The future of manufacturing: insights from industry leaders on navigating the Fourth Industrial Revolution
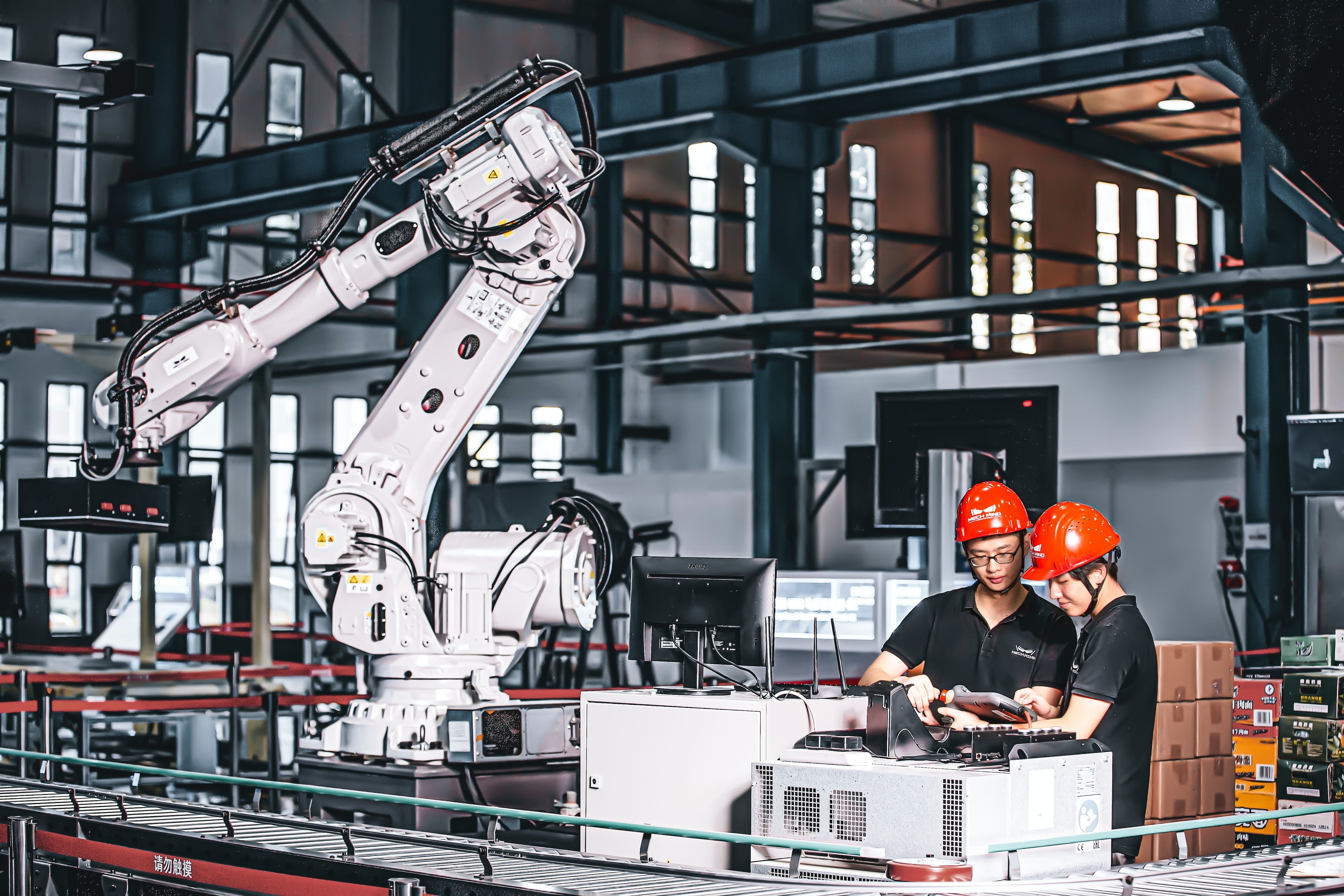
The manufacturing process is becoming increasingly high-tech
Image: Photo by Mech Mind on Unsplash
Listen to the article
- Technological advancements, climate change and geopolitical tensions have transformed the global manufacturing landscape.
- The Future of Manufacturing is a six-part video series profiling leading thinkers on the trends shaping advanced manufacturing.
- Here we pick out the series highlights from thought leaders in the manufacturing space.
Technological advancements, climate change and geopolitical tensions have transformed the global manufacturing landscape. The Future of Manufacturing is a six-part video series from the World Economic Forum where leading thinkers discuss the trends shaping advanced manufacturing. It explores key topics, such as frontier technologies, the workforce of the future, sustainable manufacturing and collaboration.
'Scale the adoption of technology in a way that works for all'
Francisco Betti, Head of Global Industries at the World Economic Forum
Accept our marketing cookies to access this content.
These cookies are currently disabled in your browser.
Francisco Betti, Head of Global Industries at the World Economic Forum, emphasises the need for closer collaboration between companies and governments in the face of manufacturing disruptions caused by geopolitics, climate change and the Fourth Industrial Revolution (4IR). Investing in reskilling, upskilling and making manufacturing more exciting for new generations is another priority for the global manufacturing community. “We need to make sure that we scale the adoption of technology in a way that works for all,” says Betti. To tackle some of the challenges facing manufacturing, the Global Lighthouse Network, an initiative by the World Economic Forum, brings together the most advanced manufacturing sites in the world to exchange knowledge and best practices to accelerate the deployment of 4IR technologies. By fostering collaboration, companies can collectively create a more inclusive and sustainable future for manufacturing.
'Manufacturing is about more than just data science'
Jay Lee, Clark Distinguished Professor and Director of Industrial AI Center at the University of Maryland
Accept our marketing cookies to access this content.
These cookies are currently disabled in your browser.
Jay Lee, Clark Distinguished Professor and Director of the Industrial AI Center at the University of Maryland, highlights the importance of bridging the gap between technology and actual implementation in manufacturing. He advocates for a clear purpose when adopting new technologies, addressing specific challenges and improving key areas, such as product quality, production efficiency and supplier integration. Academia is vital in testing and validating new technologies before implementation to ensure they meet industry standards. Purposeful innovation involves strategic planning, collaboration and continuous improvements to maximise the benefits of technological advancements in manufacturing.
'Industry is a big contributor to CO2 emissions worldwide'
Barbara Frei-Spreiter, Executive VP and CEO of Industrial Automation at Schneider Electric
Accept our marketing cookies to access this content.
These cookies are currently disabled in your browser.
Barbara Frei-Spreiter, Executive VP and CEO of Industrial Automation at Schneider Electric, recognizes the urgent need for sustainability in the manufacturing sector, given its significant contribution to global CO2 emissions. Decarbonisation efforts, including the electrification of processes, have already begun in heavy industries. However, Frei argues that more companies can reduce their carbon footprints and improve productivity by empowering employees, fostering cross-departmental collaboration, and implementing energy-saving programmes.
'It is about the human and automation interaction'
Kathy Wengel, Executive Vice President, Chief Technical Operations and Risk Officer at Johnson & Johnson
Accept our marketing cookies to access this content.
These cookies are currently disabled in your browser.
Kathy Wengel, Executive Vice President, Chief Technical Operations and Risk Officer at Johnson & Johnson, discusses the importance of engaging employees at all levels in technology selection and implementation. Wengel highlights the role of shop floor employees in bringing operational technology (OT) to improve and innovate manufacturing processes. Thoughtful choices in technology adoption are necessary to improve resilience, reduce risk and lower costs. Factory operators know the best flow across the organization, so their input and engagement in designing the technology are integral for successful deployment. Technology and customer needs continue pushing manufacturing to be better and Johnson & Johnson’s 10 Lighthouse designations (including one Sustainability Lighthouse) reflect the company's position as an industry leader. Wengel believes the ability to work together across governments, public-private partnerships and creating learning environments is crucial for the technical future of the manufacturing industry.
'It is important that governments ensure that workers have the right skills'
Jacqueline Poh, Managing Director of the Singapore Economic Development Board (EDB)
Jacqueline Poh, Managing Director of the Singapore Economic Development Board (EDB), highlights the importance of leveraging automation, artificial intelligence and technological advancements to enhance productivity and innovation in manufacturing. As technologies evolve rapidly, upskilling and reskilling programmes become essential to prepare employees with the necessary competencies. Collaborative efforts between industry, government and educational institutions can bridge the skills gap and ensure that the workforce is ready for the future of manufacturing. The World Economic Forum, in partnership with the Singapore Government and other stakeholders, has developed the Smart Industry Readiness Index (SIRI), a digital maturity benchmarking tool that enables enterprises of all sizes to assess their strengths, weaknesses and progress in embracing automation and technological advancements. Over 850 companies across 30 countries have already benefited from this initiative, which empowers them to improve their operations and contribute to the global community.
'Digital tools are the next level'
Katy George, Senior Partner and Chief People Officer at McKinsey & Company
Katy George, Senior Partner and Chief People Officer at McKinsey & Company, discusses how digital tools deployed at scale unlock new opportunities for manufacturing, allowing for real-time insights and optimisation across the entire enterprise and ecosystem. Integrating technologies such as artificial intelligence (AI) and automation improves cost-efficiency, reduces carbon footprints and improves supply chain resilience and diversification. By optimizing ecosystems, industries can achieve game-changing improvements, leading to economic inclusion and reshaping the concept of manufacturing jobs.
The manufacturing sector is undergoing a transformative journey in the Fourth Industrial Revolution. Through initiatives, such as the Global Lighthouse Network and the Smart Industry Readiness Index (SIRI), companies can benchmark their progress, foster collaboration and accelerate the deployment of 4IR technologies, ultimately transforming manufacturing into a main driver of economic growth, innovation and sustainability.
The Centre for Advanced Manufacturing and Supply Chains engages over 150 public and private sector leaders from the manufacturing and supply chains ecosystem to anticipate global trends, leverage pioneering technologies, unlock innovative business models and incubate new partnerships to drive economic, societal and environmental impact.
Contents
'Scale the adoption of technology in a way that works for all''Manufacturing is about more than just data science''Industry is a big contributor to CO2 emissions worldwide''It is about the human and automation interaction''It is important that governments ensure that workers have the right skills''Digital tools are the next level'More on Forum InstitutionalSee all
World Economic Forum
June 26, 2025
Pooja Chhabria and Gayle Markovitz
June 25, 2025
Pooja Chhabria and Gayle Markovitz
June 24, 2025
Pooja Chhabria and Gayle Markovitz
June 23, 2025
Pooja Chhabria and Christina Schunck
June 10, 2025
World Economic Forum
May 16, 2025