5 ways to empower the manufacturing workforce to survive the pandemic and thrive beyond it
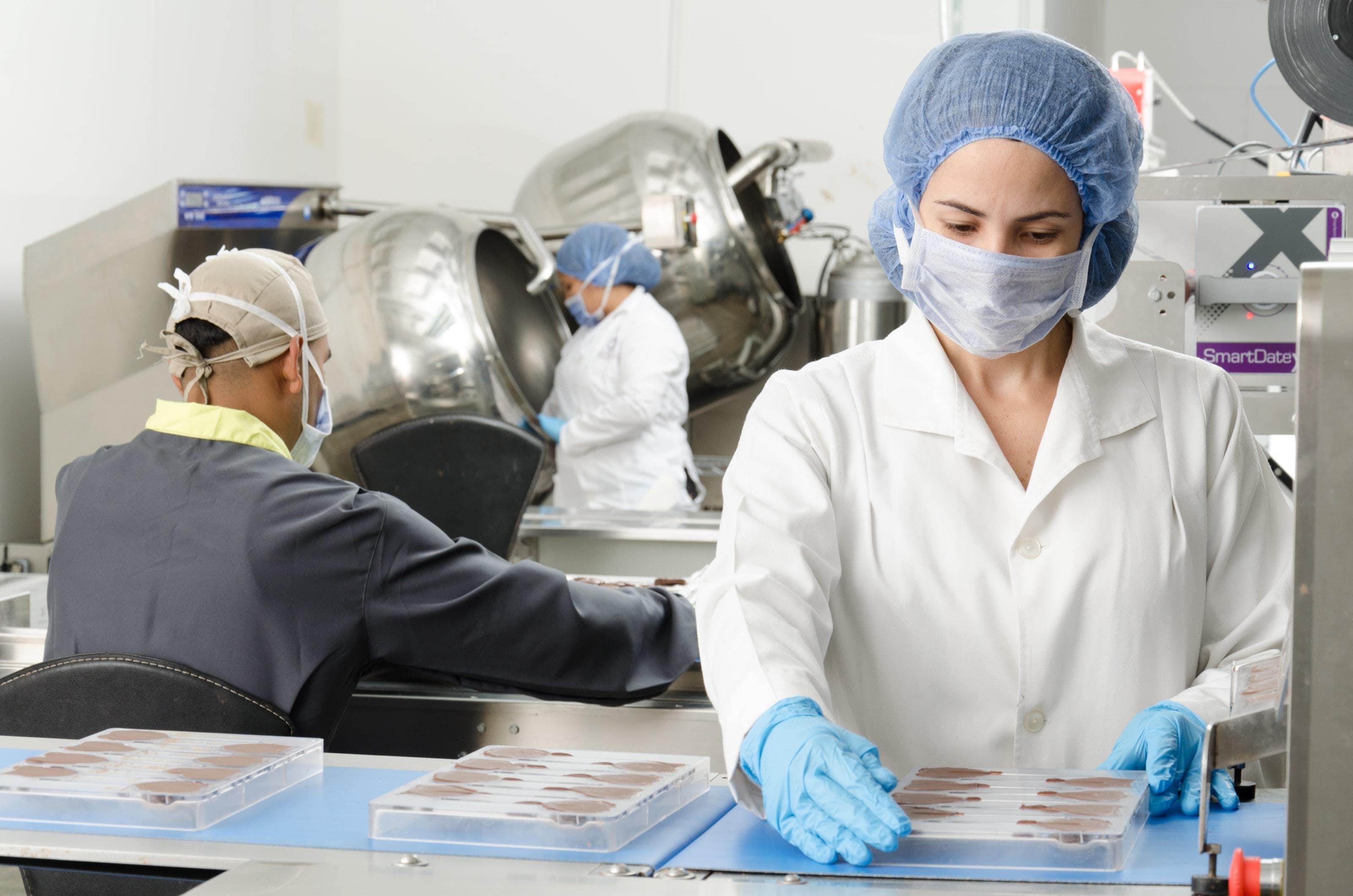
Advanced manufacturing has accelerated due to COVID-19.
Image: Photo by Walter Otto on Unsplash
Stay up to date:
Future of Manufacturing
- Before the COVID-19 pandemic, labour flexibility, digital transformation and operational excellence were key pillars of an emergent Fourth Industrial Revolution. Now, these areas provide vital lifelines to build resilience during the crisis and beyond.
- There is now more global recognition of the need for ongoing agile operations to accelerate the adoption of modern digital tools to improve the status and proficiency of frontline work.
- The industrial companies that take bold action to shore up their workforce and technology investments will emerge more resilient, and more likely to succeed no matter what uncertainties come their way.
Ten months ago, the first cases of COVID-19 were detected. In the time since, companies, supply chains and entire economies have been disrupted and forced to adapt to a "new normal" where change is constant, and agility is critical. More than 48% of respondents in a recent Forum survey of the world's top risk experts said they were most worried about a disruption of global supply chains. Another Forum report states that the COVID-19 crisis has impacted more than 75% of the world's manufacturing outputs.
As important as it is to address immediate needs and concerns while COVID-19 case rates fluctuate around the world, manufacturers must prepare for recovery and the Great Reset ahead.
“Now more than ever, industry leaders have realized that they need to transform towards agile and sustainable manufacturing. Companies must be ready for a skill shift with a rising demand for technological, social, and higher cognitive skills.”
Even before the pandemic, labour flexibility, digital transformation and operational excellence were key pillars of an emergent Fourth Industrial Revolution. Now, these areas provide vital lifelines to build resilience during the crisis and beyond. A profound sense of urgency has organizations seeking more pragmatic solutions and approaches to identifying the skills, practices and technologies most important to resilience and a successful recovery – and rapidly scaling up the programmes they've found to be effective.
While the rise in adoption of modern digital tools for frontline workers was very noticeable in 2019, perhaps one of the few positives this year is the way in which the spotlight was thrown on these essential workers. There is now more global recognition of the need for ongoing agile operations to accelerate the adoption of modern digital tools to improve the status and proficiency of frontline work.
5 workforce priorities during the pandemic and beyond
Over the past several months, members of the Forum's Platform for Shaping the Future of Advanced Manufacturing and Production and of the Platform for Shaping the Future of the New Economy and Society – including global industrial and manufacturing companies, academic institutions and technology providers – have come together to identify key workforce priorities, skills and tools that have not only proven critical for keeping operations running during the pandemic, but will be essential to recovery of the manufacturing and production ecosystem.
In a recent survey of manufacturing companies, respondents were asked to assess their own organizations with input from the shop floor, executives and peers.
The dominant theme: “Empowering the factory workforce with knowledge and digital tools”, will be essential to surviving the current pandemic and ensuring that operations can adapt to change anytime, anywhere – crisis or not. Along with that, having strong operational standards and lean practices are critical for navigating this crisis and the future of manufacturing.
More specifically, the survey highlights five priorities.
1. Employee safety and wellbeing
- Every member of the team plays a part in keeping our workforce and families safe both inside the plant and at home.
- Focused safety culture with expanded PPE requirements and ownership at all levels of organization.
Employee health and safety in industrial environments have always been a priority, but the COVID-19 crisis escalated this. Manufacturing facilities have opened up (if they shut down at all) and frontline workers have been at the centre of the disruption. A key issue is building workers' trust in their employers' ability to keep them safe and protected, and to prioritize their overall mental wellbeing.
Calling factory workers “heroes” is not enough. Instead workers want and need to have a direct say in whether they return to work, how they return, and what safety conditions are in place. Top down directives and leadership need to be matched by bottom-up input and real influence in these decisions and in their monitoring and enforcement. Where unions and/or works councils are present, these institutions need to be engaged in shaping the new workplace conditions.
2. Cross-training, upskilling and professional development
- We encourage continued professional development, plan webinars for them to join and expand their knowledge and extend their networks. The key is to keep them engaged.
- The 2+1 trained operator strategy has been highlighted as an improvement opportunity and a huge benefit from risk mitigation.
The uncertain nature of this crisis has highlighted the importance of workforce development and cross-training on the frontlines. Manufacturers had to rapidly undertake line changeovers to produce different products, volumes and combinations, and had to manage taking over the lines of sick workers.
Software that provides just-in-time digital content and learning – like digitized, interactive work procedures that ensure every step is accurately followed and information is readily available via a mobile device – are becoming a factory floor norm. Companies that provide opportunities for employees to build multiple competencies, from technical skills (automation, IT, engineering, data science) to "soft" skills (communication, adaptability, ownership, collaboration, problem-solving), will be more resilient in the long term.
3. Technology adoption to increase agility
- The climate has promoted the need to review our digital strategy to explore extending the 'digital thread' throughout our operation, supply chains and even into our OEM customers.
- Shop floor dashboards helped the team to stay aligned on critical production issues.
The lack of modern digital tools for frontline workers has been on the agenda for some time, but COVID has kicked in the need to provide these tools for greater agility’.
Technologies that support remote work, like digital twins, augmented reality, remote machine monitoring and digital dashboards, are helping companies maintain business flexibility now and in the years ahead. Automation and robotics help ensure operations continue when unpredictable staffing challenges and workforce shortages arise. Also, engaging workers as partners, enabling them to contribute to the design and deployment of new technologies is critical in driving support and adoption.
“This pandemic has taught us the importance of standard work and a cross-functional workforce, especially when you consider that workforce availability may be disrupted at any time. The use of digital tools and technologies have aided this greatly, including our support functions who can work remotely better than ever before, while still allowing our manufacturing facilities to stay open and run at capacity.”
4. Continuation of remote work
- We have learned that we are truly a distributed workforce, which means that post-COVID, we have an opportunity to continue collaborating via Zoom, Microsoft Teams, etc. We have learned that we are able to work from home.
- Leading virtual teams is a skill.
Manufacturing companies should expect to support remote work and continue to remotely collaborate with their customers and suppliers in the foreseeable future. For most organizations, the COVID-19 crisis revealed not only the extent of their ability to support and manage a remote workforce, but how quickly digital technologies enabled them to adapt to this new way of operation and collaboration.
Moreover, in deciding who can return to work it is imperative that each employee’s personal health and family circumstances are considered. No two employees’ circumstances and risks are likely to be identical, even for two otherwise similar people who do the same or very similar jobs. Some mix of remote and on-site work will likely be the norm for many people for a long time to come. Managing these diverse situations, and respecting them, will be a considerable challenge.
“My mother always used to say, ‘one size fits no one,’ and that is certainly going to be true as workplaces—especially companies with multiple work arrangements in various locations across different stages of the pandemic—determine how to reopen. For reasons aside from the health risks, some leaders might decide not to bring certain employees back in the office, as they’ve become acclimatised to a ‘new normal’ that is fully remote, including for business functions previously considered impossible to perform from home.”
5. Organizational communication and visibility
- We have made sure to not only expand safety measures (PPE, temperature monitoring, expanded cleaning) but explain to each employee why.
- Communication is the biggest key. The situation is changing rapidly, and our responses are evolving as we share best practices with our peers. Keeping our team abreast of the new normal is essential.
Hand in hand with remote work as the "new normal" is the need to almost over-index on workforce communication and transparency – as frontline workers on site need to stay connected across other teams, locations and plant managers that can no longer easily walk around the factory floor. Teams must prioritize regular communication and promote a truly people-first culture. Communication must be bottom up as much as top down. Enabling workers to speak up and listening and responding to the workforce will be more critical as standard managerial practices than before the crisis.
An opportunity to build resilience
People, companies and society have been affected by the COVID-19 crisis in unimaginable ways. Looking ahead, the industrial companies that take bold action now - in partnership with their workforce and labour institutions - to shore up their workforce and technology investments will emerge more resilient, and more likely to succeed no matter what uncertainties come their way.
“In the past few months, we’ve seen that a connected workforce is a competitive advantage. Digital technologies have been essential for safety, retooling, and ramping up. And that all starts with the workforce. Workers who can adapt their operations to changing conditions--whether sudden disruptions or naturally evolving markets--are the foundation of a resilient business."
Don't miss any update on this topic
Create a free account and access your personalized content collection with our latest publications and analyses.
License and Republishing
World Economic Forum articles may be republished in accordance with the Creative Commons Attribution-NonCommercial-NoDerivatives 4.0 International Public License, and in accordance with our Terms of Use.
The views expressed in this article are those of the author alone and not the World Economic Forum.
Related topics:
Forum Stories newsletter
Bringing you weekly curated insights and analysis on the global issues that matter.
More on Manufacturing and Value ChainsSee all
Leo Simonovich and Filipe Beato
June 18, 2025
Benedikt Gieger and Isabell Steidel
June 12, 2025