From Model T to EV: a short history of motor vehicle manufacturing
Ford created the mass-produced motor vehicle industry – and now, EVs are changing it.
Image: REUTERS/Michaela Rehle
Explore and monitor how Mobility is affecting economies, industries and global issues
Stay up to date:
Mobility
You can have any colour you like – as long as it’s black. That’s how Henry Ford is said to have explained the way his mass-manufacturing processes brought affordable, standardized motoring to the American masses.
Ford pioneered the assembly line model of car production still used today. A vehicle travels from one end of the assembly line to the other, with parts and components added along the way. Ford saw this as the best way to produce a high number of cars at the lowest possible cost. It led to the development of the Model T, which was produced from 1908 to 1927 and made car ownership a possibility for many more people.
More than 10 years before Ford’s standardized approach, German engineer Karl Benz created the first motor car. It was a two-seater with just three wheels, but it is generally considered to be the first of its kind.
Since those early days, motor cars have become a global phenomenon – and a global industry.
As some of Europe’s best-known brands look to join forces with the planned merger of Fiat Chrysler Automobiles (FCA) and Groupe PSA, here’s a quick look at the history of global car production.
Ford democratized car ownership by keeping manufacturing costs low enough to produce a lot of affordable vehicles. His assembly line would be the blueprint for the industry – until the next significant wave of change, which came from Japan.
In the 1970s, Toyota introduced the world to "just in time," or JIT. As much a philosophy as it is a production model, JIT was established by Taiichi Ohno, who became known as the father of JIT.
At its heart, JIT is all about reducing waste – all waste, from eliminating production defects to using materials efficiently to cutting down on the amount of time spent waiting or transporting goods. It works by connecting otherwise separate parts of an organization, including people, production plants and processes. JIT has been at the heart of the continued growth of car sales and car ownership.
By forecasting how many units will be made and when, the right number of parts and materials arrive at an appointed time and are used immediately. The approach makes transport and logistics more efficient while reducing excess stock. It also empowers individual workers to point out problems and make sure they are addressed promptly.
The JIT approach allows car makers’ to focus on finding economies of scale, streamlining processes and cutting back on all but the most necessary resources. And that's led to many mergers and acquisitions, with several car brands being passed from one owner to another over the years.
The planned merger of FCA with PSA (which owns Citroen, Opel, and Peugeot) will create a global business valued at around $48.3 billion. If vehicle production numbers remain constant, it will be one of the world’s largest car manufacturers, with economies of scale and shared resources helping propel its ambitious cost-reduction plans.
From Karl Benz to the present day, the car as we know it has been powered by an internal combustion engine, which burns petrol or diesel to propel the vehicle and produces exhaust fumes.
But that is changing. From self-charging and plug-in hybrids to fully electric cars, the internal combustion engine’s days are numbered. According to the International Energy Agency, sales of electric cars almost doubled in 2018. All the major car brands now offer electric vehicles and some, like Tesla, are electric only.
Volkswagen has committed to invest around $33 billion in the electrification of its vehicle portfolio and plans to produce 70 different electric models. It has also been converting an entire manufacturing plant to a dedicated electric facility.
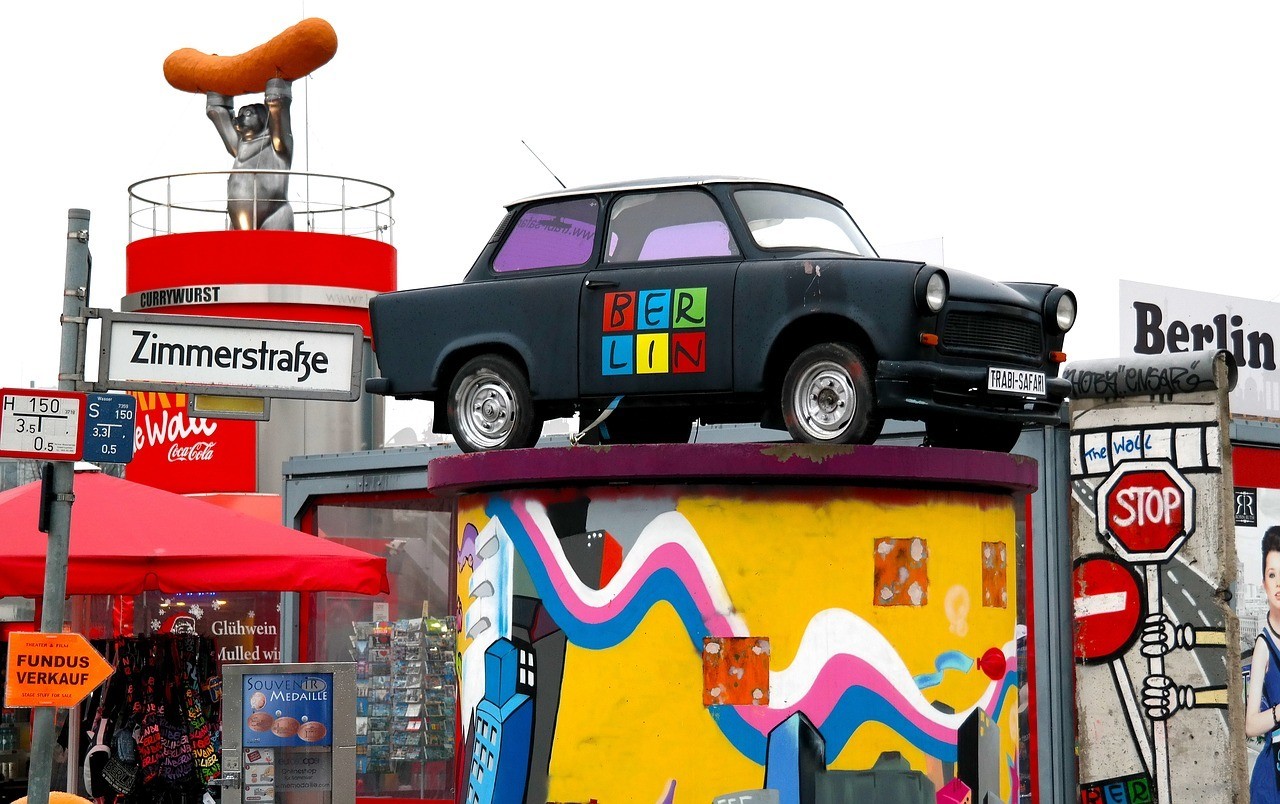
The factory, in the town of Zwickau, once built the iconic Soviet-era Trabant, which was the most commonly driven vehicle in former East Germany. Waiting lists for a Trabant could be several years long.
Looking to the future, Deloitte predicts 2022 will be a “tipping point.” That’s the year the consulting firm expects we will see parity between the cost of electric and conventional cars. And Germany could find itself at the centre of this burgeoning electric car industry, following the announcement by Elon Musk that Tesla will build its first European factory in Berlin.
Don't miss any update on this topic
Create a free account and access your personalized content collection with our latest publications and analyses.
License and Republishing
World Economic Forum articles may be republished in accordance with the Creative Commons Attribution-NonCommercial-NoDerivatives 4.0 International Public License, and in accordance with our Terms of Use.
The views expressed in this article are those of the author alone and not the World Economic Forum.
Forum Stories newsletter
Bringing you weekly curated insights and analysis on the global issues that matter.
More on Supply Chains and TransportationSee all
Mette Asmussen and Pauline Van Ostaeyen
May 2, 2025
Adegboyega Oyedijo and Temidayo Akenroye
April 18, 2025
Zara Ingilizian and Oliver Wright
April 18, 2025
Angie Farrag-Thibault and Natacha Stamatiou
April 9, 2025
Ulrich Scherbel
April 1, 2025