6 ways to unleash the power of AI in manufacturing
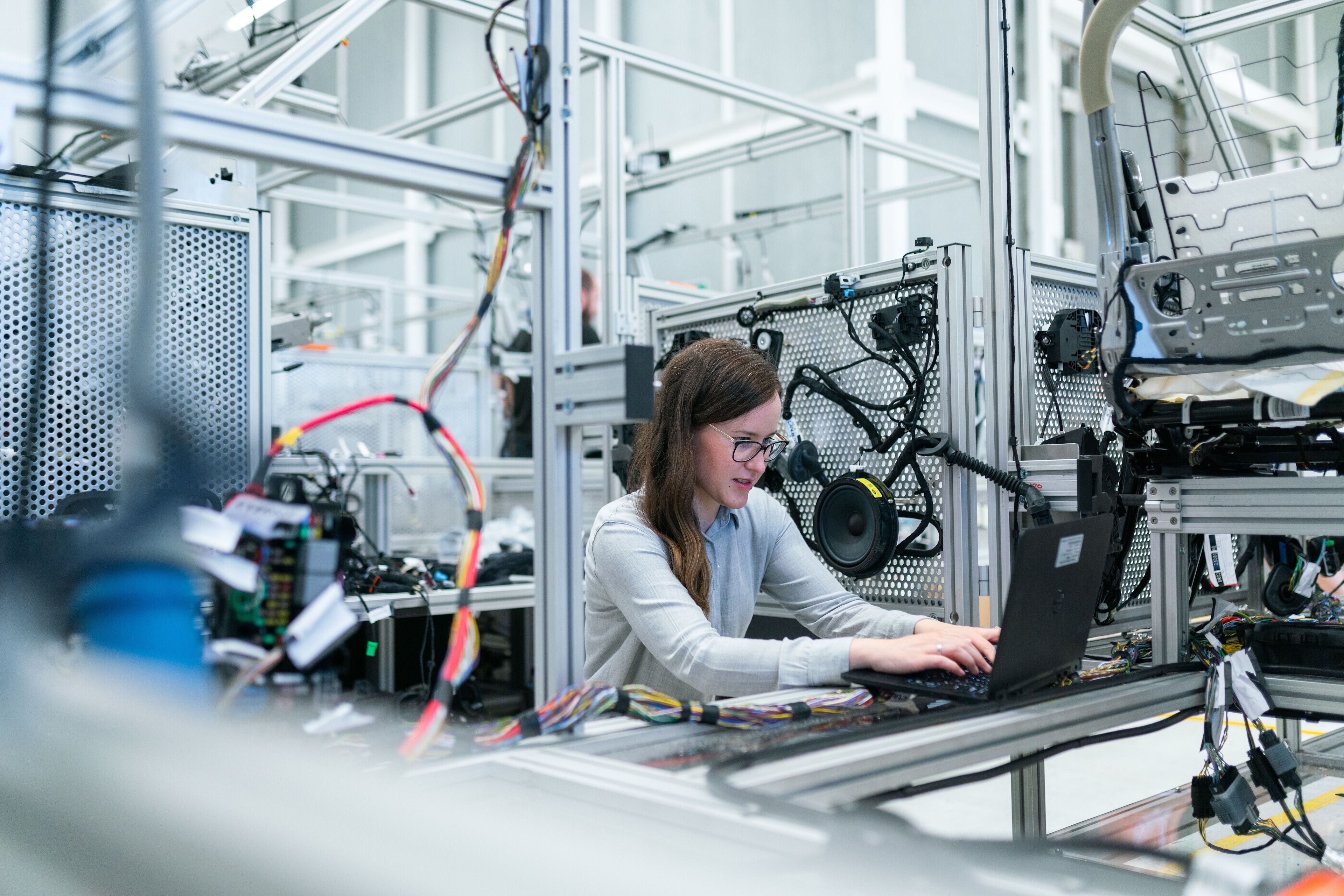
The global AI in manufacturing market is valued at $3.2 billion in 2023 and is poised to grow to $20.8 billion by 2028.
Image: Photo by ThisisEngineering RAEng on Unsplash
Jasmeet Singh
Executive Vice President, Global Head of Manufacturing and Chair Infosys Public Services and Infosys Automotive GmbH, InfosysStay up to date:
Tech and Innovation
- The global AI in manufacturing market is valued at $3.2 billion in 2023 and is poised to grow to $20.8 billion by 2028.
- Yet, despite these possibilities and significant investments, manufacturers are not harnessing the full potential of AI.
- Once manufacturers address the key challenges in AI deployment, they can transform every aspect of their business for the better.
The synergies between artificial intelligence (AI) technologies and manufacturing are well known. Among the earliest adopters of computer-based tech in the 1970s, the manufacturing industry has grown into an AI-heavyweight in the 21st century.
There is no doubt that manufacturers are making huge commitments to AI. According to estimates, the global AI in manufacturing market was valued at $3.2 billion in 2023 and is poised to grow to $20.8 billion by 2028.
This is no surprise. Manufacturers clearly recognize the pivotal role of AI in their journey to Industry 4.0 and the creation of highly efficient, connected and smart manufacturing operations.
While there is no limit to AI applications in manufacturing, below are some of the most exciting use cases:
1. Safe, productive and efficient operations
After using robots for decades, manufacturers are starting to deploy 'cobots' on their shop floors. While traditional robots must be housed separately, cobots work safely alongside humans, picking parts, operating machinery, performing various operations and even conducting quality inspections to improve overall productivity and efficiency. Being highly versatile, cobots can perform various tasks, from glueing, welding and greasing automotive parts to picking and packaging manufactured products. AI-driven machine vision plays a key role in making this happen.
2. Intelligent, autonomous supply chains
With the help of AI, machine learning (ML) and Big Data analytics, manufacturers can achieve autonomous planning – continuous, closed-loop, fully automated planning – to maintain supply-chain performance even in volatile conditions, with little human oversight. Industrial companies can also use AI agents to schedule complex manufacturing lines. The agents can consider a variety of parameters to come up with the best way to maximize throughput at minimal changeover cost to deliver products on time.
3. Proactive, predictive maintenance
Using AI to monitor and analyze data from machinery and shop floor processes, manufacturers can identify anomalous patterns to predict or even prevent breakdowns. For example, AI can process vibration, thermal imaging and oil analysis data to assess the health of machinery. The insights from AI also enable manufacturers to provision spare parts and consumables correctly and accurately predict the downtime that will affect production planning and related activities. The result is improvement in productivity, cost efficiency and equipment health. Generative AI can add further value by scanning documents, such as maintenance logs and inspection manuals, to provide actionable, precise information to execute troubleshooting and maintenance activities.
4. Automate quality checks
AI is a game changer in testing and quality control. Image recognition can be used to detect equipment damage and product defects automatically. For example, AI models trained using images of good and defective products can predict if an item may require rework or needs to be scrapped or recycled. In addition, AI’s analytical capabilities can be leveraged to identify patterns in production data, incident reports, customer complaints, etc., to uncover improvement areas.
5. Design, develop, customize and innovate products
Generative AI can transform product conceptualization by analyzing market trends, highlighting changes in regulatory compliance, summarizing product research and customer feedback, etc. Based on these insights, product designers can innovate and improve products and ensure compliance by comparing specifications against the relevant standards and regulations.
The algorithms can quickly generate innovative designs beyond the capability of traditional methods. This means manufacturers can optimize the product attributes most important to them – safety, performance, aesthetics or even profitability. For example, in 2019, General Motors used generative design to prototype a lighter, stronger seat bracket for its electric vehicles. Further, by using AI solutions and simulation software, manufacturers can develop, test and refine product designs without needing to build physical prototypes; this lowers development time and costs and increases product performance.
6. Empowering employees
By automating tedious, time-consuming tasks, AI enables manufacturing workers to focus on more creative or sophisticated activities. AI can also recommend next-best actions so employees can be more efficient and effective. Unlike the robots of yesteryears, modern AI solutions, integrated with sensors and wearable technology, can warn factory personnel about any hazards on the shop floor.
Accept our marketing cookies to access this content.
These cookies are currently disabled in your browser.
Crossing the data barrier for using AI in manufacturing
Despite these possibilities and big investments, manufacturers are unable to secure the full benefit of AI.
In a survey of 3,000 organizations from various industries and geographies, just 10% said they were extracting significant financial gains from AI. This coheres with the findings of the Infosys Generative AI Radar – North America survey, where about 30% of large companies ($10 billion+) but fewer than 10% of companies earning between $500 million and $10 billion had established generative AI use cases that were yielding business value.
While manufacturers recognize the importance of embedding AI in their business processes, they are disheartened by the results.
The World Economic Forum’s December 2022 white paper titled, Unlocking Value from Artificial Intelligence in Manufacturing, identifies six barriers to AI adoption in manufacturing, ranging from a mismatch between AI capabilities and operational needs to a lack of explainable AI models to the significant customization required across manufacturing use cases.
AI algorithms need to be trained on massive datasets of clean, accurate and unbiased data to work properly. Since providing this can be a challenge for manufacturers, many companies resort to small, fragmented, inconsistent or poor-quality data, resulting in suboptimal outcomes. Even when large data is available, it may not be readily consumable by AI models.
Hence, before feeding training data to AI, manufacturers need to ensure it is harmonized so that everyone in the organization – across functions, business units and geographies – is able to access all the data they need in the same consolidated format. The data should also be staged so AI-enabled software can generate on-demand insights personalized for users, such as factory managers, quality inspectors, top management, etc.
The good news is that once manufacturers address the key challenges in AI deployment, they can transform every aspect of their business for a wide range of benefits.
Accept our marketing cookies to access this content.
These cookies are currently disabled in your browser.
Don't miss any update on this topic
Create a free account and access your personalized content collection with our latest publications and analyses.
License and Republishing
World Economic Forum articles may be republished in accordance with the Creative Commons Attribution-NonCommercial-NoDerivatives 4.0 International Public License, and in accordance with our Terms of Use.
The views expressed in this article are those of the author alone and not the World Economic Forum.
Related topics:
Forum Stories newsletter
Bringing you weekly curated insights and analysis on the global issues that matter.
More on Manufacturing and Value ChainsSee all
Michael Donatti and Laura Fisher
July 3, 2025
Kaiser Kuo
June 26, 2025
Leo Simonovich and Filipe Beato
June 18, 2025