Millions of tons of plastics from end-of-life vehicles are wasted each year. Here are 4 ways to fix the problem
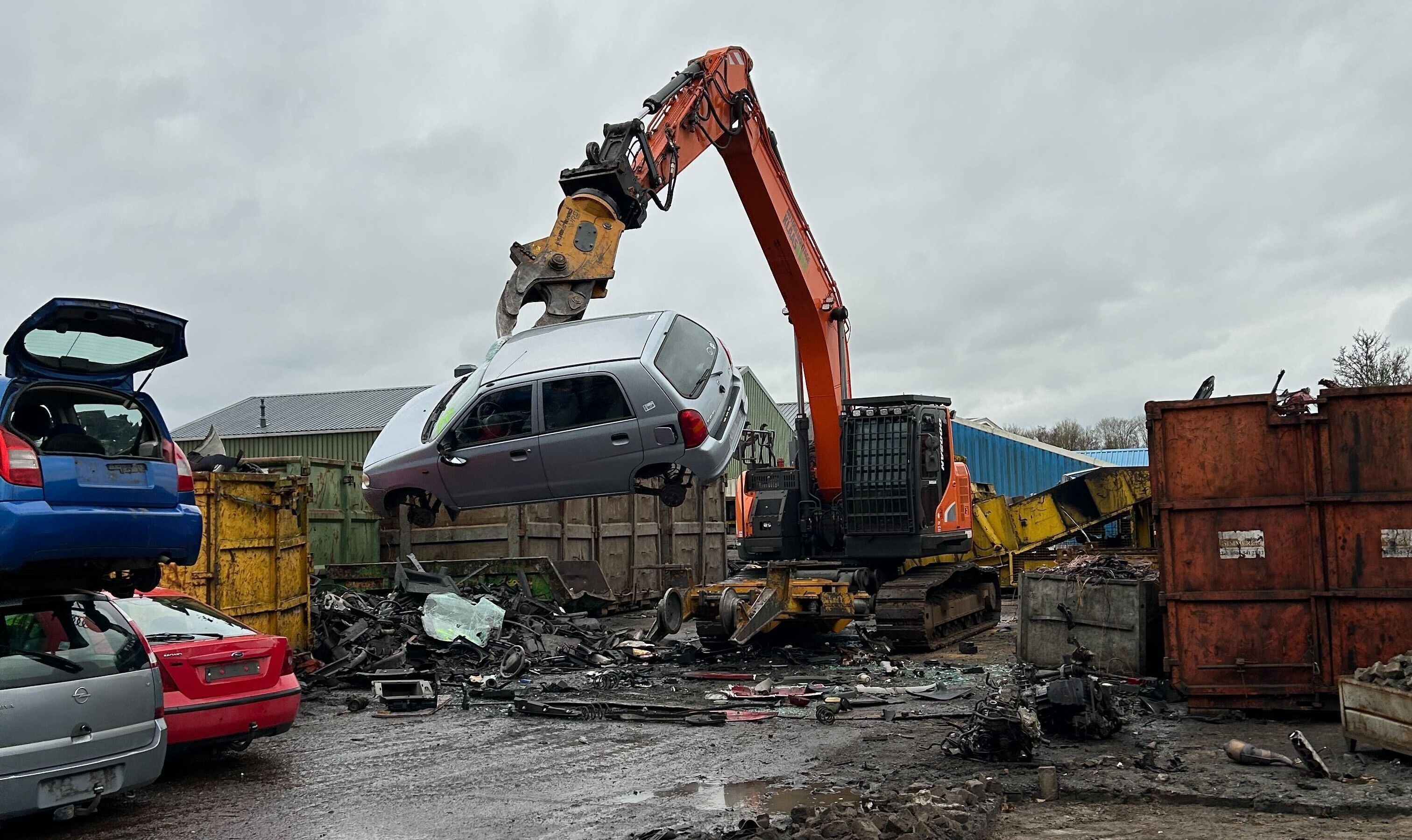
Only 20% of plastics from end-of-life vehicles currently get recycled in Europe.
Image: Davide Del Ben (GIC)
Stay up to date:
Circular Economy
- Over 800,000 metric tons of plastic from end-of-life vehicles in Europe end up in landfills or incinerators each year.
- However, despite the automotive industry’s sustainability commitments, less than 20% of these plastics are recycled.
- The Global Impact Coalition's Automotive Plastics Circularity project is working on recycling ELV plastics more efficiently.
Each year, more than 800,000 metric tons of plastic from end-of-life vehicles (ELVs) in Europe alone end up in landfills or incinerators. Despite the automotive industry’s sustainability commitments, less than 20% of these plastics are recycled today.
This waste represents not just an environmental burden, but a lost opportunity to create a circular economy for automotive plastics in vehicles that have reached the end of their useful life.
Closing the loop on ELV plastics requires a fundamental shift in how we collect, process and value these materials. Four key areas must be addressed to drive real change:
1. Rethinking the value chain: from waste to resource
Unlike metals, which have well-established recovery systems, ELV plastics are often mixed, contaminated or difficult to sort efficiently. To unlock their potential, the industry must shift from treating them as waste to valuing them as a resource.
A key step is sorting plastics at the dismantling stage. Instead of shredding entire vehicles and extracting plastics later, organizing materials by polymer type and part function can improve plastic quality and recyclability.
The Global Impact Coalition (GIC) Automotive Plastics Circularity pilot is pioneering this approach. In this pilot, eight companies – BASF, Covestro, LG Chem, LyondellBasell, Mitsubishi Chemical Group, SABIC, SUEZ, and Syensqo – are collaborating across the chemical industry and with dismantlers, sorters and shredders on a new method to sort, aggregate and process ELV plastics more efficiently.
Accept our marketing cookies to access this content.
These cookies are currently disabled in your browser.
By first clustering plastic parts according to their principal polymer typology, and keeping these clusters separated along the value chain, ELV plastics can be more easily recycled with higher purity levels. This real-world pilot demonstrates how a systemic approach can transform discarded ELV plastics into a high-quality feedstock for new materials.
2. Regulatory incentives: setting the right targets
While voluntary industry commitments help, strong policy frameworks drive investment and innovation at scale. The EU Green Deal is setting a new precedent, proposing End-of-Life Vehicle Regulations that require 25% of plastics in new cars to come from recycled sources by 2030, including a share from closed-loop systems (plastics recovered from ELVs).
For these regulations to be effective, governments and industry can collaborate to:
- Standardize collection and sorting standards across regions
- Help incentivize dismantlers to sort plastics at the source
- Support R&D in advanced recycling solutions
Aligning policy with industry needs can turn sustainability goals into economically viable solutions.
3. Advancing recycling technologies: from limitation to innovation
Traditional mechanical recycling methods have struggled with mixed, contaminated and degraded ELV plastics. However, emerging recycling technologies are changing the game. Advanced sorting systems, chemical recycling and innovative processing techniques can help overcome the technical barriers that have long hindered ELV plastic recovery.
AI-powered sorting technologies can now identify and separate plastics more accurately, enabling closed-loop recycling of hard-to-sort materials like polyolefins. Meanwhile, chemical recycling breaks plastics down to their molecular building blocks, enabling even heavily degraded materials to be turned into virgin-quality polymers.
What is the World Economic Forum doing about plastic pollution?
Many chemical companies are advancing chemical recycling methods to more efficiently recycle end-of-life plastics into new materials.
Deployment of these next generation recycling solutions demonstrates that with the right infrastructure and investment, ELV plastics can be reintegrated into new automotive materials rather than lost to incineration or landfill.
4. Financing circularity: sharing the cost, sharing the benefits
One of the biggest barriers to scaling end-of-life vehicle plastic recycling is economic feasibility. Unlike metals, which have well-established markets, recycling plastics from ELVs is currently more costly than using virgin materials. To bridge this gap, new cost-sharing models are needed, including:
- Extended producer responsibility (EPR) schemes such as France’s vehicle EPR system under the AGEC law.
- Pooling investments in centralized sorting and recycling hubs to improve economies of scale, as seen in the GIC pilot on automotive plastics circularity.
- Public-private partnerships to support infrastructure development, such as the work done by the World Economic Forum in Transitioning Industrial Clusters.
By distributing costs across the entire value chain, the industry can create a financially sustainable system where recyclers and dismantlers are not left to bear the burden alone.
A 2021 report by the World Economic Forum and Boston Consulting Group, Net-Zero Challenge: The Supply Chain Opportunity, found that fully decarbonizing a mid-size family car would increase its total cost by less than 2% – provided the burden is distributed across the entire value chain.
Have you read?
However, the heaviest cost impact occurs upstream, particularly in metal production, where steel alone could see prices rise by nearly 40%, straining the lowest-margin stage of the process. This highlights the need for a systemic, value chain-wide approach to ensure the costs of decarbonization are shared equitably.
A circular future for automotive plastics
Transitioning from wasteful disposal to circular recovery is both possible and necessary, and collaboration, policy support, financial investment and technological innovation will prove pivotal in driving this shift.
With initiatives like the GIC Automotive Plastics Circularity project leading the way, the question is no longer if automotive plastics can be recycled at scale but how quickly the industry can work together to make it happen.
By rethinking how ELV plastics are valued, sorted, regulated and financed, we can move toward a future where millions of tonnes of automotive plastics are no longer wasted but instead fuel a thriving circular economy.
Accept our marketing cookies to access this content.
These cookies are currently disabled in your browser.
Don't miss any update on this topic
Create a free account and access your personalized content collection with our latest publications and analyses.
License and Republishing
World Economic Forum articles may be republished in accordance with the Creative Commons Attribution-NonCommercial-NoDerivatives 4.0 International Public License, and in accordance with our Terms of Use.
The views expressed in this article are those of the author alone and not the World Economic Forum.
Forum Stories newsletter
Bringing you weekly curated insights and analysis on the global issues that matter.
More on Circular EconomySee all
Poonam Watine and Tim van den Bergh
April 22, 2025
Ellen de Ruiter
April 10, 2025
Henrik Hvid Jensen
April 3, 2025
Yair Reem
March 25, 2025
Fernando J. Gómez and Wesley Spindler
March 24, 2025
Antonio Gómez-Palacio
March 17, 2025