Here’s how factories can lead in the Fourth Industrial Revolution
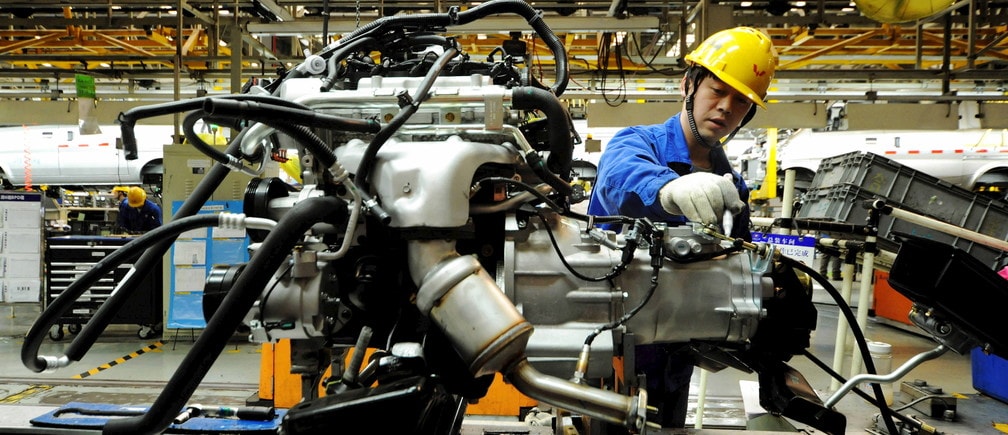
For a group of ‘lighthouse’ companies, AI is transforming the nature of work.
Image: Reuters
Stay up to date:
Fourth Industrial Revolution
There are as many people working in manufacturing in the US now as there were 70 years ago.
At the tail end of 1949, 12.88 million people were employed in manufacturing: seven decades on and almost equal numbers have jobs in the sector, according to the US Bureau of Labor Statistics.
While in 1949 the US was in the middle of a harsh recession, and a push by the White House to boost manufacturing jobs has driven up numbers more recently, the comparison still provides food for thought given the wholesale changes in the economy and broader workplace since.
Despite – and also because of – the changes that have taken place in our factories in previous decades, the manufacturing sector is still ripe for innovation. Many manufacturers have yet to embrace the Fourth Industrial Revolution, turning digitization and analytics to their advantage. Stagnating productivity and volatility are still presenting significant challenges for many.
What is the World Economic Forum doing about the Fourth Industrial Revolution?
However, a group of 'lighthouse' manufacturing companies, identified by the World Economic Forum, in collaboration with McKinsey & Company, are successfully finding opportunity in using Fourth Industrial Revolution technologies. For them, innovations like AI are transforming the nature of the work they do, driving greater efficiencies and enhancing the work of their human employees.
The global Lighthouse Network represents a range of industries and geographies and provides a platform for sharing knowledge and best practices for scaling up technology adoption. Ten new factories have been added to the network.
Here are some of the traits lighthouses have in common:
1. Technology working alongside humans, not replacing them
Contrary to concerns about robots taking our jobs, industry leaders are adopting technology in ways that allow employees in production to enjoy working routines that are less repetitive, and more interesting, diversified and productive.
At the Arçelik lighthouse in Ulmi, Romania, for example, automation of low-value tasks has reduced operational costs by 11%. The Ford Otosan site in Kocaeli, Turkey, meanwhile, uses digital manufacturing and advanced automation to increase its output by 6% and employee engagement by 45% without any additional cost.
2. Big jumps, not small steps
The manufacturing sector has typically been characterized by incremental changes and small improvements: lighthouses, however, are making changes that fundamentally reset industry benchmarks.
Analysis by McKinsey & Co suggests there will be a marked difference between those manufacturers that are early AI adopters versus those that lag behind. As the chart above shows, front-runners can expect a 122% hike in cash flow, versus a 10% cumulative change seen by the followers.
3. Collaboration is key
Innovation happens best in an ecosystem that involves working with universities, start-ups and other technology providers. Leading manufacturers are showing the way but they are not working in isolation.
Nokia’s site in Oulu, Finland uses 5G to bring together its design and production functions to introduce new products. Various technologies connected by a private wireless network have allowed the site to improve productivity by 30%, and it now brings products to market 50% faster than before.
The Posco plant in Pohang, South Korea works with AI to boost productivity and help drive improvements in the steel industry. It is working with academia, SMEs and start-ups to build its own smart-factory platform.
And Schneider Electric’s base in Batam, Indonesia is sharing a number of its technology solutions with its customers and partners, improving the operations of the entire ecosystem.
4. Size doesn’t matter
Innovations with the biggest impact are not the preserve of the biggest companies. SMEs can also make huge changes by focusing on key issues that don’t require significant investments.
Likewise, innovation and access to new technologies isn’t limited to the richest nations. China is home to the largest number of lighthouses, while a number are in Eastern Europe.
5. New isn’t always better
Big changes can be made by adapting existing systems and technologies rather than just by investing in new ones. Legacy equipment has not presented a barrier to innovation for many of the lighthouses, which have instead transformed their existing operations.
The remote location of the Petrosea plant in Tabang, Indonesia throws up a number of challenges. But by adopting technology like optimized truck dispatch, real-time monitoring and drone surveys the mine was transformed from a loss-making entity into a profitable one in just six months.
Don't miss any update on this topic
Create a free account and access your personalized content collection with our latest publications and analyses.
License and Republishing
World Economic Forum articles may be republished in accordance with the Creative Commons Attribution-NonCommercial-NoDerivatives 4.0 International Public License, and in accordance with our Terms of Use.
The views expressed in this article are those of the author alone and not the World Economic Forum.
Forum Stories newsletter
Bringing you weekly curated insights and analysis on the global issues that matter.
More on Fourth Industrial RevolutionSee all
Ibrahim Abdullah Alshunaifi and Caroline Tasse
April 3, 2025
Maria Alonso, Alex Koster and Paul Jordan
April 3, 2025
David Alexandru Timis
March 31, 2025
Utkarsh Amitabh and Ali Ansari
March 28, 2025
Bozhanka Vitanova
March 27, 2025