How modular construction drives productivity, circularity and the convergence of industries
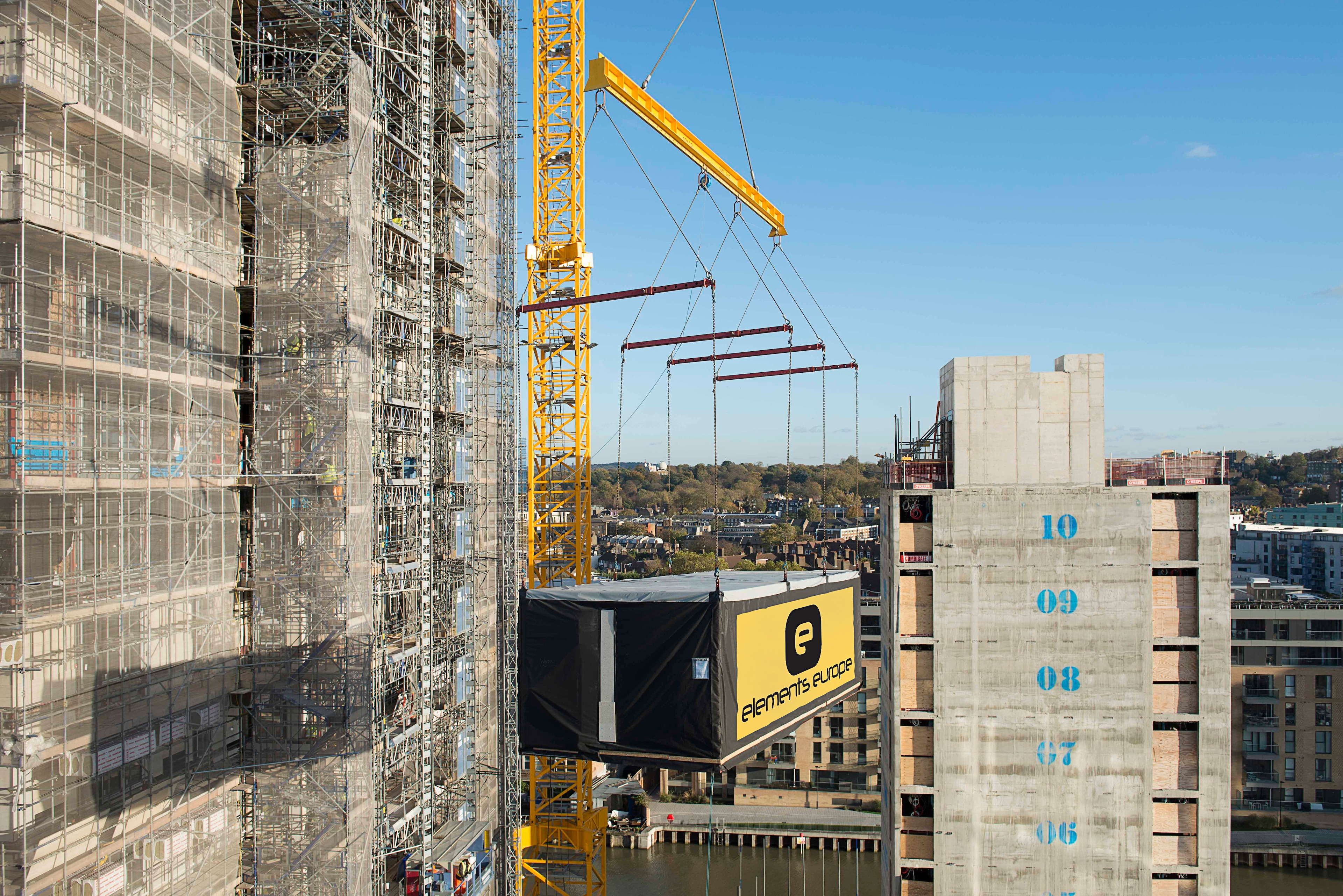
Modular construction is characterized by prefabrication, where components of buildings, usually with standardized designs, are manufactured off-site.
Image: Elements Europe
Stay up to date:
Circular Economy
- Growing trends within the construction industry point towards significant convergence with manufacturing through modular construction.
- Productivity and efficiency gains from shortened project timelines and less disruptive on-site work are some of the advantages of modular construction.
- Circularity in built environments will become more commercially viable in the future with modular construction practices.
The construction industry is often perceived as being stagnant and facing considerable difficulty in making technological progress. This is largely due to its capital-intensive nature and reliance on manual labour and conventional machinery. In response, a more innovative and sustainable path forward is emerging through modular construction — a method of construction that incorporates the advantages of manufacturing into traditional construction practices.
Modular construction is characterized by prefabrication, where components of buildings, usually with standardized designs, are manufactured off-site. The modules are then transported to the construction site to be assembled into full structures. Specific methods of assembly may vary. Panelized construction, for example, involves the manufacturing of panels, such as walls, ceilings and floors that are bolted together and erected at the site, while volumetric construction requires prefabricating three-dimensional room-sized modules that are later stacked and joined together.
What is the World Economic Forum doing on infrastructure?
The benefits of modular construction
Modular construction in itself is not a novel invention. Its roots can be traced back to ancient civilizations in places, such as Egypt and Sri Lanka, where structures were assembled from segments that were crafted separately. Centuries of technological progress, however, have given rise to modular construction that is modernizing the construction industry and paving the way for a more resource-efficient built environment in a few key ways:
1. Improved productivity and efficiency
Despite being the largest emitter of greenhouse gases, the construction industry has been slow in adopting innovations. Modular construction allows structures to be built at a much faster rate compared to traditional construction, revolutionizing the way projects are completed. According to McKinsey & Company, volumetric modular construction can shorten a project timeline by up to 50% by significantly decreasing the amount of work required on-site, as well as cutting various overruns of traditional construction, such as redesigning.
2. Significant project cost savings
Improved efficiency, as well as reduced labour requirements for modular construction, create the potential for significant reductions in project costs. McKinsey & Company predicts that there is potential for up to 20% of total cost savings to be realized through productivity boosts from modular construction methods. While additional costs of logistics and factory operations currently complicate this equation, there is a clear path forward for future optimizations that can translate into real gains in cost efficiency.
3. Improved systems outcomes and community health
Modular construction offers a less disruptive alternative for communities affected by construction, significantly reducing the negative impacts on residents and their surroundings. Let's look at an internal study conducted by Elements Europe, a subsidiary of my company, GS E&C, of its Camp Hill project of 550 residential units of steel modular construction located in Birmingham’s city centre in the UK. The analysis showed that approximately 3,700 fewer deliveries, translating to 56% fewer vehicle movements overall, will be required compared to a traditional construction project of equivalent size and scale. The reduction in vehicles helps alleviate negative consequences, such as traffic congestion and pollution, while improving air quality — an imperative in British urban environments where clean air zones and low emission zones are frequently implemented to safeguard public health.
Modular construction’s role in circular built environments
According to the European Commission, construction is responsible for creating roughly a third of the world’s total waste, as well as producing nearly 40% of the world’s total carbon dioxide emissions. Although construction aims to improve people’s lives through projects ranging from family homes to skyscrapers and public infrastructure, it simultaneously causes unparalleled environmental destruction and significantly harms the planet at a rate unmatched by any other industry.
The future of construction depends on advancing built environments towards circularity — a goal that modular construction can help achieve by enabling the reuse and repurposing of building components, reducing waste and promoting sustainable resource cycles.
Today, there are only a handful of instances – mostly in smaller, non-commercial cases – where building components from permanent structures have been reused or buildings have been reconstructed from existing ones. With the rise of modular construction, however, these can become a foreseeable reality.
Although largely explored at the conceptual level and yet to be profitably implemented, the ability to dismantle and reuse modules instead of demolishing permanent structures presents an exciting opportunity, particularly given the recyclability of building materials and components.
Even without the commercial rise of circular construction methodologies, modular construction has illustrated a significant reduction in carbon footprints. A study of the Camp Hill project’s carbon output has shown approximately a 35% reduction in embodied carbon throughout the project life cycle. With total embodied carbon levels of 915 kgCO₂e/m², the project has moved notably closer to achieving the Royal Institute of British Architects’ world-leading targets on carbon reduction, which includes bringing down embodied carbon levels to <800 kgCO₂e/m².
Modular construction presents a new paradigm for an industry that has struggled to innovate and adapt. In an age of technological advancements and increasingly stricter ESG regulations, modular construction will continue to provide an industry advantage. However, long-term viability and the demand for modular structures will heavily depend on the commercial perspectives of the construction industry and its stakeholders. Beyond cost efficiency and profitability, a strong focus on environmental impact and sustainable innovation must be a key incentive to adopting modular construction practices.
GS E&C is a member of the Davos Baukultur Alliance. This Alliance unites public and private sector stakeholders around a shared set of principles to improve the quality of our living environments, including through scaling circular solutions.
Accept our marketing cookies to access this content.
These cookies are currently disabled in your browser.
Don't miss any update on this topic
Create a free account and access your personalized content collection with our latest publications and analyses.
License and Republishing
World Economic Forum articles may be republished in accordance with the Creative Commons Attribution-NonCommercial-NoDerivatives 4.0 International Public License, and in accordance with our Terms of Use.
The views expressed in this article are those of the author alone and not the World Economic Forum.
Forum Stories newsletter
Bringing you weekly curated insights and analysis on the global issues that matter.
More on Urban TransformationSee all
Jeff Merritt, Charlotte Boutboul and Marc Biosca
July 2, 2025
Pepe Puchol-Salort and Nicole Cowell
June 30, 2025