3 challenges en route to electric vehicle batteries driving the circular economy
Electric vehicles could lead us to a low-carbon future – if we can recycle their batteries.
Image: Reuters/Fabrizio Bensch
Explore and monitor how Mobility is affecting economies, industries and global issues
Stay up to date:
Mobility
Listen to the article
- Batteries are an enabler of the shift to a low-carbon society – at least one in two cars sold in 2030 is expected to be electric.
- While EVs are driving 90% of the global demand for lithium-ion batteries, collaborative networks capable of efficiently retrieving scarce materials to maximize their lifespan have yet to form.
- Industry players in the Circular Cars Initiative have designed a circular blueprint for EV batteries for maximizing their sustainability.
Between 2020 and 2021, electric vehicle (EV) sales increased by 50% to 6.6 million vehicles. By 2030, EVs could exceed 50% of total automotive sales in markets, backed by major markets’ internal combustion car phase-out regulations. As cars, trucks and buses are increasingly battery-powered and generate zero tail-pipe emissions, the increasing demand for road mobility can be met without compromising global warming and people’s health. But what happens when the battery that powers an electric vehicle is no longer fit for use? Are we resolving one challenge by creating the next big one?
The complex set of batteries in an electric car is made of materials including cobalt, copper, lithium and nickel – scarce metals whose mining carries harsh environmental and social costs. The bulk of a new battery’s carbon emissions stem from mining and refining processes, the societal impact of which is far from being resolved. Similarly, the disposal of batteries, classified by the Basel Convention as hazardous, can create further sustainability challenges and costs.
We are proud to be a champion company for the Circular Cars Initiative as it seeks to bring industry leaders together to minimize total lifecycle emissions within the automotive value chain. ADI is committed to empowering intelligence at the cutting edge and transparency into the battery lifecycle management – right from its formation through to second life applications
”In order to electrify the mobility sector, batteries need to be collected, treated, reused and recycled effectively. By 2030, more than 1 million such batteries will need to go through this process in Europe alone. Recycled materials can cut about 40% of a battery’s carbon footprint, and address the bulk of an EV’s life cycle footprint. This has an enormous impact on electric vehicles, as half of the production emissions are embedded in the battery. However, three challenges stand in the way:
1. Building capacities along the EV battery value chain
Because each EV battery holds a pack of battery cells, analyzing its state is no simple task. Once batteries’ quality and depletion are assessed, the future of each one needs to be determined – not depending simply on a single company, but by overall market capacity to treat it as efficiently as possible. Batteries with some power left, for example, can be given a second life as power packs for mobile vehicle charging. Batteries that have little left to give can be ground down to a fine powder to extract raw materials such as lithium, nickel, manganese and lithium – and then re-enter the EV battery production cycle. Dedicated regional centres that could receive and safely store a wide variety of end-of-life batteries are only in their infancy.
Only by adopting a circular approach can we support our ultimate goal of net-zero transport in the coming years, one that is enhanced through partnerships with every player on the electrification journey, at every stage of our sustainable transport’s development
”2. Making the business case for EV battery value-chain investment
The costs associated with collecting end-of-life batteries and managing the necessary logistics impact the overall business case and hamper creating economies of scale. The cost of individual battery collection is the most significant issue in battery-powered transportation today, according to Circular Cars Initiative community members. The transport of End of Life (EoL) batteries alone can amount to 41% of battery recycling costs.
Umicore is building on its track record in battery recycling and is preparing for the future incoming wave of end-of-life batteries to ensure that no strategic metals go to waste. The Circular Cars Initiative offers a much-needed opportunity to get the most out of battery recycling in this unseen mobility transformation
”The EV battery market is booming. The market for battery cells alone is expected to grow by over 20% annually, reaching $360-410 billion by 2030. Yet though auto manufacturers and suppliers are experimenting with EoL business creation, the commercial case has not been demonstrated at scale. This greenfield is sometimes untapped collaboratively because companies view this as a competitive area. A dozen companies involved with the Circular Cars Initiative along the car battery value chain, including Analog Devices, CATL, DHL, Hoppecke, Jaguar Land Rover, Li-Cycle, Mahindra, Mercedes-Benz, Volvo Group and Umicore, were therefore motivated to develop a blueprint to forge partnerships and improve the business case for value-chain battery management:
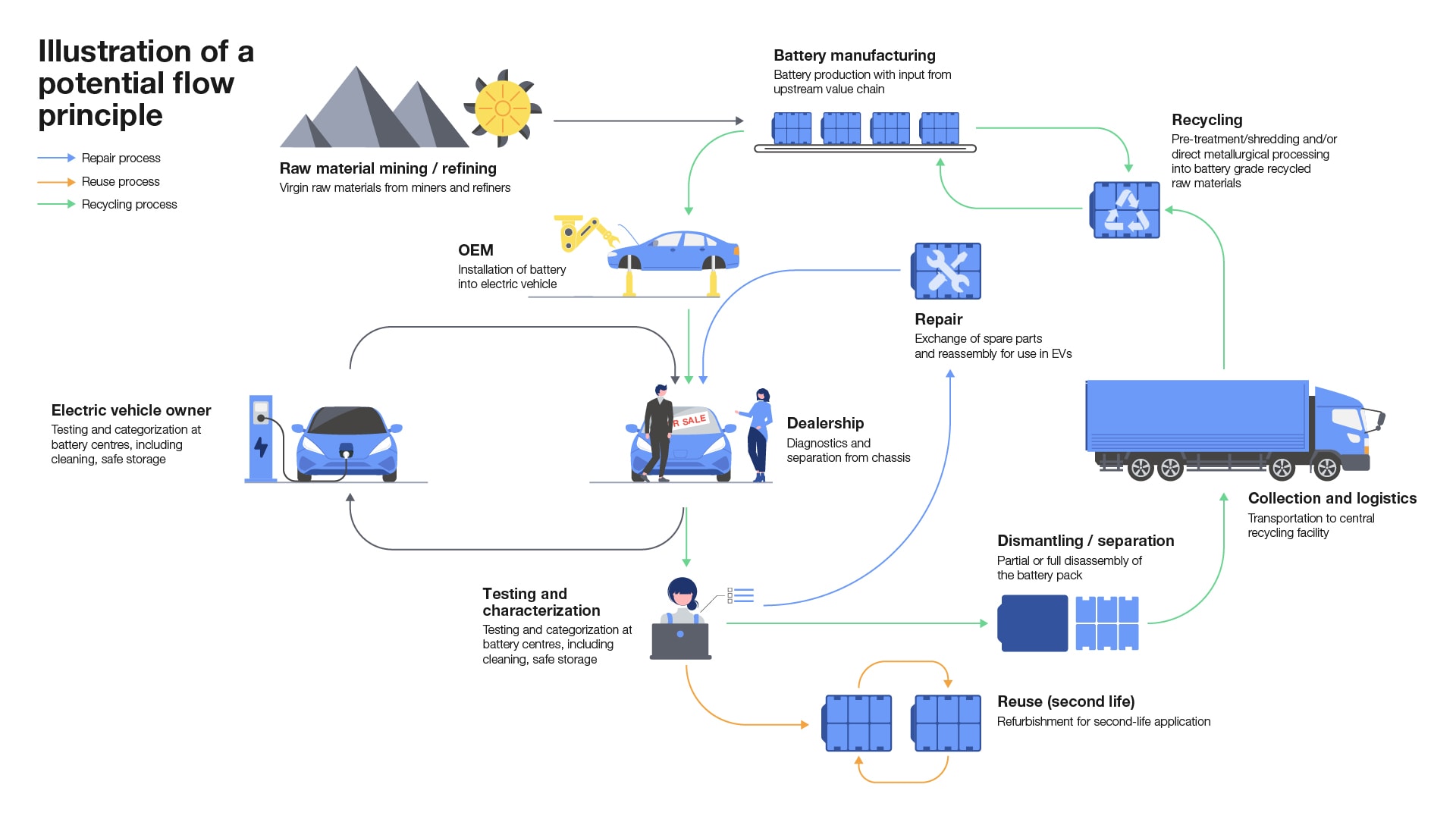
3. Standardize the process
Another significant challenge for EV battery circularity is the lack of a common set of standards to monitor the health of a battery, collect the hardware and handle reverse logistics – recapturing the value of a product at the end of its life cycle. Without common standards, each company is forced to develop individualized requirements, based on where batteries stop functioning. Subsequently, suppliers find synchronization of operations and services difficult. Batteries remain outside of the recycling loop.
For sustainable mobility products such as electric vehicles, end of life management is key. Circularity helps limit their environmental impact, and logistics play a key role in this process
”The is no doubt that a global circular economy approach to e-mobility needs to be harnessed by public and private stakeholders along the value chain. Through the Circular Cars Initiative, vehicle manufacturers, component suppliers and logistics companies have prioritized joint action for end-of-life battery management:
- Sharing learnings on expected EoL batteries distribution, returns and recycling.
- Exploring potential joint pooling as well as safe transport of end-of-life batteries through shared (regional) collection centres.
- Sharing learnings on how to categorize, disassemble, repair, and recycle batteries.
EVs are the future – and have the potential to drastically reduce global CO2 emissions through tail-pipe savings in the race to hit net zero. But this reduction will mean far less if the automotive industry, trying to meet the demand for batteries, still contributes heavily at the manufacturing end. By closing the loop with a circular EV battery value chain that analyzes materials, standardizes the process and delivers profit, e-mobility will be taking the fast lane to a low-carbon world.
• The Circular Cars Initiative is a community of stakeholders from across the automotive value chain that leverages circularity principles to minimize total life-cycle emissions, and to firmly ground the automotive sector within a 1.5°C scenario.
Don't miss any update on this topic
Create a free account and access your personalized content collection with our latest publications and analyses.
License and Republishing
World Economic Forum articles may be republished in accordance with the Creative Commons Attribution-NonCommercial-NoDerivatives 4.0 International Public License, and in accordance with our Terms of Use.
The views expressed in this article are those of the author alone and not the World Economic Forum.
Related topics:
Forum Stories newsletter
Bringing you weekly curated insights and analysis on the global issues that matter.
More on Emerging TechnologiesSee all
Elena Fersman
May 14, 2025
Rya G. Kuewor
May 13, 2025
Tea Trumbic and Dhivya O’Connor
May 13, 2025
Anurag Sinha
May 9, 2025
Jake Okechukwu Effoduh
May 7, 2025