Automation can empower workers and enhance productivity. Here's how
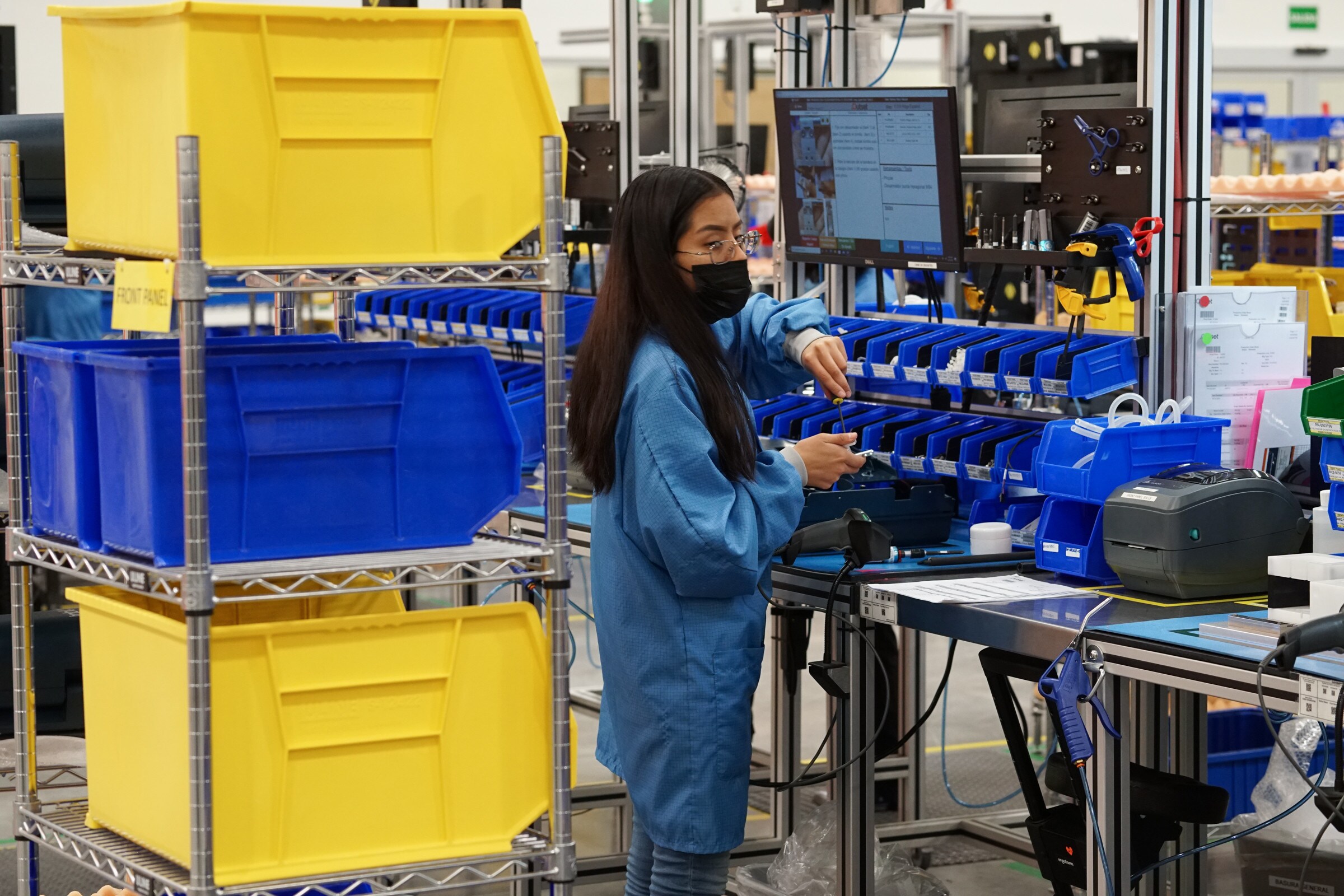
Image: Outset
Stay up to date:
The Digital Transformation of Business
- 'Augmented Lean' is a concept that highlights how technology interfaces have to foster intrinsic workforce motivation, excitement and empowerment, with a workforce that is efficient and enhanced.
- Augmented lean organizations require a new breed of emergent governance, which is a combination of leadership and workers interacting with technology to change how a company works.
- Here is an example of five key aspects all of which emerged in a collaborative process.
Successful digital transformation is the holy grail of many manufacturing firms, but it does not always come easy. The failure rate is high, because companies tend to start with complex technologies promising efficiencies, not with the needs of their workers. By reversing this focus, success can be achieved.
This is the essence of Augmented Lean, the view that in order to achieve transformative effects from efficiency investments, technology interfaces have to foster intrinsic workforce motivation, excitement and empowerment. The workforce needs to be both lean (efficient), and augmented (enhanced). That being said, in the last 30 years, industrial tech has fostered the opposite: demotivation, frustration, and disempowerment, because it wrongly attempted to automate the workforce away prematurely.
On the brink of a new technological revolution
The Fourth Industrial Revolution requires awareness of how humanity is at the brink of a new technological revolution, with distinct velocity, scope, and systems impact. The Forum's Global Lighthouse Network, with its best practice examples from the world’s best factories, emphasizes excellence in large industrial factories that are taking these lessons.
But this has been tricky to achieve for smaller factories. What’s now needed is a management framework to help all stakeholders achieve the full benefits of industrial technology.
Implementing an Augmented Lean framework
To this end, industrial leaders must first understand that they can digitally transform their companies in (at least) four ways, by choosing between an agile and an incremental rollout, and by either planning the details or letting changes emerge. It is important, however, to realise that there is no one best way.
Augmented lean organizations demand full attention from their workers. Implementing such a framework requires embracing a new breed of emergent governance, which is a combination of leadership and workers interacting with technology to change how a company functions.
To achieve that, organizations need to establish principles that value openness to change within certain constraints. Specifically, the eight principles are learn, emerge, augment, decentralize, empower, respect, hack, and govern. These principles, that combine top-down and bottom-up approaches, also work in smaller organizations.
An agile and emergent transformation
A clear example of this framework in action is the transformation of a greenfield factory in Mexico (OMM), at Outset Medical, a US-listed medical device manufacturer based in San Jose, California, that was both agile and emergent. This is perhaps the most risky strategy but also the approach with the most visible rewards.
This flies in the face of the adage that it’s typical for an SME – with fewer resources at hand when compared to large companies – to experience significant challenges while innovating, growing and digitally transforming at the same time. The secret was simple and meant deeply involving the workforce, the creation and execution of a laser focused 4IR roadmap and the deployment of frontline apps from Tulip.
A core part of Outset’s product, consoles, are manufactured in Mexico, at a facility that was built from scratch. Outset designed, built, grew and scaled the facility in nine months. At the six-month mark, it had already ramped up capacity by six times. All digital apps needed for Outset’s transformation were built internally by six people on site.
Augmented lean production, an approach which prioritizes worker empowerment over machine efficiency, is best accomplished as a team effort where organizations are ruthless in the pursuit of democratization. They start to run first. Then, they learn and let a dedicated set of employees create governance, training and agile project charters in sprints with an 18-month roadmap. Once the foundation was in place, Outset and Tulip started auditing app building documentation methods, as well as performing monthly audits for IoT connectivity on the floor.
How to be Augmented Lean
The augmented lean process that Outset employed had five key aspects all of which emerged in a collaborative process with the workforce:
1. Empowerment
Empowerment is easy to target but hard to do in practice. However, through upskilling and professional development, 60% of Outset’s direct labor have high school diplomas (compared to 23% in the industry).
2. Sustainability
Sustainability is key. Sensor-connected water conservation systems enable the facility to recycle more than 50% of its water usage used during Finished Goods testing. Ultra-high-efficiency HVAC systems leverage technology designed to utilize only 1/3 of the energy required to provide a cool and comfortable working environment for the team.
3. Connectivity
Connectivity at the enterprise level has reduced ERP transactional work by over 40,000 transactions a week.
4. Manufacturing agility
Manufacturing Agility from more than 100 smart workstations provide a seamless experience for operators, from their interactive interview through training and into operations, representing a reduction in training time by 60%.
5. Capabilities
Capabilities must be continuously developed, in a systematic fashion, no matter the starting point. That way, future growth opportunities in the areas of additive manufacturing and vision system development, were identified and acted upon.
Outset achieved significant results by joining forces with a frontline operations platform where, from day one, Outset’s industrial engineers took full ownership of the platform. That way, it got configured the way workers needed, and did not get delivered as a fixed solution to adapt to.
Tailoring the augmentation process to the company's needs
As long as smaller companies keep the mantras of augmented lean management at top of mind, emphasizing augmenting workers over efficiencies from pure automation, they can be nimble and scalable in the pursuit of digital transformation. Balancing an initial deployment mentality with a process to eventually implement a light, but robust governance structure, is key.
We recommend that others who are looking to digitally transform their manufacturing deploy the same augmented lean principles but adjust their approach to their own industry, context, culture and circumstances. Most important is not to let go of important company principles just to fit an IT solution that is supposed to be best-in-class. For example, among those that can be said to practice augmented lean include companies as different as Stanley Black & Decker, DMG MORI and J&J.
Each tailor-made their own augmented process, and scaled but only after certain checks-and-balances, most notably buy-in from their industrial engineers. In our view, the real champions for organizational or technological change must always be internal to the company, never consultants or service providers. With a bit of effort, even smaller organizations can learn, emerge, augment, decentralize, empower, respect, hack, and govern – as they see fit. With these points in mind, company size is no longer a major limiting factor for process change, since every relevant variable scales organically.
Don't miss any update on this topic
Create a free account and access your personalized content collection with our latest publications and analyses.
License and Republishing
World Economic Forum articles may be republished in accordance with the Creative Commons Attribution-NonCommercial-NoDerivatives 4.0 International Public License, and in accordance with our Terms of Use.
The views expressed in this article are those of the author alone and not the World Economic Forum.
Forum Stories newsletter
Bringing you weekly curated insights and analysis on the global issues that matter.