Here’s how smart construction could transform home-building after COVID-19
The pandemic is forcing us to find new ways of building homes and offices.
Image: REUTERS/Pascal Rossignol
Stay up to date:
Future of Construction
- The COVID-19 pandemic is forcing us to find safer and smarter ways of building homes and offices.
- Prefab construction powered by digital technology can help us safely create sustainable, high-quality housing at speed.
- Using big data and artificial intelligence throughout the design and construction process can transform the building sector and help us provide sustainable, affordable housing for all.
As building sites all over the world gradually re-open after lockdown, it’s becoming increasingly clear that construction will look different after COVID-19. Our global public health crisis has confirmed the urgent need for a new way of building homes and offices, using smart construction to tackle design problems, inefficiency, outdated techniques and environmental challenges.
Where sites have re-started, the consensus is that at best, a maximum of 60% of workers can safely return under social distancing rules. Productivity is expected to be 30%-40% lower, meaning projects will take longer to complete. Tighter immigration controls to control the spread of coronavirus will exacerbate the current labor problem in the building sector.
At the same time, demand for high-quality housing is continuing to rise, especially in cities. Offering urban populations better and more spacious accommodation is crucial for reducing overcrowding and preventing future waves of infection. The question is how to do this in a fast, sustainable and environmentally sound way. One answer is prefabricated housing, powered by digital technology.
Unlike traditionally built homes, prefab houses are assembled from components including walls and roofs that are produced in factories and delivered to site for assembly. This helps make them cheaper and faster to build. Digital technology, including artificial intelligence, robotics and the Internet of Things, has also improved the design and production process.
Here are four ways smart, technology-driven construction can transform the building sector, ensuring high quality standards for affordable, factory-built housing and offering a solution to our most pressing housing problems.
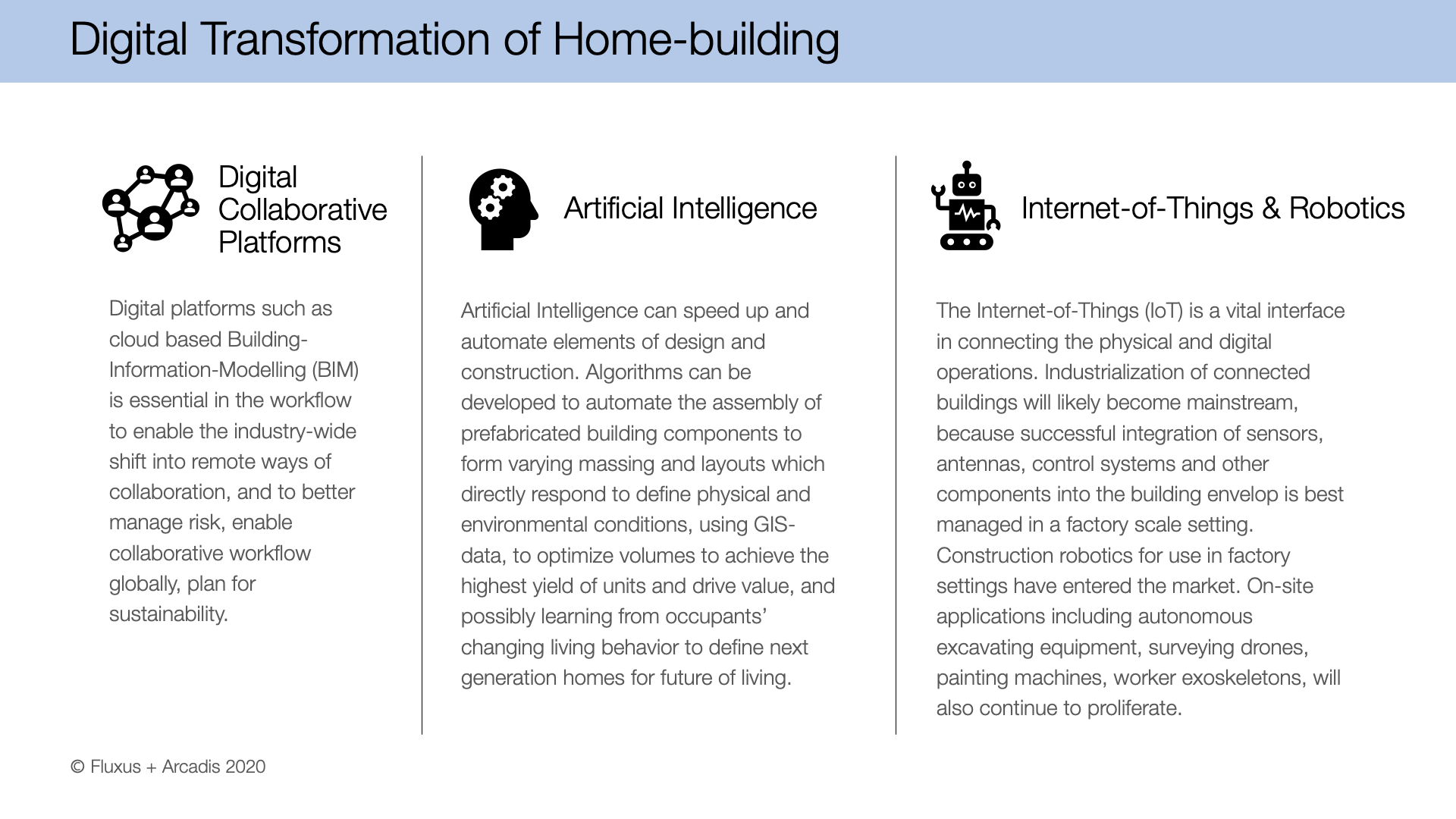
Smarter planning and design
The construction sector is already using Building Information Modelling (BIM), a first step in the digital transformation of the sector. During the COVID-19 lockdown, BIM was more widely adopted in the industry. It enabled projects to continue in a digital and virtual environment even when participants were unable to meet in person. This collaborative approach allows data to be shared across professional disciplines and businesses, and facilitates smarter construction. In the prefab industry, the data can then be fed into manufacturing processes for components and modules that are later put together to form finishing buildings.
Smart technologies including artificial intelligence (AI) can further enhance the design process. They use big data and complex algorithms to create standardized designs at pace. The resulting designs can then be tested on a virtual platform in terms of their viability and cost, the local environment, and the developer’s specific ideas and requirements. This means decisions and commitments can be made at an early stage, which speeds up the whole process.
The standardized components developed this way can then be produced in factories with all the advantages of mass manufacturing, such as reducing costs and improving productivity and efficiency. For this to work on a global scale, manufacturers need to collaborate and combine resources and processes.
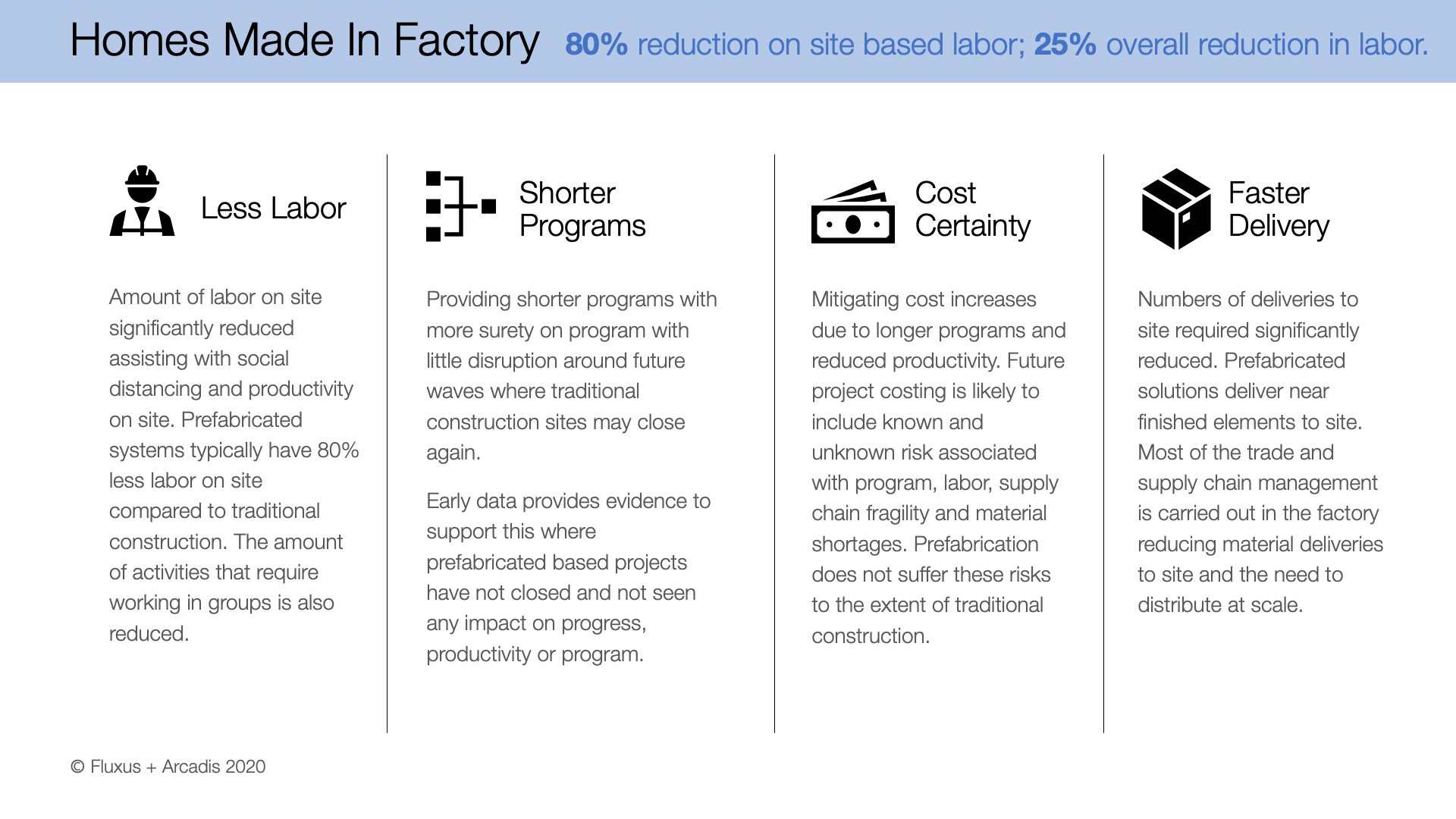
Safer construction
With the right technological support, prefab construction is safer, faster and more reliable than conventional building work.
Factories typically offer a more controlled working environment compared to building sites, with static workspaces and more structured supervision. This makes it easier to implement safety processes and procedures such as physical distancing. Site-based activities, on the other hand, commonly include a lot of interaction between workers.
Technology can support these safe processes by analyzing factory activities and people’s movements within the factory environment. The production process can then be adjusted to separate individuals or create small groups working together.
Pre-manufactured components require minimal labor to install when compared to traditional construction, which reduces accidents on site. Minimal labor not only helps with issues around physical distancing in the COVID-19 context, but also accelerates production.
Other emerging digital technologies include GPS-enabled devices that monitor people’s movements around building sites and alert individuals if they come too close to others, or accidentally mix with those outside their working “bubble”.
How is the World Economic Forum supporting the development of cities and communities globally?
Faster and more predictable timelines
Using smart digital technologies and prefab construction can halve the time of a project, compared to conventional building techniques. This productivity boost is of vital importance when it comes to meeting pent-up demand after the lockdowns.
Prefab housing also offers greater certainty. Conventional building projects regularly see costs escalate and schedules lengthen due to unexpected events such as supply issues or bad weather. Projects that use factory-made components, on the other hand, tend to be very predictable and not impacted by the weather.
As prefab construction gains momentum, data gathered from manufacturing and construction can be analyzed to further understand, optimize and standardize the process.
In the context of COVID-19, such predictability is all the more important as the sector already faces a number of uncertainties, such as the risk of a second wave of infections that could force traditional building sites to close again.
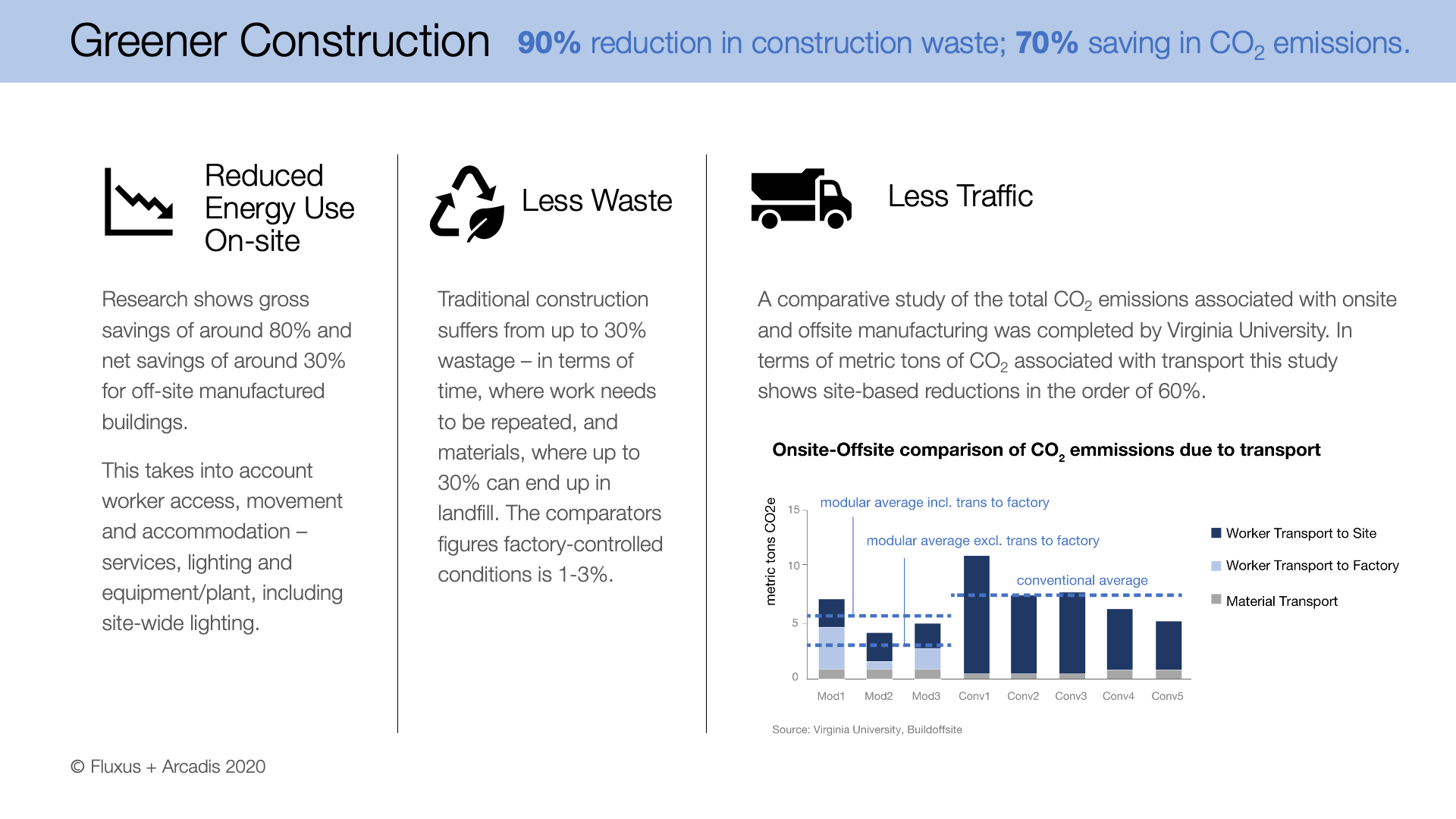
Improving sustainability
The construction industry is estimated to be responsible for 35% to 45% of CO2 released into the atmosphere, making it a major contributor to global warming. Given global commitments to reduce greenhouse gas emissions and fight climate change, the industry needs to urgently adopt more sustainable methods. Prefabrication can be part of the solution.
Manufacturing components in a factory has been shown to cut emissions by up to 60%, compared to conventional construction. One significant factor is the sharp reduction of traffic movements by up to 40%. Conventional building sites typically see a constant flow of vehicles delivering materials and shipping out waste. Factories on the other hand organize deliveries to minimize traffic. Using big data, the scheduling of deliveries can be planned and optimized to reduce frequency, avoid peak times and reduce double handling on site, all contributing to improving sustainability.
Research suggests that prefab construction can cut waste by up to 90% compared to conventional building, partly thanks to the help of data analytics and smart planning.
Modern prefab elements are designed with long-term sustainability in mind, including using data analytics to design homes with optimal energy use and storage. These homes are manufactured using materials that them at a comfortable temperature, reducing the need for extra heating or cooling.
Other smart energy solutions include connecting homes to electric cars, and using the energy stored in the car’s battery to power the home. This can help alleviate peaks in energy consumption caused by sudden high demand at certain times of the day.
Have you read?
New homes for a new era
We are currently in the middle of a global health crisis. Infection outbreaks are frequently associated with low-income, high-deprivation clusters of high-occupancy homes, often with many generations of the same families living together. Alleviating this risk by providing high-quality homes must become an urgent priority for governments everywhere.
Traditional construction techniques will always play a role in the housing sector. They can be useful for small and more complex buildings, or the replication and restoration of historic buildings. However, prefab construction has the potential to take us into a new and more sustainable and affordable era of home-building. Supported by digital technologies, it presents an unprecedented opportunity to provide comfortable and affordable housing to a growing global population.
Taking inspiration from more technologically advanced sectors such as the automobile industry, robotics would be the next natural step in the housing production process. Robotics and automation could speed up production even more, and make it even safer.
The key is to collaborate on a global scale, and share the best solutions so we can all advance together, create a pool of talent, research and development, and make use of economies of scale. One way to do this would be to develop a blueprint for so-called Global Powerhouse Hubs that connect industry players all over the world, allowing them to exchange best practices, align their strategies and co-operate throughout the supply and production chain.
Technology has helped many of us weather the crisis. Now is the time to tap its potential in the construction sector, putting humans at the center to make a positive impact on communities all over the world.
Don't miss any update on this topic
Create a free account and access your personalized content collection with our latest publications and analyses.
License and Republishing
World Economic Forum articles may be republished in accordance with the Creative Commons Attribution-NonCommercial-NoDerivatives 4.0 International Public License, and in accordance with our Terms of Use.
The views expressed in this article are those of the author alone and not the World Economic Forum.
Forum Stories newsletter
Bringing you weekly curated insights and analysis on the global issues that matter.
More on Health and Healthcare SystemsSee all
Shyam Bishen
July 7, 2025
Daniel Mahadzir and David Yip
June 30, 2025
Madeleine North
June 27, 2025
Plínio Targa
June 27, 2025
Alexandros Pantalis and Ithri Benamara
June 25, 2025