Should robotic design follow these three laws?
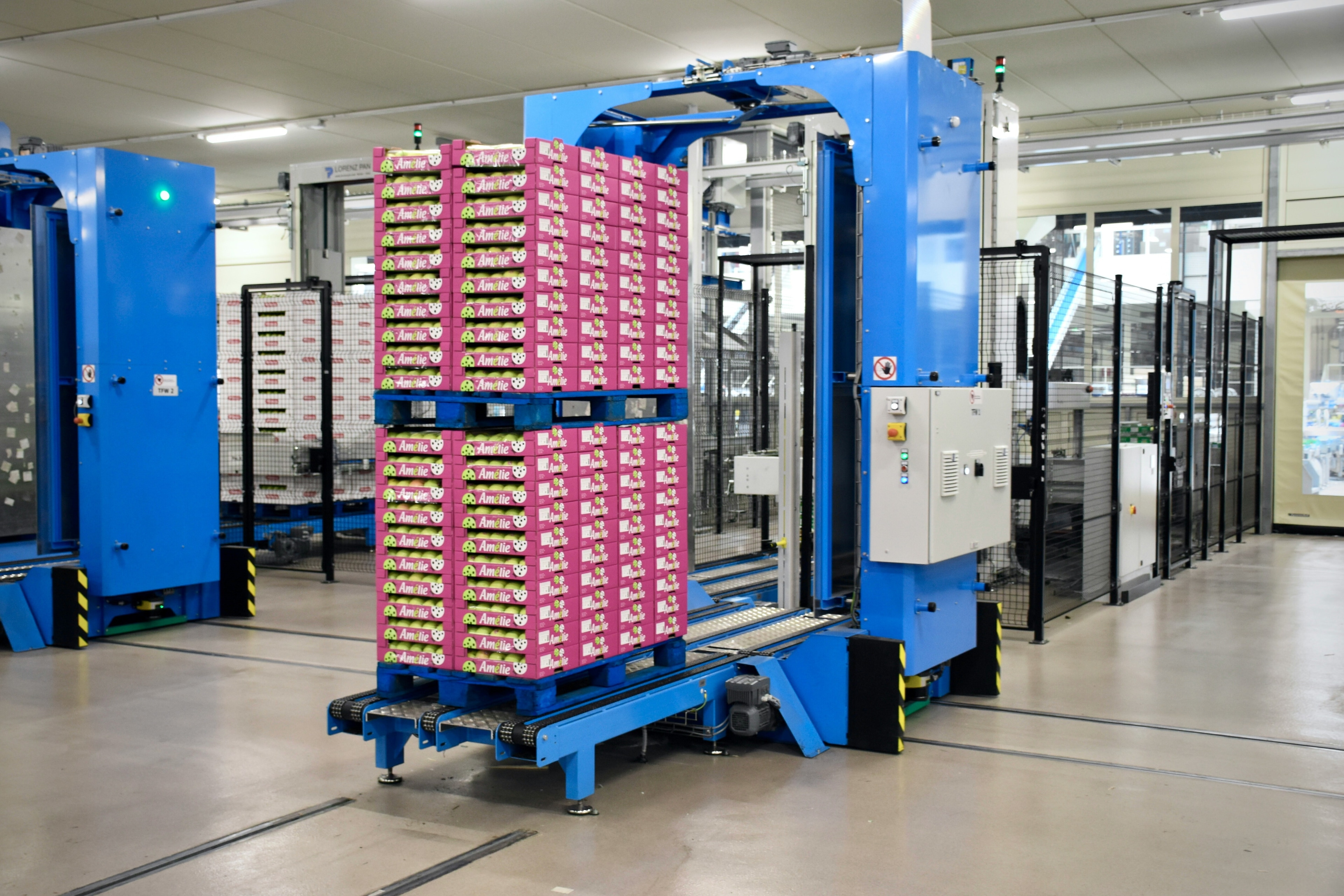
Robotic automation needs a people first approach.
Image: Arno Senoner on Unsplash
Stay up to date:
Future of Work
- Warehouse operators are challenged by labour shortages, an ageing workforce and growing e-commerce demand.
- Robotics is too often an engineering-first discipline, looking only at the physical problems robots can solve without acknowledging that people are critical to successful robot deployments.
- Robots designed to take people into account will make the difference between success and failure in the workplace and these three laws of robot design are the key.
Labour shortages, increased e-commerce demand and an ageing workforce are the new normal for warehouse operations teams. Warehouse managers need to figure out how to do more with less. Naturally, many of them want to know if automation can help.
It can. Robots have become more capable and cost-effective over the past decade. New capabilities in camera-based perception, autonomous navigation and machine learning are helping robots perform useful tasks for people.
But it's still not enough. The difficulties for material handling workers have worsened since autonomous mobile robots (AMRs) began gaining traction. There are over 1 million unfilled positions for hand labourers and material movers in the United States alone, a number that has nearly doubled in the past six years.
Why is this? Robotics is too often an engineering-first discipline, looking only at the physical problems that a robot could solve – e.g., drive from point A to point B – without acknowledging the people in the loop who are critical to successful robot deployments. If a robot isn't designed to be part of a human-robot team, it doesn't have much chance of succeeding in a real workplace.
To counterbalance these engineering-first instincts, I've developed three laws of robot design.
Law 1: Set the proper expectations and deliver on them
Unlike other industries, robotic products are compared to fictional characters; sci-fi specifically. As a result, many people expect a robot to be able to do almost anything people do.
It's not so. Real robots – robots deployed today – have nowhere near human-level skills. But that’s ok. Robots have complementary skills to us. There are tens of millions of Roombas, or robotic vacuum cleaners, in the world today, which were co-invented by my colleague Rodney Brooks. Clearly, robots don’t have to look like C-3PO to be good at getting work done.
Our first law is about setting proper expectations. Robot design should only make promises it can keep. If people and robots are going to work together effectively, then people need to understand what their workplace’s robots can and can’t do, so that they can plan accordingly. As Brooks would say, if the robot has eyes, it had better be able to see.
When a robot is safely operating, it should make people feel safe. No matter how confident the robot is about its collision avoidance system, it still shouldn't startle people by zooming by them too closely or too quickly. Startled people move erratically and unsafely. When a robot is less safely operating (e.g., carrying a heavy payload), it should also make clear to people when they should give the robot more space.
It's easy to think of robot deployment as a pure engineering challenge. However, it’s also a change management challenge, an operations design challenge and a human-robot interaction design challenge. People have the experience, resourcefulness and creativity to develop solutions to problems encountered on the warehouse floor, no matter how new or complex those problems may be.
Law 2: It's not about things - it's about people
Hence, my second law of robot design. Organizations deploy robots to make life better for everyone – to reduce error rates and operating costs for warehouse managers, improve employee engagement and retention and provide better customer satisfaction. To get these benefits, workers have to feel that the robot is truly collaborative, working for them and with them. Robot design needs to tell them and show them, even without words, that the robot isn't there to make people work like machines. People need to be in control and feel that they're in control. This makes employees feel respected and valued. That means better day-to-day work performance, job satisfaction and employee retention.
So, following this people-centred principle, we avoid robot design decisions that will make workers feel they're being rushed, pushed to do things in a 'robotic' way, or otherwise feel like they are cogs in a big machine. Instead, the machine's form, behaviour and role in the workplace reassures workers that their skills are valued.
Law 3: Design for teamwork
Ask a warehouse associate to describe a good day at work and they will probably tell you about getting into a state of 'flow', cranking out orders accurately and on time and working in smooth coordination with their teammates. This requires not getting sidetracked by broken equipment, interpersonal conflict or other workplace distractions.
Robots need to do more than solve narrowly defined problems like 'move these orders to the shipping area.' Instead, we need to design for the broader challenge of making human-robot collaborations efficient, effective and engaging. Keeping people in a flow state means finding and eliminating the friction and breakdowns that can knock a person out of their high-performance mode.
Following this law requires us to see robots as part of an ecosystem that includes people. It's a design philosophy that doesn't begin by asking, 'What job could the robot do?' Instead, we ask, 'What tasks should robots do to make work better for people on this team?' People’s bodies suffer when they perform repetitive physical tasks and when they walk too much across hard warehouse floors. Let’s give robots the work tasks that people don’t want to do. Then let’s design robot behaviors in such a way that the robots show up for people at the right time and in the right way to keep people in flow.
Robotic automation solutions can reduce employee turnover, improve work performance and ultimately address the growing job gap. Designing robots that take people into account will make the difference between success and failure in real-world workplaces.
These three laws of robot design — set the proper expectations and deliver on them; it's not about things, it's about people; and design for teamwork — are the key to making a transition to happier employees, more productive operations and more satisfied customers.
Accept our marketing cookies to access this content.
These cookies are currently disabled in your browser.
Don't miss any update on this topic
Create a free account and access your personalized content collection with our latest publications and analyses.
License and Republishing
World Economic Forum articles may be republished in accordance with the Creative Commons Attribution-NonCommercial-NoDerivatives 4.0 International Public License, and in accordance with our Terms of Use.
The views expressed in this article are those of the author alone and not the World Economic Forum.
Related topics:
Forum Stories newsletter
Bringing you weekly curated insights and analysis on the global issues that matter.
More on Emerging TechnologiesSee all
Michael Donatti and Laura Fisher
July 3, 2025
Benjamin Hertz-Shargel
July 1, 2025
Ravi Kumar S. and Rohan Murty
July 1, 2025
Abayomi Olusunle
July 1, 2025
Stacy Greiner
July 1, 2025
Amged B Shwehdy
June 30, 2025