Modernizing ageing factories: The role of digital transformation in enhancing brownfield manufacturing
Image: Jubilant Ingrevia
- Over the past decade, companies across industries have harnessed digital technologies to transform and enhance efficiency and productivity.
- However, its penetration in brownfield manufacturing remains limited.
- Digitizing these ageing sites has the potential to create immense impact across business lines, as well as on social and environmental levels.
Studies have found that over 80% of companies around the world have launched digital transformation initiatives. While other industries are undergoing rapid digital transformation, the implementation of digital interventions in the manufacturing sector has had less momentum. In fact, McKinsey & Company reports that only 30% of manufacturing companies have effectively realized value at scale through Industry 4.0 practices across all their plants.
The adoption rate is even lower for brownfield manufacturing - plants which rely on existing facilities or legacy infrastructure. This is especially the case in the Asia Pacific region.
Digital penetration in brownfield manufacturing remains low due to several factors:
- Digital interventions are costly. The significant investment required for digitization often leaves organizations in 'pilot purgatory' where most projects fail to progress beyond the pilot stage.
- In brownfield manufacturing, legacy equipment and ageing infrastructure pose substantial barriers to digital solutions.
- Manufacturing plants frequently operate in data silos. Over time, these plants have accumulated data in isolated pockets, hindering a comprehensive view of operations.
Digital transformation in brownfield manufacturing can positively impact businesses, the environment and society
Brownfield manufacturing businesses can benefit immensely from digital interventions and can enhance efficiencies, further environmental sustainability, and ensure a positive societal impact.
- Efficiency: Digitization could lead to higher throughput and yields. For example, the Jubilant Ingrevia's Acetic Anhydride plant in Bharuch, Gujarat, India, implemented predictive models and advanced analytics to achieve higher yields. This has supported the organization's ability to capture over 20% of the global market share.
- Environmental benefits: By optimizing processes and improving resource allocation, digital technologies can significantly reduce carbon emissions. At Jubilant Ingrevia, downstream processes accounted for 70% of energy consumption and nearly 8% of total cost. By leveraging Internet of Things (IoT) solutions including deploying 120 sensors and 4 technologies, steam consumption was reduced by 20%. Similarly, scope-1 emissions were reduced by 20% and liquid waste by 100%.
- Societal impact: Digital technologies can monitor working conditions in real-time, predict potential hazards, and plan for preventive measures. This ensures a safer working environment. Technologies also make the manufacturing sector more attractive to skilled workers. At Jubilant Ingrevia, incidents are being pre-empted by workers through a digital platform which enables proactive submissions of potential hazards and near-misses.
A case study of the Jubilant Ingrevia's Acetic Anhydride Plant
Acetic Anhydride is a highly controlled chemical with stringent measures due to its potential use in narcotics. It has diverse applications in industries like pharmaceuticals, agriculture, personal and consumer goods and defense. Jubilant Ingrevia operates Asia's largest Acetic Anhydride production facility with the world's largest merchant capacity. The plant manages complex chemical processes at scale with less than 40 full-time employees.
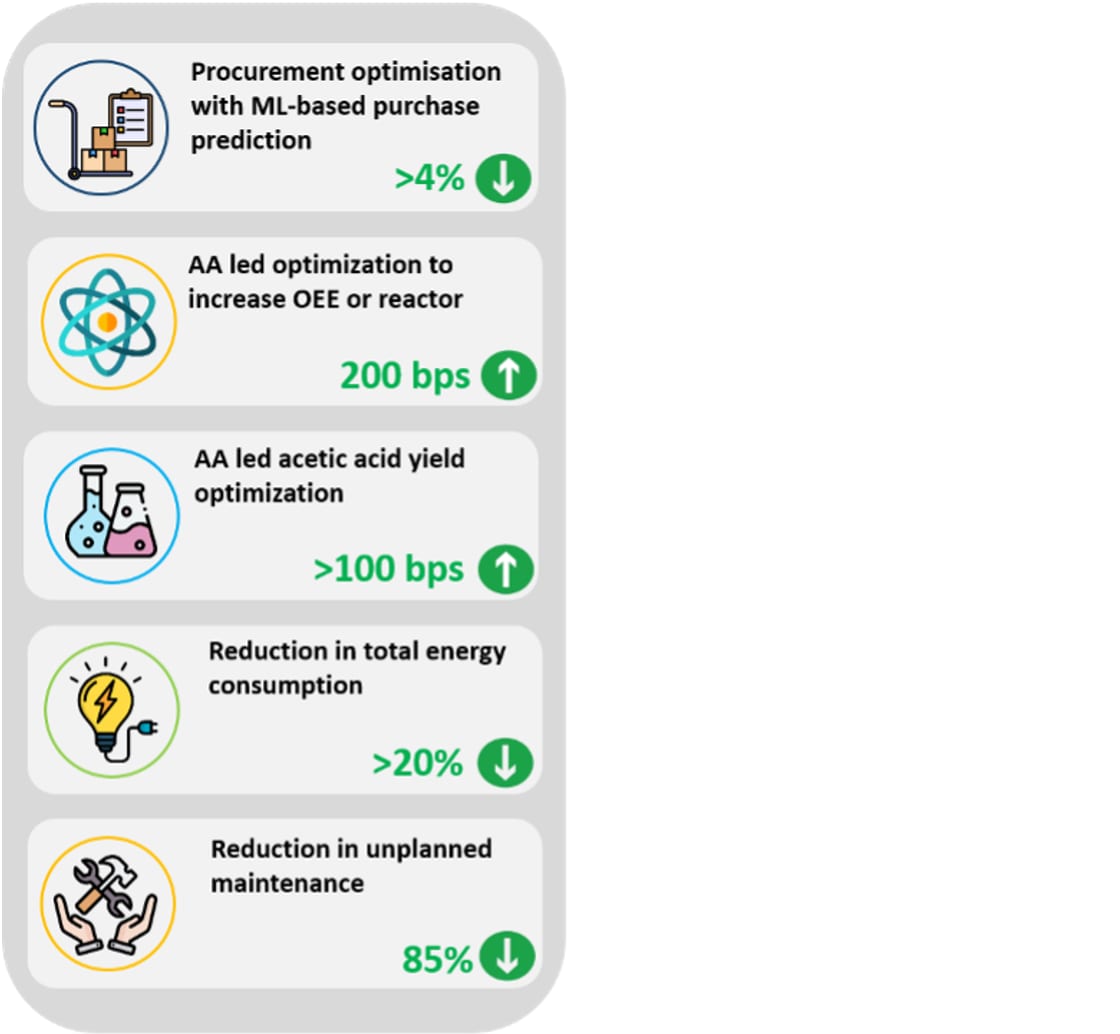
How is the World Economic Forum contributing to build resilient supply chains?
Toward digital transformation
Although digital transformation has always been integral to Jubilant Ingrevia's overall strategy, the push for digital advancement at the Acetic Anhydride plant was driven by the product's dominant market share in India and its keenness to grow its global market share. Aiming to enhance Jubilant Ingrevia's global market share through cost and quality leadership, the plant and digital teams identified critical digital interventions across the value chain.
Procurement interventions: Given the significant impact of product pricing on market share, efforts were focused on cost reduction. Optimization was essential with raw acetic acid accounting for over 80% of the total product cost. An advanced analytics model, utilising techniques such as VAR, XG Boost, and Mixed Integer Linear Programming, was developed to predict prices with over 95% accuracy for the next eight weeks. These data-driven predictions now guide pricing and quantity decisions, resulting in substantial raw material cost reductions.
Yield improvement: Plant teams employed machine learning models to establish 'Golden Batch' operating ranges, maximizing yield. Ten real-time soft sensors were deployed for quality parameters, reducing lab dependency and boosting overall productivity. Deviation alerts via digital performance management dashboards for out-of-control parameters and iterative model fine-tuning led to significant yield improvement and a reduction in process variability of over 60%. Additionally, 12 smart sensors were installed in the reactor section, and analytical models were developed using a cloud-based digital twin platform. This increased reactor uptime through preventive actions and decreased unplanned downtime due to coil leakage.
Energy consumption: Steam consumption was optimized which reduced costs, lowered Scope 1 emissions, and eliminated unwanted liquid waste generation. IoT-based real-time visibility and trend reversal analyses, utilising over 120 critical parameters, were crucial in achieving these benefits. Predictive maintenance based on radial and axial vibration, temperature, acoustic analysis, leakage identification, and equipment health analysis was implemented for critical equipment. Early warnings from the model and accurate root cause identification helped maintain equipment availability.
What was the impact?
The combined efforts led to significant growth in global market share, notably enhancing Jubilant Ingrevia's performance in European markets. Additionally, manufacturing efficiency improved dramatically, reducing production losses by over 30% and increasing workforce productivity by over 20%.
Conclusion
Digital transformation requires several systemic enablers. These include top-down vision and sponsorship from management to drive change, which can be achieved through clear communication and appropriate allocation of resources.
Management must set clear objectives, define goals, have a roadmap for success, and appropriate use cases. This would include deploying the best cross-functioning teams with multidisciplinary skills and should promote, specifically, the participation of the shop floor teams. Objectives for digitization can include revenue growth targets and cost reduction goals. Here, companies can hire digital talent which would include data scientists, UX designers and DevOps engineers. It is important to identify skills gaps and align new hires to overall digital objectives.
As the company navigates this transition, it should adopt agile processes and governance to ensure adaptability. This can include Kanban or Scrum models for development.
Finally, the company must foster a digital culture and ensure a mindset change among workers. Here, regular town halls and awareness sessions may help. This can be boosted through continuous communication, rewards and recognition for digital adoption, and creating change champions among workers.
Digital transformation of brownfield assets is imperative for economic, societal, and environmental prosperity. Although the challenges are significant — ranging from higher costs and outdated infrastructure to data privacy concerns — it is still achievable.
Our plant in Bharuch, Gujarat, serves as a testament to this possibility, demonstrating success despite the old and commodity nature of the product.
Don't miss any update on this topic
Create a free account and access your personalized content collection with our latest publications and analyses.
License and Republishing
World Economic Forum articles may be republished in accordance with the Creative Commons Attribution-NonCommercial-NoDerivatives 4.0 International Public License, and in accordance with our Terms of Use.
The views expressed in this article are those of the author alone and not the World Economic Forum.
Forum Stories newsletter
Bringing you weekly curated insights and analysis on the global issues that matter.
More on Manufacturing and Value ChainsSee all
Leo Simonovich and Filipe Beato
June 18, 2025
Benedikt Gieger and Isabell Steidel
June 12, 2025