How the petrochemicals industry can reduce its carbon footprint
The technology exists to reduce syngas CO2 emissions.
Image: Pexels.
Stay up to date:
SDG 13: Climate Action
Listen to the article
- The chemical building blocks derived from petrochemicals continue to play a crucial role in society.
- Syngas production contributes significantly to petrochemical CO2 emissions.
- The technology exists to significantly reduce syngas CO2 emissions at scale and help the industry on its road to net zero.
Petrochemicals have played a crucial role in society for over 50 years and throughout that time the industry has constantly evolved, adopting novel technologies and processes to drive efficiency improvements and cost reductions. The focus is now on how to reduce the carbon footprint of the chemical industry, which is the third largest emitting industry behind the iron/steel and cement industries.
According to the IEA, 2018 CO2 emissions from the chemical sector were 1.5 gigatonnes or 18% of industrial CO2 emissions. A significant quantity of this CO2 originates from syngas derived from fossil fuels. The technology to substantially reduce these emissions already exists and it can help the chemical industry as it moves towards net zero.
Not all syngas CO2 emissions are the same
Syngas production uses steam methane reformer (SMR) technology to convert natural gas into a mixture of predominantly hydrogen and carbon monoxide – referred to as syngas. Syngas gets its name from its use as a building block for the synthesis of other chemicals including ammonia fertilisers, cleaner burning fuels for transport, ethylene, propylene and butadiene for plastic production, and commodity chemicals such as methanol.
Methanol is used to make thousands of products used in practically every aspect of our lives, including acrylic plastic, synthetic fabrics and fibres used to make clothing, adhesives, paint, and plywood used in construction, and as a chemical agent in pharmaceuticals and agrochemicals. Hydrogen can also be used to power fuel-cell cars and trucks, and will work alongside battery technology to drive the decarbonization of the transport sector.
Steam reforming is an endothermic process, which means that high levels of heat need to be supplied to drive the reaction; in the traditional SMR process this heat is generated by burning methane in a separate process stream, which produces CO2 resulting in a high carbon intensity for this process. Carbon capture and storage (CCS), in which the CO2 is captured and subsequently stored (for example in depleted oil and gas fields), can reduce the carbon intensity of the SMR process.
What's the World Economic Forum doing about the transition to clean energy?
Unfortunately, this “post combustion” (Fired CCS) CO2 is generated as a dilute, relatively low pressure stream, making it tricky and relatively expensive to capture. The other significant source of CO2 comes from the process side reactions during syngas production, and the capture of this process CO2 (Process CCS) is less complex and costly as it has a more consistent composition, fewer impurities, and leaves the reactor at a favourable (high) pressure for capture using established solvent and absorbent-based technologies.
Advanced reforming generates CO2 which can be captured
The good news is that there is a proven way to generate syngas at scale in which all the CO2 (Process CCS) comes out in a single stream at high pressure, making it easy and economical to capture with very high efficiency – 95% and above. Advanced reforming, utilizing Gas Heated Reforming (GHR), and Autothermal Reforming (ATR), has been used at industrial scale for decades, and removes the need for a separate stream of methane to be used to generate the temperature to drive the reactions. This in turn eliminates the dilute, low pressure outlet stream containing CO2 (Fired CCS). As the figure below illustrates, using advanced reforming with CCS enables the production of hydrogen with a very low carbon intensity, which will keep this process relevant through to 2050 and beyond.
A further advantage of advanced reforming is that it uses the natural gas within syngas production more efficiently, leading to lower operating costs.
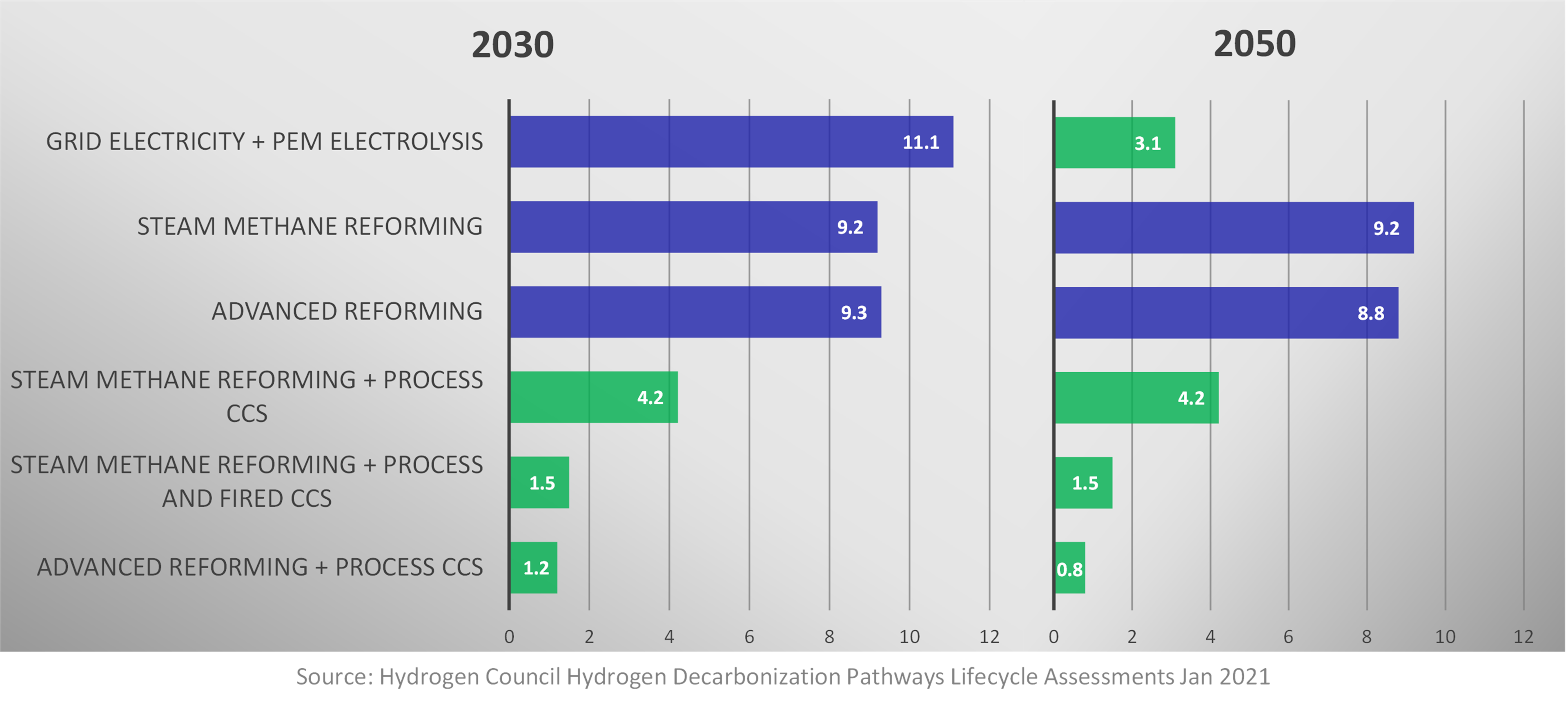
Renewable carbon sources sustain petrochemicals viability
In the broader context, the products made by the chemical industry contain carbon, and this will continue, so a carbon-free chemical industry isn’t possible. However, as outlined above, the industry can, and will, find ways to use the carbon more efficiently, reducing carbon intensity, and reducing CO2 emissions to very low levels.
As part of this drive, the industry is looking at ways to make chemicals using renewable carbon sources, such as biomass, municipal solid waste and captured CO2. Combining this carbon with hydrogen generated by electrolysis powered by renewable electricity enables further carbon footprint reductions.
For example, captured CO2 and renewable hydrogen can be directly transformed into methanol, or can be converted within the reverse water-gas shift reaction to a syngas containing CO, CO2 and hydrogen, which can be further processed through well-established Fischer-Tropsch synthesis processes to make chemicals and fuels. This is one route to make drop-in fuels for planes – such as Sustainable Aviation Fuel (SAF) which is regarded as critical to assist the decarbonization of aviation. In addition, syngas-based technologies can be used to store and transport renewable energy in the form of methanol and ammonia and are being proposed as fuels for sustainable shipping.
Moving towards net zero
Achieving net zero targets and limiting global temperature increases to the 1.5C recommended by the intergovernmental panel on climate change is going to be very challenging, and governments and industry will need to deploy a range of technologies to meet these goals. Advanced reforming technology, available and proven at large scale today, can play a key role in the move towards net zero, by enabling the production of syngas with a very low carbon footprint. This syngas, and the hydrogen within it, can help to reduce the carbon footprint of the chemical industry substantially, and will support the decarbonization of other sectors such as transport and agriculture. And the beauty is that the route to deploy this technology at scale and with very low CO2 emissions exists today and its deployment will give the world a great head start in the race to net zero.
Accept our marketing cookies to access this content.
These cookies are currently disabled in your browser.
Don't miss any update on this topic
Create a free account and access your personalized content collection with our latest publications and analyses.
License and Republishing
World Economic Forum articles may be republished in accordance with the Creative Commons Attribution-NonCommercial-NoDerivatives 4.0 International Public License, and in accordance with our Terms of Use.
The views expressed in this article are those of the author alone and not the World Economic Forum.
Related topics:
Forum Stories newsletter
Bringing you weekly curated insights and analysis on the global issues that matter.
More on Industries in DepthSee all
Francisco Betti
May 9, 2025
David Elliott and Johnny Wood
April 25, 2025
Katia Moskvitch
April 14, 2025
Cathy Li and Andrew Caruana Galizia
March 3, 2025
Francesco Venturini and Bart Valkhof
February 27, 2025