These researchers 3D-print bridges with dramatically less waste and CO2
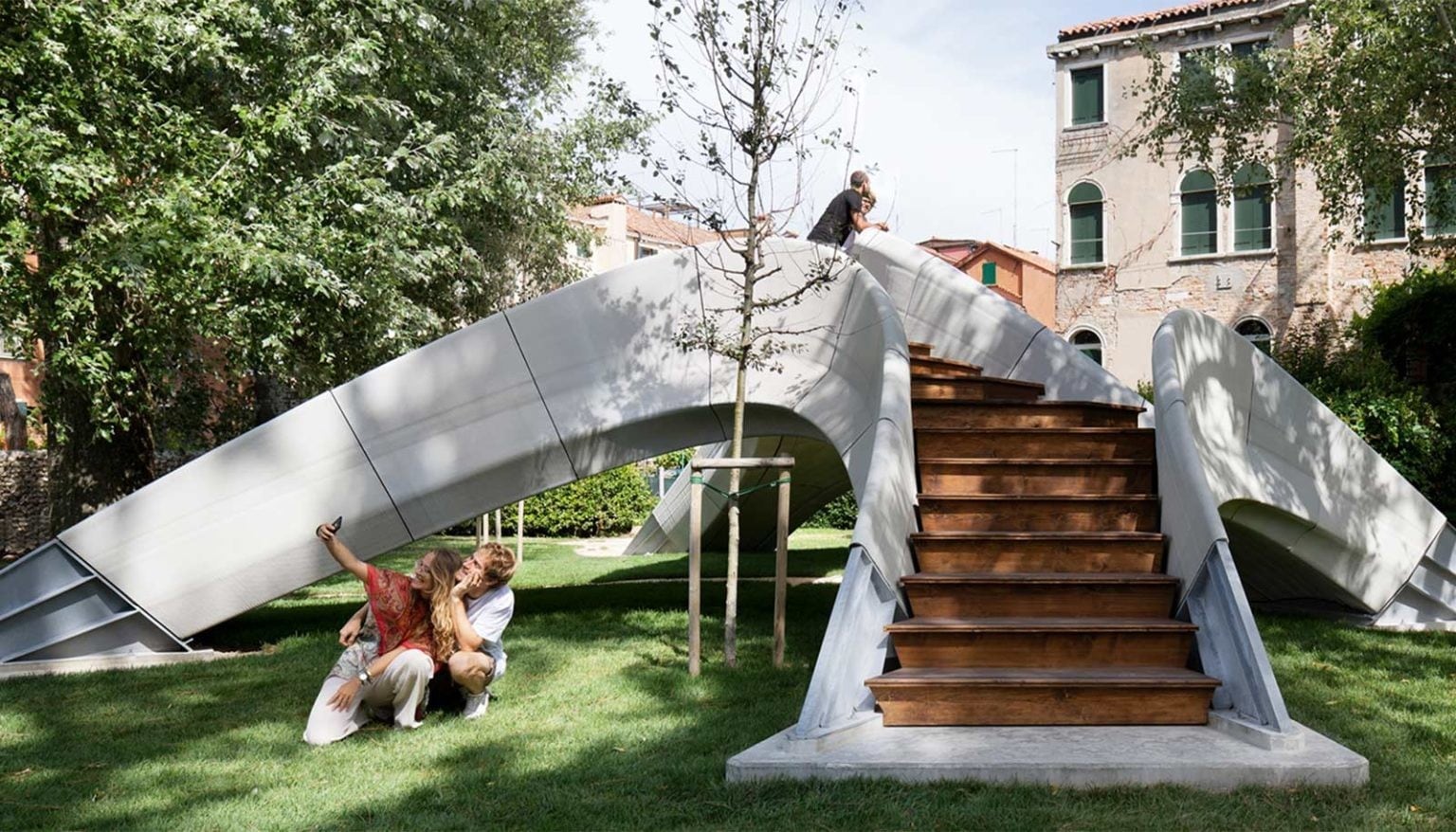
The concrete is not applied horizontally in the usual way but instead at specific angles.
Image: Studio Naaro
Stay up to date:
Engineering and Construction
- ETH Zurich architects and engineers from the Block Research Group built a 12-by-16-meter arched footbridge entirely without reinforcement.
- These steel reinforcements and the cement for the concrete typically generate large amounts of CO2 and have been cut from the process.
- Due to the structural design, these bridges can also be moved to a different location, damage-free, offering a host of new opportunities in the construction space.
Accept our marketing cookies to access this content.
These cookies are currently disabled in your browser.
Millions of new buildings all over the world are being constructed with reinforced concrete, even though this type of construction generates large amounts of CO2 emissions.
The steel used for the reinforcement and the cement for the concrete are especially problematic in this regard. The researchers have now presented a way to reduce both, in a real project.
ETH Zurich architects and engineers from the Block Research Group in collaboration with Zaha Hadid Architects built a 12-by-16-meter (around 39.37-by-52.5 feet) arched footbridge in a park in Venice—entirely without reinforcement.
Using an additive process, the construction dubbed “Striatus” was built with concrete blocks that form an arch much like traditional masonry bridges. This compression-only structure allows the forces to travel to the footings, which are tied together on the ground. The dry-assembled construction is stable due to its geometry only.
What is completely new is the type of 3D-printed concrete, which the researchers developed together with the company Incremental3D. The concrete is not applied horizontally in the usual way but instead at specific angles such that they are orthogonal to the flow of compressive forces.
This keeps the printed layers in the blocks nicely pressed together, without the need for reinforcement or post-tensioning. The company Holcim developed this special concrete ink for the 3D printer precisely for this purpose.
“This precise method of 3D concrete printing allows us to combine the principles of traditional vaulted construction with digital concrete fabrication to use material only where it is structurally necessary without producing waste,” says Philippe Block, a professor at ETH.
Because the construction does not need mortar, the blocks can be dismantled, and the bridge reassembled again at a different location. If the construction is no longer needed, the materials can simply be separated and recycled.
Accept our marketing cookies to access this content.
These cookies are currently disabled in your browser.
Don't miss any update on this topic
Create a free account and access your personalized content collection with our latest publications and analyses.
License and Republishing
World Economic Forum articles may be republished in accordance with the Creative Commons Attribution-NonCommercial-NoDerivatives 4.0 International Public License, and in accordance with our Terms of Use.
The views expressed in this article are those of the author alone and not the World Economic Forum.
Forum Stories newsletter
Bringing you weekly curated insights and analysis on the global issues that matter.