ survey on automation in manufacturing
Given the variation in automation across firms, an immediate question is what drives investments in automation. Therefore, we turn to examining a potential driver of the adoption of automation technologies. Specifically, we focus on increasing international competition from China since its admission to the WTO, and investigate whether this has accelerated the adoption of automation technologies. We refer to this as the trade-induced automation hypothesis. We find that increasing Chinese exports to the world drive investments in automated capital, which supports the hypothesis. The firms that specialise in product types in which Chinese exporters have a comparative advantage have an incentive to invest more in automation to withstand the increasing competition compared to firms that specialise in other products. The growth rate in automated capital is 2.16% higher per year for the 75th percentile firm compared to the 25th ranked after Chinese export changes for the firms’ main product. We also investigate whether increasing Chinese exports to the world is related to the automation score. This turns out not to be the case, suggesting that Chinese export changes for the firms’ main product only drive investments in automated capital but not how these investments are implemented in production. The results are presented in Figure 2.
Figure 2 Automation and international competition: Five-year difference estimation, 2005-2010
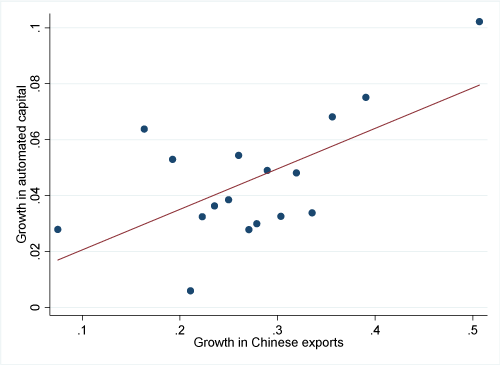
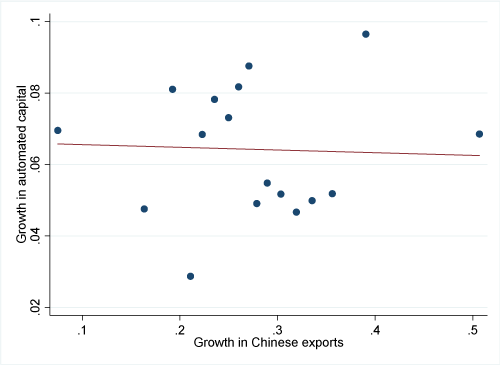
Note: Figures are representations of Table II, columns 1 and 4 of Kromann and Sørensen (2019). Figures are constructed using the Stata programme “binscatter”. Each bin is represented by a dot and represents the mean of 26 firms. The number of bins are chosen to fulfill Statistics Denmark’s regulations on anonymity that among others requires that the two largest firms in a bin do not have a total sales share that exceed 85%. The fitted lines are estimated by OLS on the estimation data set consisting of 442 firms. Regressions are performed on long-differences that sweep out firm fixed effects. The dependent variables are: Δlog of automated capital in the top panel and Δ automation score in the bottom panel. The explanatory variables presented in the figure is Δlog of Chinese export within the product type with the largest sales share of the firm. In both figures, we control for a set of explanatory variables including Δlog of other types of capital, Δlog of employment, and Δ skill share and a full set of industry by region dummies (10 industries and 8 regions). All changes are in five-year differences between 2005 and 2010, except for Δlog of Chinese exports where the five-year differences are measured between 2001 and 2006. The measures of international competition are measured at the product level. There are 189 different product codes for the 442 firms.
Source: Authors’ survey on automation in manufacturing, UN Comtrade data, and register data from Statistics Denmark
Model description and external validation
The empirical model is related to the theoretical model suggested by Bloom et al. (2014) that proposes a positive relationship between innovation and import competition. Specifically, the theoretical model explains why firms that are more exposed to competition from China have larger incentive to innovate after trade is liberalised. The mechanism is driven by “temporarily trapped factors”, e.g. skilled workers that are expensive to train for the firm and, therefore, to fire because their firm-specific human capital is lost for the firm. The increasing competition from China lowers the demand for products that skilled workers produce. Due to the high training costs, the skilled workers keep their jobs in the firm, but their opportunity cost is reduced. Accordingly, the incentive for innovation in the firm increases after trade liberalisation because the opportunity cost of skilled workers has gone down. Bloom et al. (2016) establish empirical support for the model and investigate the effect of Chinese import competition on innovation across twelve European countries.
Finally, we investigate whether the automation measures are significantly associated with measures of firm performance. The analysis is a way to determine whether our survey contains important information on automation and not just white noise. We find that increasing use of automation is significantly associated with higher productivity growth and increases in profitability. The relationships are robust to a wide range of control variables including skill shares, other production factors, and industry dummies interacted with region dummies. These results offer some external validation of the automation survey.
Concluding remarks
As discussed above, the variation in automation across firms is high. A first-order policy question arises from this result, which is as follows. Is the absence of adoption of technology sub-optimal and consequently motivates policy intervention or is the absence of adoption optimal implying that firms do not automate because they are specialised in products where production should not be automated?
The close collaboration with industry experts and production managers, during firm visits carried out during the development of the automation survey, suggested that the low use of automation to some extent is due to a particular lack of the necessary skills and resources to investigate the firms’ needs, possibilities for automation, and automation planning for the factory floor. The production managers were not unaware that automation technologies existed, but they were lacking knowledge or awareness regarding the specific technologies that they could invest in, on how to implement these, and on which production processes to automate. In this sense, information barriers may be an important market failure that potentially justifies policy intervention.
We find that increasing international competition from China is a driver of automated capital. Increasing international competition from China can, however, not explain changes in the automation score. An important research issue for the future is drivers for the automation score answering the question why some firms have high automation scores while others have low scores.
References
Bartel, A, C Ichniowski, and K Shaw (2007), “How Does Information Technology Affect Productivity? Plant-Level Comparisons of Product Innovation, Process Improvements, and Worker Skills”, Quarterly Journal of Economics, 122, 1721-58.
Bartelsman, E, G V Leeuwen, and H Nieuwenhuijsen (1998), “Adoption of Advanced Manufacturing Technology and Firm Performance in the Netherlands,” Economics of Innovation and New Technology, 6 (4), 291–312.
Bloom, N, P Romer, S Terry, and J Van Reenen (2014), “Trapped factors and China’s impact on global growth”, NBER Working Paper 19951.
Bloom, N, M Draca, and J Van Reenen (2016), “Trade Induced Technical Change: The Impact of Chinese Imports on Innovation, IT and Productivity”, Review of Economic Studies, 83 (1), 87-117.
Bruegel (2017), “Remaking Europe: the new manufacturing as an engine for growth”, in R Veugelers (ed.), Blueprint Series 26.
Council of Economic Advisers (2016), Economic Report of the President.
Doms, M, T Dunne, and K R Troske (1997), “Workers, Wages, and Technology,” Quarterly Journal of Economics, 112 (1), 253–290.
Dunne, T (1994), “Plant Age and Technology use in U.S. Manufacturing Industries,” The RAND Journal of Economics, 25 (3), 488–499.
Graetz, G, and G Michaels (2018), “Robots at Work”, Review of Economics and Statistics, 100 (5), 753-768.
Helper, S, T Krueger, and H Wial (2012), “Why does Manufacturing Matter? Which Manufacturing Matters? A Policy Framework”, Metropolitan Policy Program, Brookings Institution.
Kromann, L, and A Sørensen (2019), “Automation, Performance and International Competition: Firm-level Comparisons of Process Innovation”, Economic Policy (Paper presented at the 69th Economic Policy Panel Meeting of Economic Policy in April 2019), forthcoming.
Kromann, L, N Malchow-Møller, J R Skaksen, and A Sørensen (2019), “Automation and Productivity – A Cross-country, Cross-industry Comparison”, Industrial and Corporate Change, forthcoming.
Don't miss any update on this topic
Create a free account and access your personalized content collection with our latest publications and analyses.
License and Republishing
World Economic Forum articles may be republished in accordance with the Creative Commons Attribution-NonCommercial-NoDerivatives 4.0 International Public License, and in accordance with our Terms of Use.
The views expressed in this article are those of the author alone and not the World Economic Forum.
Related topics:
Forum Stories newsletter
Bringing you weekly curated insights and analysis on the global issues that matter.
More on Manufacturing and Value ChainsSee all
Aarushi Singhania and Kiva Allgood
July 4, 2025
Michael Donatti and Laura Fisher
July 3, 2025
Kaiser Kuo
June 26, 2025
Leo Simonovich and Filipe Beato
June 18, 2025