How to introduce new technology into US manufacturing, from a worker's perspective
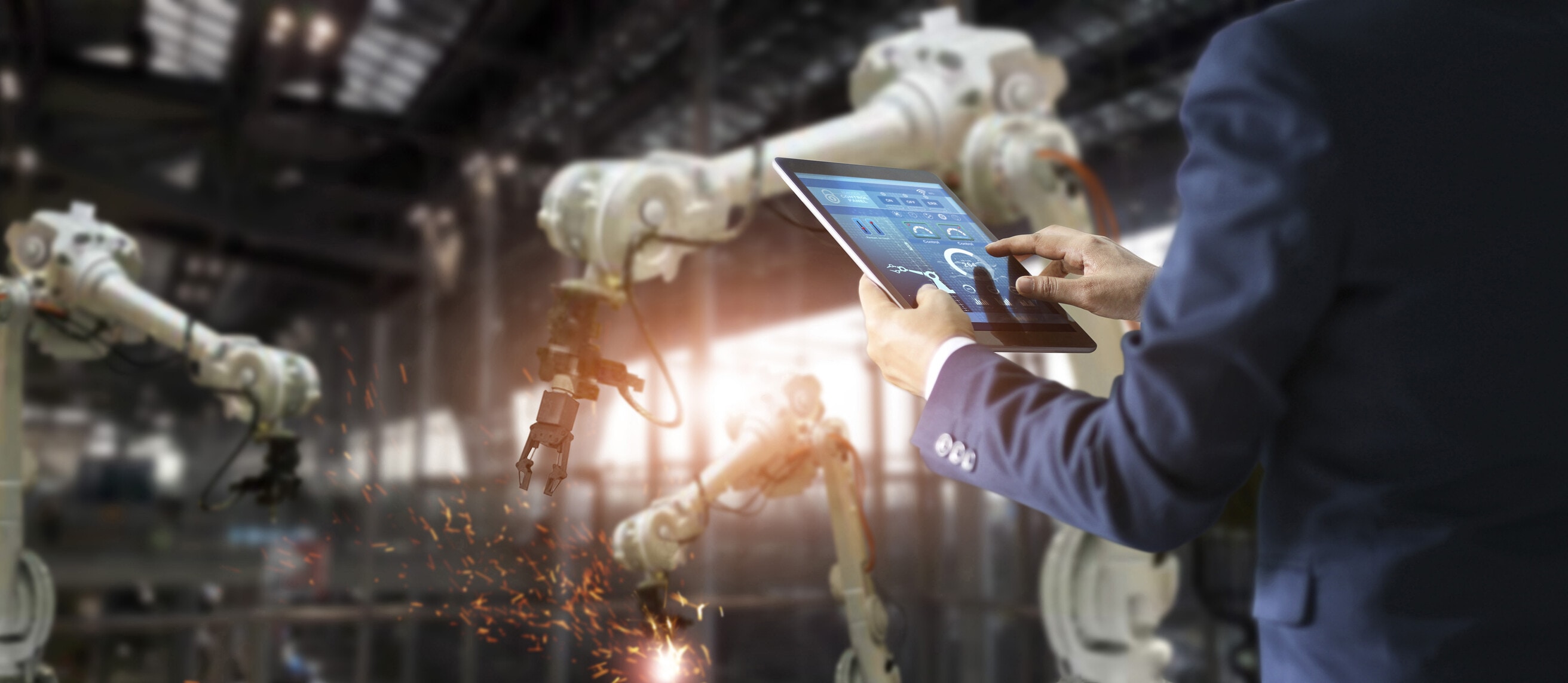
New technologies could help the US manufacturing sector recruit and retain staff.
Image: Getty Images/iStockphoto
Kyle Winters
Initiatives and Communities Lead, Advanced Manufacturing and Value Chains, World Economic ForumStay up to date:
Advanced Manufacturing
- The US is a world leader and innovator in manufacturing, spearheading research and development with a 28% of global spending.
- But the US manufacturing sector is facing joint challenges of unfilled roles and a struggle to attract and retain experienced employees.
- The World Economic Forum and the US Center for Advanced Manufacturing outline a shop floor workers' perspective on how to ensure new technology is introduced in a human-centric and effective way.
In the ever-evolving landscape of global competitiveness, the US stands as a pivotal force and innovator in manufacturing, spearheading research and development with a staggering 28% share of global spending.
However, a pressing challenge looms over the sector – 55% of manufacturing roles remain vacant, compounded by a persistent struggle to attract and retain manufacturing employees, identified as a top challenge by 71% of manufacturers for the sixth consecutive year.
Recognizing the immediate need to address this workforce crisis, the US Center for Advanced Manufacturing expanded upon the World Economic Forum’s Centre for Advanced Manufacturing and Supply Chains’ global effort on the 'Views from the Manufacturing Front Line: Workers’ Insights on How to Introduce New Technology’ report.
As outlined in this report, fully automated operations are rarely feasible or the most efficient processes, making humans an essential differentiating factor in manufacturing. But without mastering the art of successfully introducing technologies to the shop floor, companies risk failing to keep up with innovation and falling behind their global competitors.
So taking into account the views of workers on the ground, the US Center delved into the priorities and best practices for workforce engagement in the digital transformation that are most relevant to the US context.
A shop floor workers' view on digitalizing manufacturing
Drawing from more than 40 interviews with shop floor operators on successful practices of adoption and introduction of emerging technology in daily operations across five industry sectors in New York, Pennsylvania, Michigan and Texas, the Center identified five key practices that are instrumental for US executives to ensure technology introductions are designed in a sustainable, human-centric and effective way. These five practices are:
1. Demystifying efficiency tracking
The introduction of new technologies particularly for efficiency, tracking or documentation purposes has put increased pressure on operators and introduced a fear of errors. Authentic communication and encouraging a two-way dialogue that resonates with employees can help proactively manage expectations, demystify the learning journey and alleviate concerns associated with technology change.
2. Introducing a ‘live my life’ format
The “live my life” format involves management spending intentional time on the shop floor, interacting and performing tasks with shopfloor operators. This can spur innovative problem-solving by creating visibility into how operators’ experiences, lessons learnt and best practices interacting with new technologies vary.
In addition, extending this opportunity to operators allows for cross-pollination of nuances such as personal experiences, individual best practices and lessons learned during a new technology introduction. In the US context, this has been highlighted as particularly helpful for visibility between different shifts, such as night-shift operators who often have less engineer and supervisory support.
3. Cultivating small group interactions
Building on the importance of catering for different learning styles, which includes accounting for a range of linguistic needs, different levels of abilities and learning styles, US operators indicated a preference for smaller group settings when it comes to training on new technologies, capped at 20 employees.
4. Establishing cross-mentoring programmes
With a maturing US workforce, identifying technology champions or “super users” is particularly relevant for successful technology adoption. Pairing super users with employees from different generations and levels of seniority in cross-mentoring programmes aids in the exchange of both new technology-based skills and legacy information learned on the shop floor.
5. Offering continuous learning opportunities
Embracing technological transformations necessitates an unwavering commitment to continuous skill enhancement. Encouraging and building in time for employees to take advantage of learning opportunities that further their development benefits creativity and innovation among an agile workforce.
How is the World Economic Forum contributing to build resilient supply chains?
Both employer-sponsored and non-employer-sponsored certificate and degree programmes are helpful in creating a continuous learning culture that empowers employees to invest time in acquiring complementary skills.
The way forward for US manufacturing
With manufacturing turnover and absenteeism rates averaging 40%, the US Center for Advanced Manufacturing remains committed to the continuation of addressing attracting and retaining workers and invites stakeholders from industry, policy and academia across the US to join their effort.
In this context, the Center’s Upskilling the US Workforce Program is running a series of how-to workshops and articles highlighting best practices in attracting and retaining talent across five key demographic pillars:
- Current culture: An organization’s current workforce and how they are adapting to technological change, and continually learning.
- K-12: Students exposed to manufacturing at kindergarten through high school level, focusing on changing negative perceptions of a career in manufacturing.
- Alternative pathways: Those who receive a manufacturing education through non-traditional four-year university degree programmes, such as apprenticeship schemes.
- Traditional pathways: Those with four-year university degree programme including higher education such as master's degrees and PhDs that enter the manufacturing workforce.
- Under-represented: Expanding manufacturing workforce opportunities for minority groups, individuals with disabilities, veterans, re-entering citizens, women, 55+, low-income, and LGBTQ(+) individuals and groups.
Accept our marketing cookies to access this content.
These cookies are currently disabled in your browser.
In addition, the US Center for Advanced Manufacturing will also continue to play a crucial role in uncovering new insights on local workforce transformation principles and priorities.
It does this by bringing together key stakeholders across the US manufacturing landscape and further collaborating with the World Economic Forum’s Centre for Advanced Manufacturing and Supply Chains to inform the global agenda.
Launched in October of 2022 in collaboration with the World Economic Forum, the US Center for Advanced Manufacturing is a public-private partnering platform committed to accelerating the growth of manufacturing in the US.
The Center's mission is rooted in driving state, regional and national initiatives aimed at of generating new insights and collaborations that can fortify US manufacturing, making it more innovative, sustainable and inclusive.
As part of the World Economic Forum’s Centre for the Fourth Industrial Revolution Network, the US Center draws on global insights to ensure its activities are aligned with the latest trends observed around the world as well as sheds light on US capabilities and priorities to shape the global manufacturing agenda.
Don't miss any update on this topic
Create a free account and access your personalized content collection with our latest publications and analyses.
License and Republishing
World Economic Forum articles may be republished in accordance with the Creative Commons Attribution-NonCommercial-NoDerivatives 4.0 International Public License, and in accordance with our Terms of Use.
The views expressed in this article are those of the author alone and not the World Economic Forum.
Related topics:
Forum Stories newsletter
Bringing you weekly curated insights and analysis on the global issues that matter.
More on Manufacturing and Value ChainsSee all
Adegboyega Oyedijo and Temidayo Akenroye
April 18, 2025
Kiva Allgood and Sue Ellspermann
April 9, 2025
Ulrich Scherbel
April 1, 2025