Putting people first: a new imperative for manufacturing
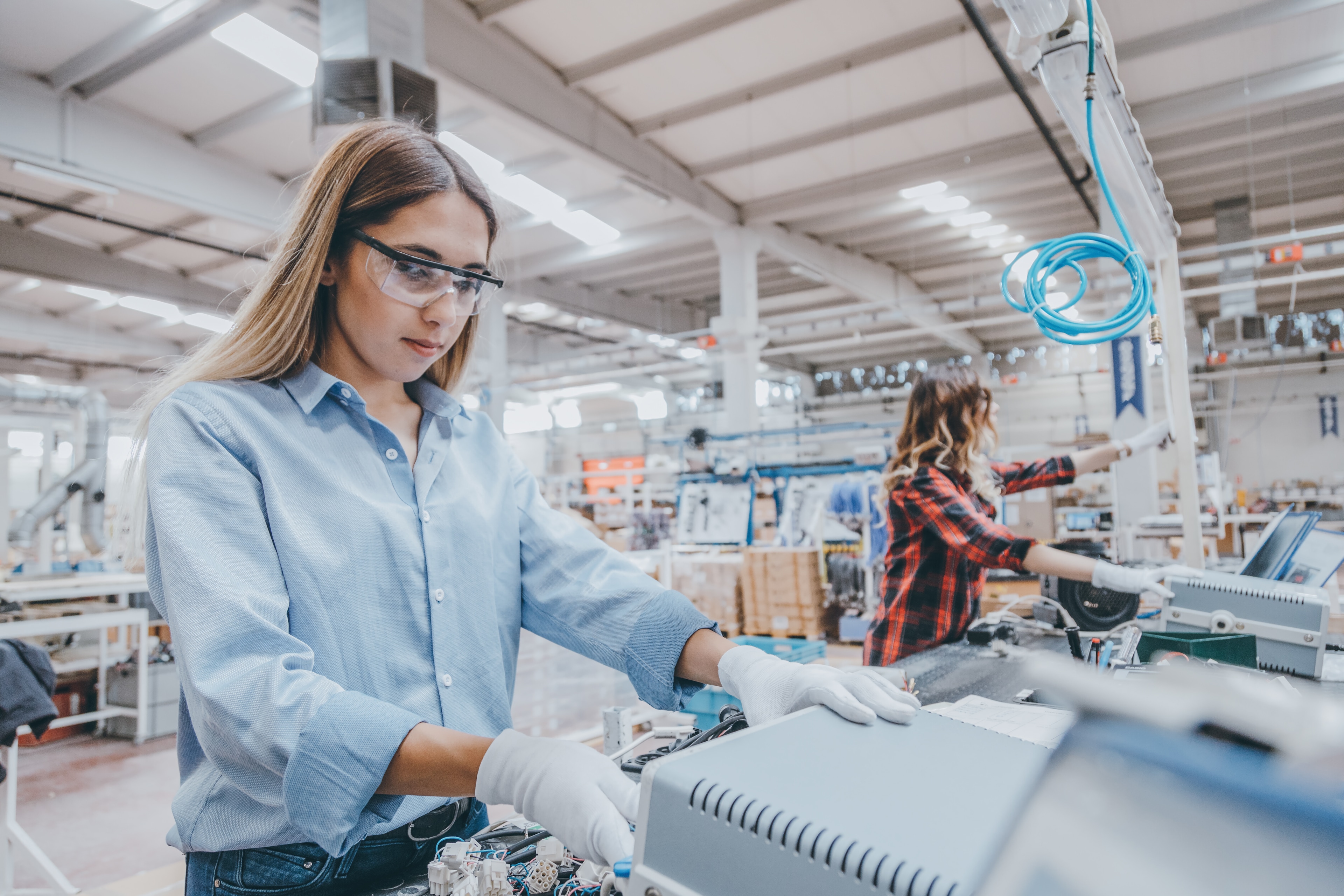
The manufacturing production ecosystem needs a new playbook for talent.
Image: Getty Images
Kiva Allgood
Head, Centre for Advanced Manufacturing & Supply Chains, Member, Exec. Committee, World Economic ForumStay up to date:
Advanced Manufacturing
- Workforce talent is a major barrier to successfully implementing digital transformation of manufacturing sites.
- High employee turnover remains a particular challenge in maintaining the frontline talent stability needed.
- To learn more about how leading companies are investing in talent, see the attached presentation here.
The World Economic Forum's Future of Jobs report highlights that over 50% of leaders cite skills gaps and talent attraction as major barriers to transformation. While executives in manufacturing and supply chain understand the need for a skilled workforce, they often struggle to find, retain and engage the talent they need. The production system needs a new playbook for talent – that draws on learnings and best practices from sites who are performing at the highest levels. To address this, the World Economic Forum in collaboration with McKinsey launched the Frontline Talent of the Future initiative in 2023 to identify and share successful talent innovations from leading industrial sites.
Just over one year later, the Frontline Talent of the Future Initiative has conducted 80+ interviews with industry leaders and completed numerous site visits across the globe, to assemble a database of 61 innovative talent solutions, and build a playbook for frontline talent excellence.
Now this initiative is joining forces with the Global Lighthouse Network (GLN), founded in 2018 in collaboration with McKinsey, and led by a coalition of industry partners that identify the world’s leading sites for their exceptional performance in productivity, supply chain resilience, customer centricity, sustainability and talent. The 172 members and counting represent the frontier of holistic performance across sites, production networks and value chains.
These Lighthouses have seen impressive outcomes such as 50% productivity improvements, 80%+ quality improvements, 40% lead time reductions, and 30% emissions reductions. They have illuminated the path to innovating with impact through technology, talent and sustainability solutions. Why aren’t more companies following suit? One of the main issues companies face today is talent. In 2025, the GLN will deepen its focus on talent by including additional talent-related achievements and solutions into its framework. This means, starting in 2025, sites can apply to be recognized for achieving world-class performance with distinction in talent transformation.
Accept our marketing cookies to access this content.
These cookies are currently disabled in your browser.
Today’s talent puzzle
Despite the many advancements brought by the Fourth Industrial Revolution (4IR), companies continue to face challenges achieving productivity growth, driven in part by a lack of workforce stability. A recent US report found that 71% of manufacturers cited the inability to attract and retain employees as their primary challenge. Attrition, especially among those hired in the last 90 days, remains stubbornly high. Across advanced economies, productivity growth in units per hour has slowed to an average of 1% percent between 2016-2022, compared to 2.2% between 1997-2002.
It has never been harder to attract, retain and engage workers than it is today. These combined challenges emerge from five root causes:
1. Talent shortages
The demand for frontline workers is outpacing availability. In January 2024, the US Bureau of Labor Statistics reported 622,000 unfilled manufacturing job openings nationwide, while the overall labour force participation rate fell from 67% in the 1990s to below 63% in 2023.
2. Widening skill gaps
Technical skills are lagging behind the pace of investment in digital and automation. Approximately 15% of workers are reporting some degree of skills mismatch across manufacturing industries. This reality echoes the World Economic Forum’s 2023 Future of Jobs report, which predicted that 44% of workers’ skills would be disrupted in the following five years.
3. Insufficient rewards, recognition and incentives
McKinsey & Company analysis found 41% of workers feel they have inadequate total compensation, driving attrition and workplace switching.
4. Struggling supervisors
Supervisors often lack soft skills and are spending less than one-third of their time on people.
5. Evolving worker needs
Today’s frontline employees want a discernible career path, respond to inspiring leaders, value meaningful work, and seek more scheduling flexibility. However, according to McKinsey research, there is a mismatch between what employers believe employees’ top needs are and what employees say they are.
Six talent capabilities for growth
Historically, business leaders have viewed the workforce as a cost centre. However, companies that create the most value are those that focus on driving capital and labour productivity in tandem. They do this by thinking of their talent as an investment, in the same way they think of capital.
The Frontline Talent of the Future initiative partnered with nine companies to develop a comprehensive assessment process to identify examples of successful frontline talent investments.
The pilot revealed that companies are investing in talent across six capabilities. When companies couple these investments with compensation packages appropriate for their industry and location, they see productivity and stability improvements that greatly outpace their peers. The following are just a few examples of innovations we have seen across the six capabilities; for more detail, please see the attached presentation.
1. Work design and safety
Reimagining frontline work to create safe and productive workspaces and processes:
- Western Digital’s Prachin Buri site uses a digital control room to transform their factory and move operators into higher skilled roles.
- Unilever’s Kilbourn site implements agile and continuous organizational restructuring to create career development opportunities that are individually tailored to the talent they have.
2. Talent planning
Understanding the organization and site-level needs for frontline talent; match demand and supply through dynamic scheduling:
- Haier COSMOPlat’s dynamic line-balancing tool creates opportunities for scheduling flexibility.
- Schneider Electric’s competency management system enables smart talent planning at their site in India.
3. Attraction and onboarding
Finding and activating the next generation of frontline talent:
- Flex’s Althofen site offers an apprenticeship programme creating a pipeline for young talent.
- Aramco uses AI matching to optimize their hiring process by improving quality and speed of employee screening.
4. Development
Building distinctive frontline capabilities for operators and supervisors:
- Western Digital in Thailand created their own digital leadership essentials programme in partnership with universities.
- Aramco implements virtual reality and gamified training to increase training effectiveness.
5. Talent effectiveness
Managing performance for operators and supervisors in a way that drives the right behaviours to achieve performance aspirations:
- Unilever’s Kilbourn site implements creative performance-based rewards that enable open dialogue between employees and leadership.
- Haier COSMOPlat deploys an innovative approach to salary accounting.
6. Culture and experience
Defining and delivering a compelling employee value proposition:
- Nestlé’s Garoto chocolate factory creates an inclusive environment for deaf and hard of hearing employees.
- Haier COSMOPlat implements a social platform to engage employees in innovation.
If you believe you have achieved world-class performance through talent transformation, we encourage your application to the Global Lighthouse Network at: initiatives.weforum.org/global-lighthouse-network/home. Applications are open from 9 December to 2 February.
Thank you to our pilot participants: Aramco, Coca-Cola, Flex, First Solar, Fortune Brands, Haier COSMOPlat, Nestlé, Schneider Electric, Unilever, Western Digital
Don't miss any update on this topic
Create a free account and access your personalized content collection with our latest publications and analyses.
License and Republishing
World Economic Forum articles may be republished in accordance with the Creative Commons Attribution-NonCommercial-NoDerivatives 4.0 International Public License, and in accordance with our Terms of Use.
The views expressed in this article are those of the author alone and not the World Economic Forum.
Related topics:
Forum Stories newsletter
Bringing you weekly curated insights and analysis on the global issues that matter.
More on Manufacturing and Value ChainsSee all
Nii Simmonds and Nii Ahele Nunoo
March 6, 2025
Benedikt Gieger and Dominik Metzger
March 3, 2025
César Dugast and Ana Luiza Sanches
March 3, 2025
John Ferguson and Melanie Noronha
February 21, 2025